Maini Precision Products and L3Harris ink deal for aircraft ejector release units
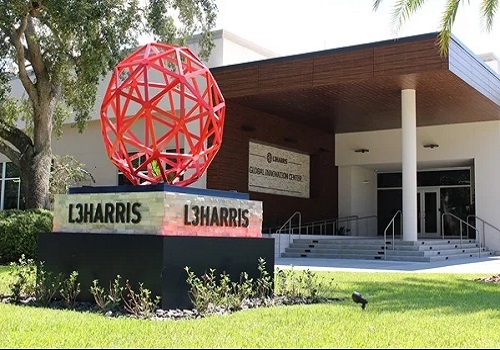
Follow us Now on Telegram ! Get daily 10 - 12 important updates on Business, Finance and Investment. Join our Telegram Channel
US-based L3Harris Technologies and Maini Precision Products Limited (MPP), Bengaluru, have signed a teaming agreement for manufacture of aircraft ejector release units (ERUs), at the Aero India 2023 here on Tuesday.
Under the terms of the agreement, L3Harris and MPP will localise the ERUs in a phased manner, as well as set up an MRO facility in India. The definitive objective of the partnership is to jointly offer 'life of type' support with maximum localisation.
A Make in India project, the ERUs will be suitable for various prestigious Indian aircraft programmes including the Light Combat Aircraft Mark 2 and the Advanced Medium Combat Aircraft.
Approved by the US government for safety features and crew interface even when pressurised, the ERUs feature advanced technology compared to other contemporary ERUs. This partnership is expected to give a boost to the 'Aatmanirbhar Bharat' programme.
Speaking at the signing ceremony, Gautam Maini, Managing Director, MPP, said, "The signing of the teaming agreement between L3Harris and the Aerospace Division of MPP stands testament to the 19 years of our focus on ensuring quality and working to provide high-tech solutions for our partners and customers in the Aerospace industry.
"Working with a global organisation like L3Harris to localise manufacturing, repair and overhaul high technology products will facilitate MPP's principle of Make in India and for the World' and provide life of type support to the Indian aircraft programmes."
The ERUs offered by L3Harris and MPP will be designed with integral bottles, offering several advantages over the external bottle concept, including being designed as fit-and-forget ERUs with a zero-maintenance requirement on the part of operators, resulting in significant savings in life cycle costs as well as substantial ease in day to day and combat operations.
Additionally, integral bottle management has no requirement for logistics, unlike an external bottle approach. Pylon integration is also simplified since access doors or brackets are not required in the pylon design, and pneumatic tubes do not need to be routed from ERUs to pylons. These design features enable faster and safer re-arming operations for loading crews and the ability to carry a wider array of weapons.
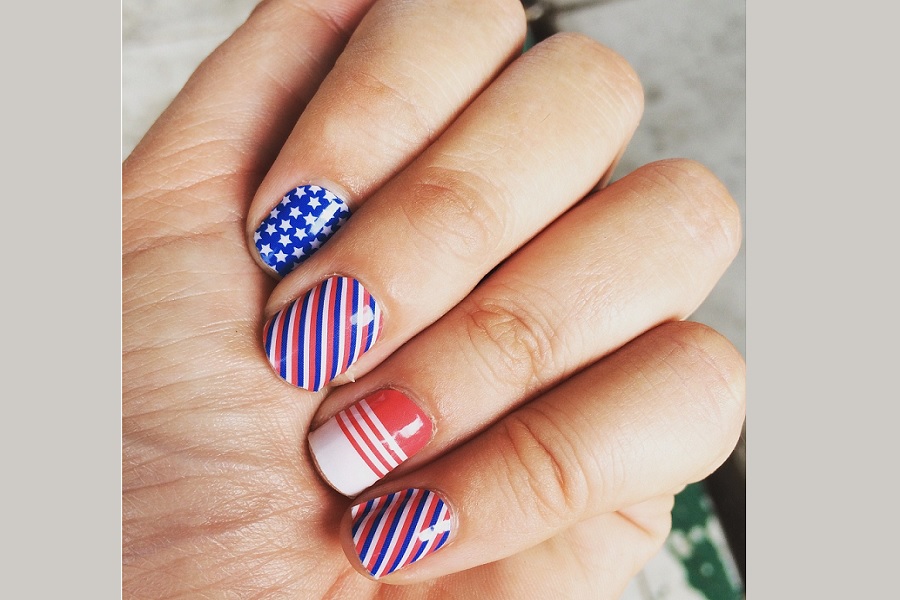
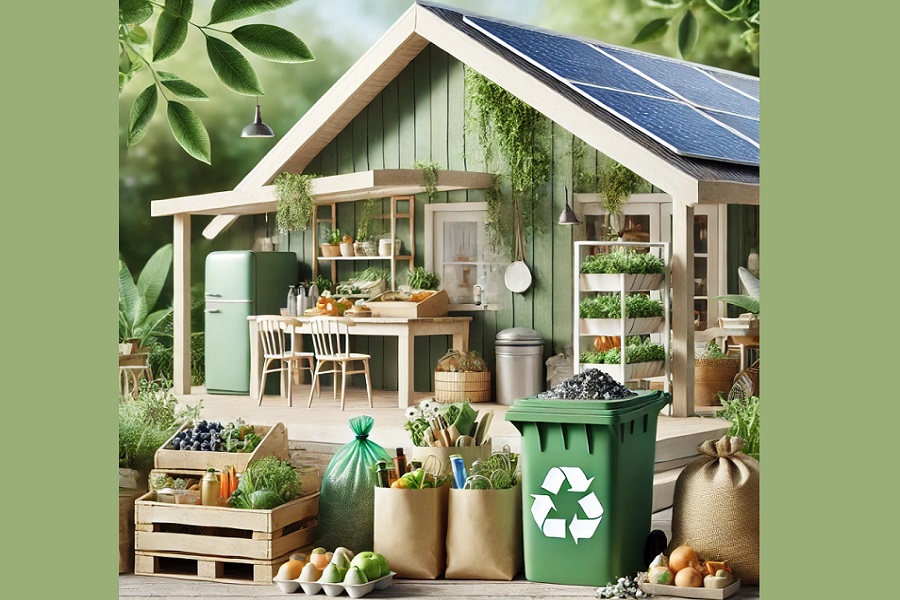
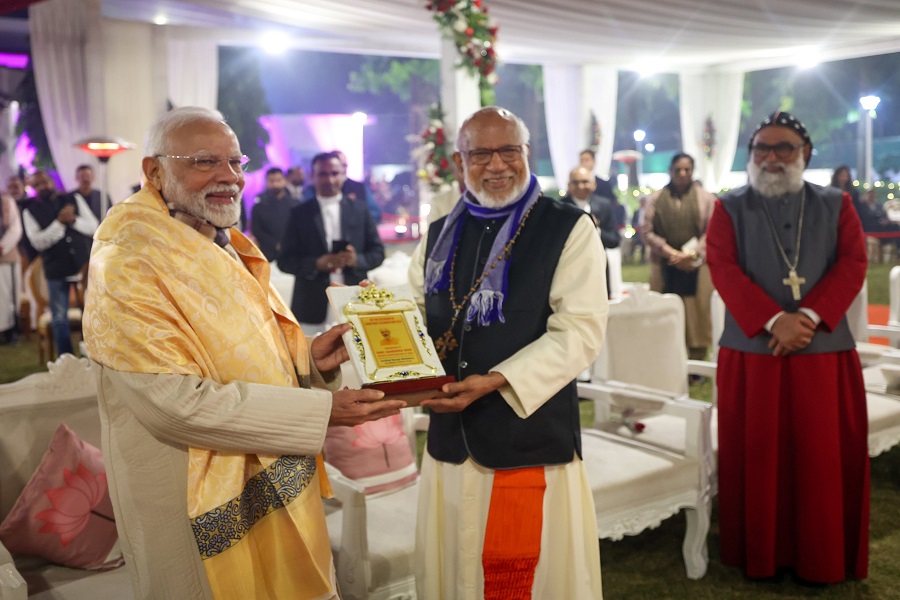
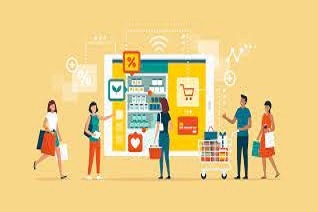

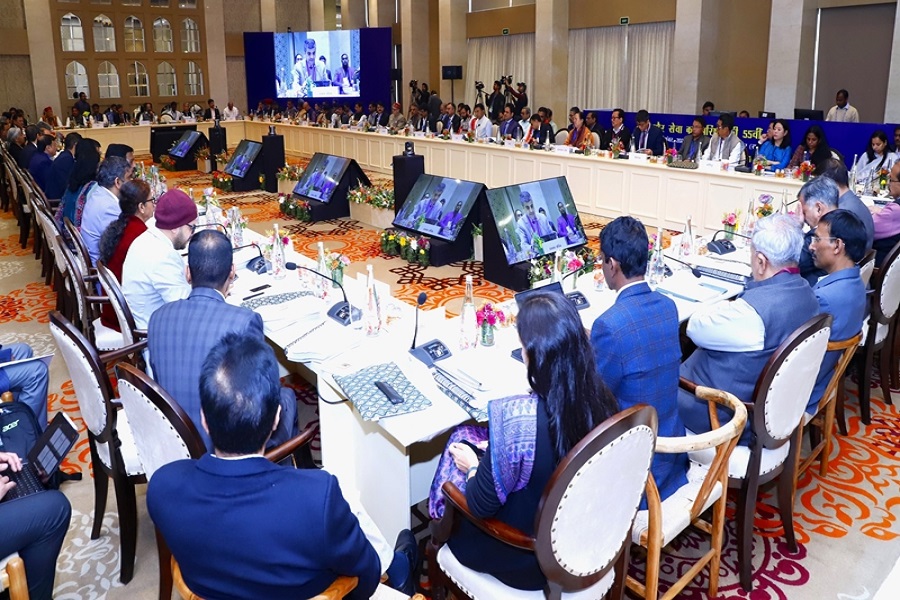
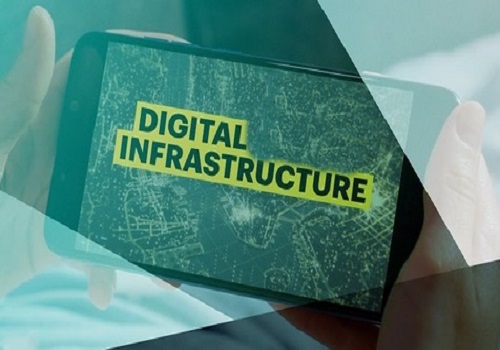
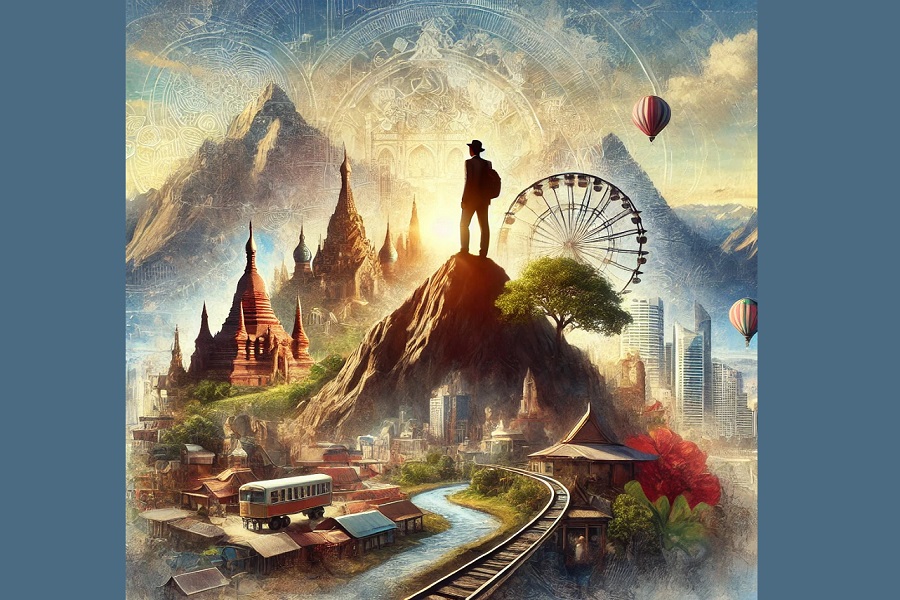
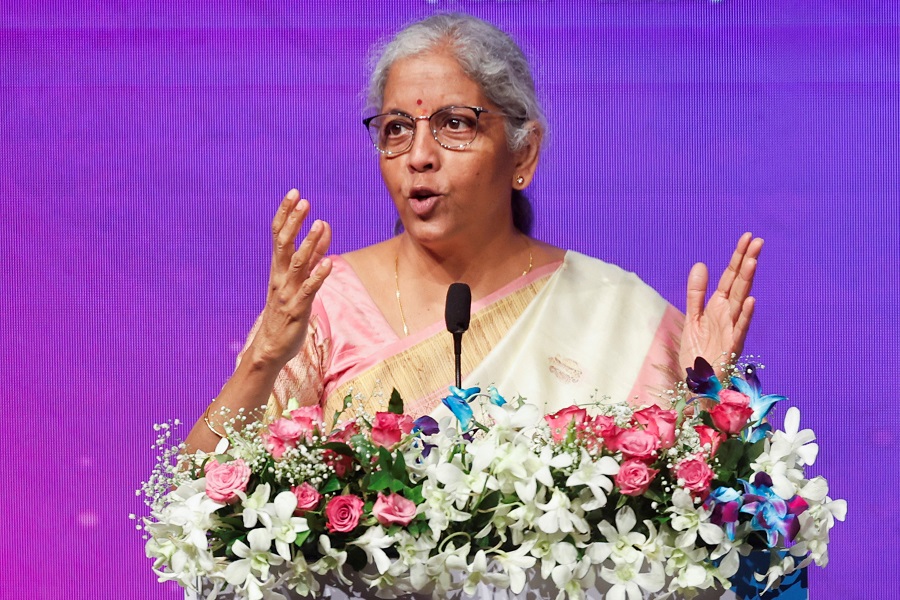
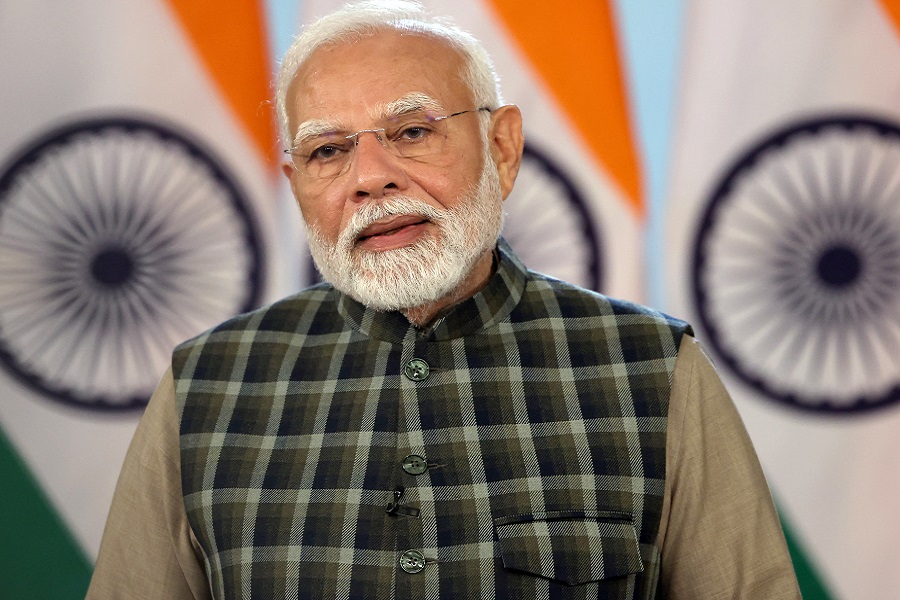