Borana Weaves coming with IPO to raise upto Rs 145 crore
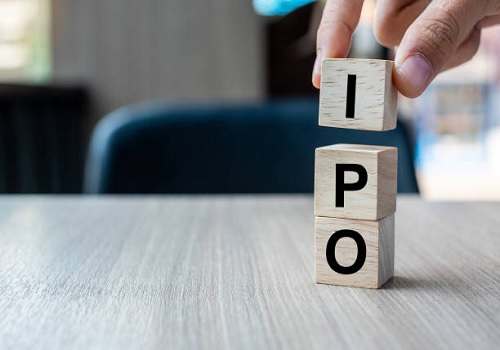
- Borana Weaves is coming out with a 100% book building; initial public offering (IPO) of 67,08,000 shares of Rs 10 each in a price band Rs 205-216 per equity share.
- Not more than 75% of the issue will be allocated to Qualified Institutional Buyers (QIBs), including 5% to the mutual funds. Further, not less than 15% of the issue will be available for the non-institutional bidders and the remaining 10% for the retail investors.
- The issue will open for subscription on May 20, 2025 and will close on May 22, 2025.
- The shares will be listed on BSE as well as NSE.
- The face value of the share is Rs 10 and is priced 20.50 times of its face value on the lower side and 21.60 times on the higher side.
- Book running lead manager to the issue is Beeline Capital Advisors.
- Compliance Officer for the issue is Seema Luniya.
Profile of the company
Borana Weaves is a textile manufacturer based in Surat, specializing in the production of unbleached synthetic grey fabric. This fabric serves as a fundamental material for further processing, such as dyeing and printing, in various industries, including fashion, traditional textiles, technical textiles, home decor, and interior design. The versatility of grey fabric allows it to complement a wide range of unbleached fabrics across different styles, making it a valuable resource in the textile supply chain. In addition to grey fabric, the company also manufactures polyester textured yarn (PTY Yarn), which is produced by heating polyester oriented yarn (POY Yarn), its raw material used in the production of grey fabric.
The company commenced its operations in 2020, and the production from its first unit, Unit 1 located at Hojiwala Industrial Estate, SUSML, Surat, Gujarat, was subsequently started in 2021. Currently, the company operates three manufacturing units in Surat, Gujarat, equipped with textile manufacturing technologies for, inter alia, texturizing, warping, water jet looms, and textile folding.
Most of the manufacturing and processing in its units are carried out using textile manufacturing technologies, pollution light machinery and tools which are supplied by domestic and global players in the synthetic fibre industry. As of December 31, 2024, the company had a total of 15 texturizing machines, 6 warping machines, 700 water jet looms and 10 folding machines active at its three units.
Proceed is being used to:
- Proposing to finance the cost of establishing a new manufacturing Unit to expand its production capabilities to produce grey fabric at Surat, Gujarat, India (Proposed Unit 4)
- Funding incremental working capital requirements
- General corporate purposes
Industry Overview
India is currently one of the largest manufacturers of readymade garments and amongst the largest exporters as well. Domestic market for readymade garments too has grown at a fast pace helping India emerge as one of the fastest growing and lucrative readymade garment markets in the world. Apparel manufacturing alone provides employment to a population of 12.3 million. Domestic demand in the last years witnessed a slowed down as consumers paired down their discretionary spending on the wake of economic uncertainty. Exports too suffered the same fate as recessionary scenario in key export markets - US and EU - dampened demand for readymade garments in those markets.
Synthetic fabrics are man-made textiles produced from chemical processes. These fabrics are derived from synthetic fibers such as polyester, nylon, acrylic, and spandex, which are made by polymerizing small molecules into long chains. Synthetic fabrics are widely used in various industries, including fashion, home furnishings, and industrial applications, due to their durability, versatility, and cost-effectiveness. In the fiscal year 2018-19, production of Synthetic fabrics was robust at 95,897 thousand metric tons. However, this was followed by a slight decline in 2019-20 to 92,452 thousand metric tons. The downturn continued into 2020-21, with production dropping to 83,296 thousand metric tons, a trend attributed to the global disruptions caused by the COVID-19 pandemic. Despite these challenges, the industry showed resilience, with a Compound Annual Growth Rate (CAGR) of approximately 5.19% over the period from 2018-19 to 2023-24, reflecting a steady recovery and growth trajectory.
Recent advancements in fabric technology have enhanced the quality and performance of synthetic textiles. Innovations such as moisture-wicking, breathability, and eco-friendly production processes have increased the appeal of synthetic garments to consumers. Despite historical criticisms regarding environmental impact, there is a growing interest in sustainable synthetic textiles, such as recycled polyester, which aligns with the rising consumer demand for eco-friendly fashion options. The influence of global fashion trends, particularly from Western markets, has also played a significant role in shaping the popularity of synthetic garments in India.
Pros and strengths
Well positioned to capitalize on the growing demand of unbleached synthetic grey fabric: The company is a textile manufacturer based in Surat, specializing in the production of unbleached synthetic grey fabric. This fabric serves as a fundamental material for further processing, such as dyeing and printing, in various industries including fashion, traditional textiles, technical textiles, home decor, and interior design. The versatility of grey fabric allows it to complement a wide range of unbleached fabrics across different styles, making it a valuable resource in the textile supply chain. It is well positioned to capitalize on the growing demand in this sector. Its presence in the industry allows it to leverage the expertise of its Promoters and manufacturing capabilities to meet the needs of its customers.
Investment in water jet looms capable of producing uniform textured fabric: Water jet looms offers significant advantages over traditional power looms in the manufacturing of synthetic grey fabric. The adoption of water jet looms presents significant benefits in the production of synthetic grey fabric. These machines offer greater precision in the weaving process, resulting in fabric that exhibits uniform texture and consistent quality. Unlike traditional power looms, which may require more mechanical components and labour-intensive setups, water jet looms can operate at higher speeds with reduced downtime. This efficiency enhances the ability to meet larger production demands without compromising on quality. Additionally, the water jet technology places less tension on the polyester textured yarn, decreasing the likelihood of breakage during weaving. This results in fewer interruptions in the production cycle, lower waste generation, and a more streamlined manufacturing process compared to traditional methods.
Delivering strong financial and operating metrics: The company has organically grown its operations and has demonstrated an increase in revenues and profitability. The company’s revenue from operations grew at a CAGR of 116.84% from Rs 4,233.40 lakh in Fiscal 2022 to Rs 19,905.56 lakh in Fiscal 2024, based on its Restated Financial Information. The company’s restated profit after tax margin was 13.85%, 11.85%, 12.04%, 4.25% in the nine months period ended December 31, 2024 and during Fiscals 2024, 2023 and 2022, respectively.
Experienced Promoters: The company attributes its growth to the experience of its Promoters. Its Promoter and Chairman and Managing Director, Mangilal Ambalal Borana has over 24 years of experience in textiles industry and has been responsible in augmenting relationships with various stakeholders which has helped the company expand its operations. He is also currently associated as a director with Borana Filaments Private Limited which is involved in manufacturing and processing industrial and synthetic fabrics, yarns, including cotton, wool, silk, nylon, polyester, and other fibrous materials. It also undertakes services like twisting, texturizing, dyeing, bleaching, printing, and processing of man-made and natural fibres in various forms.
Risks and concerns
Geographical constrain: The company’s customers are pre-dominantly based in South Gujarat, more than 98% of its revenue from its customers being derived from customers based in Gujarat, as of December 31, 2024. A decrease in business from its customers due to any adverse market conditions or the economic environment generally prevailing in the state or any neighboring state or region, may adversely affect its business, results of operations, cash flows and financial condition. The concentration of its customer base in Gujarat also exposes it to risks arising from fluctuations in the political, economic, and weather conditions of the state, as well as regional natural or man-made disasters that may disrupt operations.
Limited operating history: The company was incorporated in October 2020 and the production from its first unit, Unit 1 in Surat, was subsequently started in 2021. While it attributes its growth to the experience of its Promoters who have been associated with entities in the textile manufacturing sector that form part of its Promoter Group or Group Companies, such as, Borana Filaments Private Limited and R & B Denims Limited, it has a significantly limited operating history. Accordingly, investors are cautioned against placing undue reliance on the robust growth in its business operations and the significant improvement in its financial performance in such periods. It may not be familiar with the operations of its manufacturing units or the business, which may adversely affect its financial conditions and results of operations.
Maximum revenue comes from sale of Grey fabric: The company’s business is heavily dependent on the sale of grey fabric, which had contributed to 84.24% of its revenue from operations in the nine months ended December 31, 2024. The demand for grey fabric is closely tied to the performance of end industries such as apparel and home textiles. Any downturn in these sectors, either due to seasonal trends, changing consumer preferences, or economic conditions, could lead to reduced orders for grey fabric. Further, grey fabric prices are subject to fluctuation due to various factors such as changes in the prices of raw material, POY Yarn, exchange rate variations, and transportation costs. A reduction in prices could erode its profit margins, and a failure to pass on these cost changes to customers could adversely affect its financial performance.
Require significant financing to support growth strategies: The company requires a substantial amount of capital to build and maintain its manufacturing units, purchase equipment and machineries, implement new technologies in its new and existing plants and facilitate its expansion plans. Its ability to arrange financing and the costs of capital of such financing are dependent on numerous factors, including general economic and capital market conditions, existing terms under its financing agreements, credit availability from banks, investor confidence, the continued success of its operations and other laws that are conducive to its raising capital in this manner. If it decides to meet its capital requirements through debt financing, it may be subject to certain restrictive covenants. If the company is unable to obtain such financing in a timely manner, at a reasonable cost and on acceptable terms, it may be forced to delay its expansion plans, downsize or abandon such plans, which may materially and adversely affect its business, financial condition and results of operations, as well as future prospects.
Outlook
Borana Weaves is a manufacturer of unbleached synthetic grey fabric based in Surat, Gujarat. The company's unbleached synthetic grey fabric is often widely used as a base for further processing (including dyeing and printing) in industries such as fashion, traditional textiles, technical textiles, home decor, interior design, etc. Currently, the company had a total of 15 texturizing machines, 6 warping machines, 700 water jet looms, and 10 folding machines active at its three units. On the concern side, 98% of the company’s revenue comes from its customers based in Gujarat and it does not have long-term agreements with them. Any changes or cancellations of purchase orders from them or its inability to forecast demand for its products may adversely affect its business, results of operations and financial condition.
The issue has been offering 67,08,000 shares in a price band of Rs 205-216 per equity share. The aggregate size of the offer is around Rs 137.51 crore to Rs 144.89 crore based on lower and upper price band respectively. Minimum application is to be made for 69 shares and in multiples thereon, thereafter. On performance front, the company’s revenue from operations increased by 47.01% from Rs 13,539.90 lakh in Fiscal 2023 to Rs 19,905.56 lakh in Fiscal 2024. This increase is primarily attributed to revenue generated from its sales of products and due to increase in installed capacity and actual production of its products. The company’s profit for the year increased by 44.69% to Rs 2,358.64 lakh for Fiscal 2024 from Rs 1,630.09 lakh for Fiscal 2023.
The Indian market is experiencing a notable shift towards synthetic textiles, driven by their affordability, durability, and ease of maintenance. Current demand for polyester in India stands at approximately 4 million tonnes and is projected to rise to 6.7 million tonnes by 2025, indicating a growing consumer preference for synthetic materials. With the global end-use market for man-made fibers expected to expand by 3.7% by 2025, the Indian synthetic textile industry is well-positioned to benefit, with growth opportunities in both domestic consumption and exports. The demand for synthetic textiles has been expanding into various non-apparel applications due to their distinct properties and benefits. The company is well positioned to capitalize on the growing demand in this sector. The increasing preference for synthetic fabrics across various industries such as fashion, sportswear, home decor, and traditional textiles presents substantial growth opportunities.

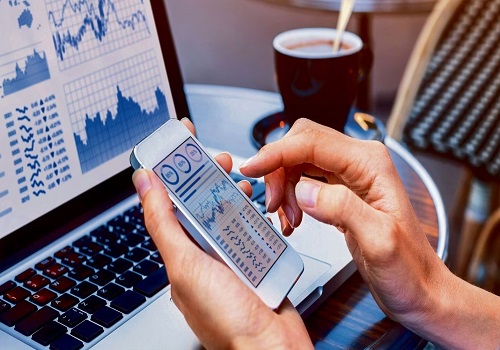

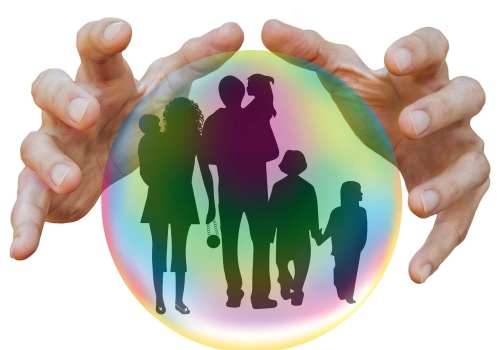
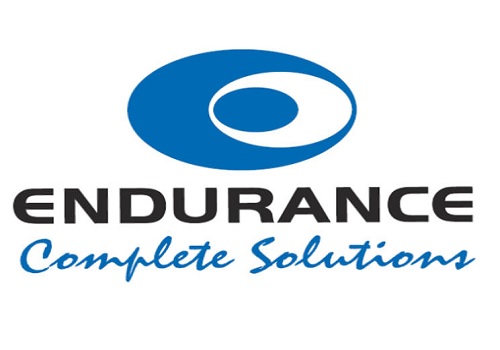


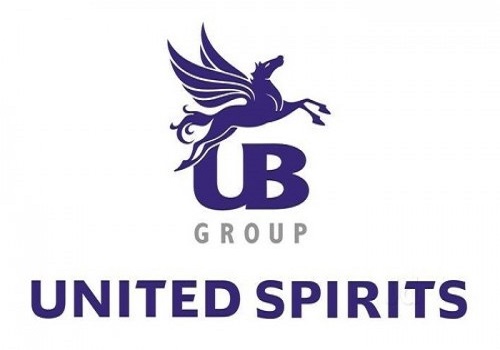

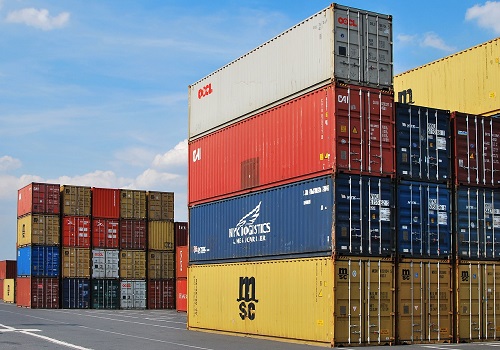