Royal Arc Electrodes coming with IPO to raise Rs 36 crore
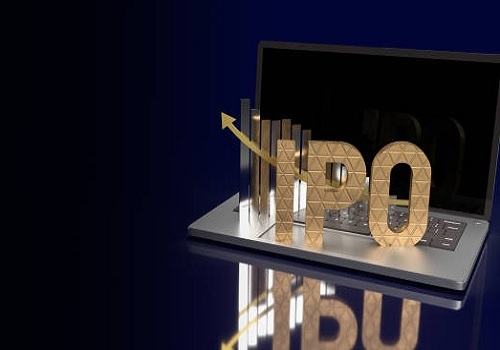
Royal Arc Electrodes
- Royal Arc Electrodes is coming out with an initial public offering (IPO) of 30,00,000 equity shares in a price band Rs 114-120 per equity share.
- The issue will open on February 14, 2025 and will close on February 18, 2025.
- The shares will be listed on SME Platform of NSE.
- The face value of the share is Rs 10 and is priced 11.40 times of its face value on the lower side and 12.00 times on the higher side.
- Book running lead manager to the issue is Fedex Securities.
- Compliance Officer for the issue is Mansi Bagadiya.
Profile of the company
Incorporated in 1996, Royal Arc Electrodes is engaged in the business of manufacturing of welding consumables such as, welding electrodes, flux cored wire, MIG/TIG wires, which finds its application in the welding of tanks, boilers, heavy structures, beams, pipes, cylinders, pressure vessels, etc. which are used in industries like railways, roadways, airport infrastructure, refineries, shipyards, mines, sugar industries, telecom industries, thermal power stations, PEB sectors, etc. Further, the company is also engaged in the business of trading of ancillary/incidental products like wheels, electro slag, welding flux cored wire, electro slag strip cladding, saw flux and TIG /MIG wires.
It manufactures its products from copper coated wire, MS Strips, MS wire, SS strip, SS wire, nickel wire, ferro alloy powder, etc. conforming to international standards, from its highly sophisticated and technically competent manufacturing facility spread over an area of 25082.61 sq. mtr which is situated at Zaroli, Umbergaon Valsad, Gujarat, Bharat. At its manufacturing facility, the raw materials undergo through a process of wire drawing and cutting, powder mixing, covering and baking. Accordingly, its existing manufacturing plant consists of extrusion units, baking ovens, drawing units, cutting units, forming mills, powder mixers, packing machines and testing labs.
The company has the necessary instruments such as, chemical analysis instrument, spectro-meter, material testing lab equipment and is backed by related quality assurance equipment’s for measuring chemical and mechanical properties along with their sizes and shapes of its raw materials and finished goods to match international and domestic standards as well as customer specifications. Its manufacturing facility is also accredited with ISO 9001:2015 certified by DNV - Business Assurance.
Proceed is being used for:
- Funding towards the expansion of its manufacturing facility situated at Village Zaroli, Umbergaon Valsad, Gujarat, Bharat
- Funding the working capital requirements of the company
- General corporate purposes
Industry Overview
By 2030, the Indian government expects the electronics manufacturing sector to be worth $300 billion. Initiatives like Make in India, Digital India and Startup India have given the much needed thrust to the Electronics System Design and Manufacturing (ESDM) sector in India. Moreover, the government’s endeavors such as Modified Special Incentive Scheme (M-SIPS), Electronics Manufacturing Clusters, Electronics Development Fund and National Policy on Electronics 2019 (NPE 2019) have been a huge success. India's electronic manufacturing sector is projected to reach around $ 50 billion in the next five years, driven by technological advancements like 5 G and the Internet of Things (IoT). Currently, electronic exports stand at $125 to $130 billion, with the government aiming to double employment in the sector from 2.5 million jobs.
The machine tools market is expected to reach $3.2 billion by 2032, exhibiting a growth rate (CAGR) of 8.2% during 2024-32. The Indian machine tool market size reached $1.5 billion in 2023. The emerging trend of automation, along with the growing utilization of machine tools to increase the overall productivity and improve the efficiency of various products, is primarily driving the India machine tools market. The manufacturers of machine tools are mostly SMEs, few of them are mid-sized manufacturers which have an annual turnover varying between Rs 300-500 crore ($36-60 million). The types of machine tools currently manufactured are general/special purpose machines, standard Computer Numerical Control (CNC) machines, gear cutting, grinding, medium size machines, electrical discharge machining (EDM), presses, press brakes, pipe bending, rolling, bending machines, etc.
The electrical equipment market share in India is expected to increase from $52.98 billion in 2022 to $125 billion by 2027, implying a robust CAGR of 11.68%. Market size for the Indian Construction Equipment Market stood at $7.2 billion in FY23 and is forecasted to grow at a CAGR of 15% for next 5 years, as per the estimates of CII. Export policy is being established for the State of Uttar Pradesh to tap onto opportunities in international market, optimum utilization of the resources of the state, employment generation and to synergize with the Foreign Trade Policy 2020-25. The objective of this policy is to promote development and competition in the field of exports, to provide necessary export-related assistance and services to export ancillary institutions, to establish and develop technical and physical infrastructure to increase exports from the state. Further, the PLI Scheme for the automobile and auto components industry has been launched with a total budgetary outlay of Rs 25,938 crore ($3.17 billion) for a period of 5 years (FY23 to FY27).
Pros and strengths
Geographically spread across Bharat and overseas market: The company sells its products across various states in Bharat with a diverse customer base through its network of dealers and distributer and also directly to its end customers. It also has a sales and marketing team of 9 employees as at December 31, 2024, who aid the distribution process and are primarily engaged in distributor/dealer relationship management, appointment of dealers and distributors, procuring orders and collections. Its geographical widespread across Bharat have enabled it to cater to the growing demand for its products.
Long-standing relationships with customers across industries: The company has over 2.5 decades of business operations and have been engaged in the business of welding consumables since its incorporation. Over the years, it has a supplied its products to a diversified customer base such as, railways, roadways, airport infrastructure, refineries, shipyards, mines, sugar industries, telecom industries, thermal power stations, PEB sectors, etc. Its focus on quality, providing customized solutions to its customers and timely delivery of its product offerings have helped it to establish and maintain long term relationships with its customers.
Consistent financial performance: Over the years, the company has grown into a multi-product welding consumable manufacturing company. It has demonstrated consistent growth in terms of revenues and profitability. Its revenue from operations has grown from Rs 6,290.97 lakh in Fiscal 2022 to Rs 9,978.75 lakh in Fiscal 2024, registering a CAGR of 25.94%. Its PAT has grown from Rs 212.13 lakh in Fiscal 2022 to Rs 1,192.63 lakh in Fiscal 2024, registering a CAGR of 137.11%. It has been able to maintain its consistent financial growth, due to efficient business model over the years. It strives to maintain a robust financial position with emphasis on having a strong balance sheet and cash flows.
Risks and concerns
Significant revenue comes from limited customers: The company is dependent on a limited number of customers for a significant portion of its revenues. The company has garnered 44.19%, 44.68% and 53.40% of its total revenue from top 10 customers in FY24, FY23 and FY22 respectively. While it has developed long-term relationships with certain of its customers, there is no commitment on the part of its key customers to continue to place new purchase orders with it and as a result, its cash flow and consequent revenue may fluctuate significantly from time to time. Further, it may not find any other customers for the surplus or excess capacity, in which case it may be forced to incur a loss. The loss of one or more of these significant customers or a significant decrease in business from any such key customer may materially and adversely affect its business, results of operations and financial condition.
Single manufacturing facility: The company sole manufacturing facility is located at Umbergaon, District Valsad, Gujarat. Further, the expansion will be constructed on the land where its existing manufacturing facility is situated. Any material adverse social, political or economic development, natural calamities, civil disruptions, or changes in the policies of the state government or local governments in this region could adversely affect its manufacturing operations, and require a modification of its business strategy, or require it to incur significant capital expenditure or suspend its operations.
Significant working capital requirements: The company’s business requires significant working capital in connection with manufacturing of its products, financing inventory, day-to-day operations, amongst other purposes which may be adversely affected in case there is any change in terms of credit or payment. Delays in payment from its existing customers or any increase in inventory and work in progress and/or accelerated payments to suppliers, could adversely affect its working capital, lower its cash flows and materially increase the amount of working capital requirements. Accordingly, it may require additional capital or financing from time to time to meet its working capital requirements.
Outlook
Royal Arc Electrodes is engaged in the business of manufacturing of welding consumables such as, welding electrodes, flux cored wire, MIG/TIG wires. The company is used welding consumables for welding tanks, boilers, heavy structures, beams, pipes, cylinders, pressure vessels, and more, across industries such as railways, roadways, airports, refineries, shipyards, mining, sugar, telecom, thermal power stations, and PEB sectors. On the concern side, the company derived a significant portion of its revenue from a few customers and the loss of one or more such customers, the deterioration of their financial condition or prospects, or a reduction in their demand for its products may adversely affect its business, results of operations, financial condition and cash flows. Moreover, the company operates only one manufacturing facility and therefore, any localized social unrest, natural disaster, or breakdown of services, in and around its manufacturing facility or any disruption in production at, or shutdown of its manufacturing facility could have a material adverse effect on its business and financial condition.
The company is coming out with a maiden IPO of 30,00,000 equity shares of Rs 10 each. The issue has been offered in a price band of Rs 114-120 per equity share. The aggregate size of the offer is around Rs 34.20 crore to Rs 36.00 crore based on lower and upper price band respectively. On performance front, the revenue from operations marginally increased by 2.94% to Rs 9,978.75 lakh for the Fiscal 2024 from Rs 9,694.02 lakh for the Fiscal 2023. Moreover, the company recorded an increase of 24.65% in its profit for the year from Rs 956.82 lakh in Fiscal 2023 to Rs 1,192.63 lakh in Fiscal 2024.
The company has over the years increased its production capacities through consistent growth and innovation. The company commenced manufacturing of welding consumables of welding electrodes and flux cored wire with an installed capacity of 18,000 MTPA in its manufacturing unit situated at Umbergaon Valsad, Gujarat. In order to capture the market and cater to the growing demand, in the year 2003, it increased its manufacturing capacity and thereafter it further expanded its manufacturing facility in 2014 spread over around 25082.61 sq. mtr. Its strong presence in the Indian market positions it well to capitalise on the anticipated growth in demand of its products. It intends to expand the manufacturing capacity by establishing a new factory shed in the same premises as its manufacturing facility, which will increase the present capacity and subsequently boost its sales and profitability.

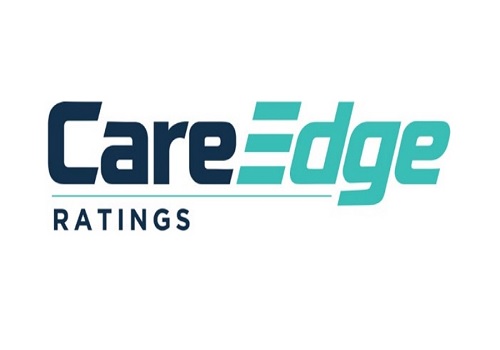
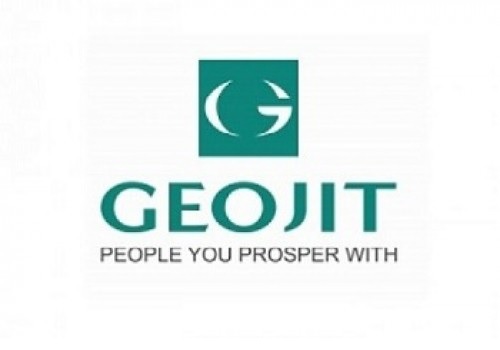
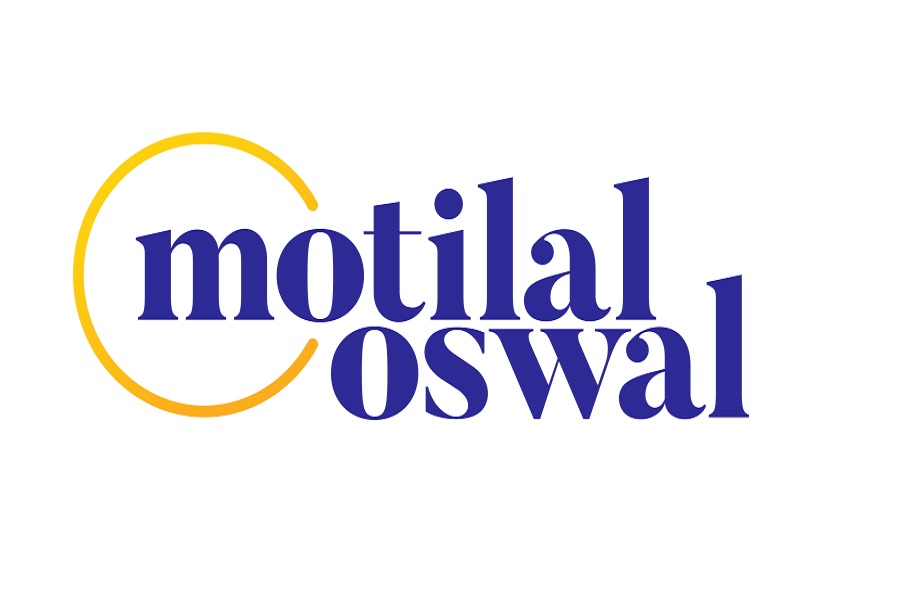




