20-09-2023 04:01 PM | Source: Accord Fintech
Mangalam Alloys coming with IPO to raise Rs 54.91 crore
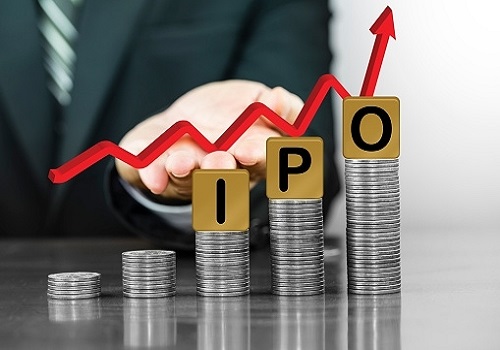
Follow us Now on Telegram ! Get daily 10 - 12 important updates on Business, Finance and Investment. Join our Telegram Channel
Mangalam Alloys
- Mangalam Alloys is coming out with an initial public offering (IPO) of 68,64,000 equity shares of face value of Rs 10 each for cash at a fixed price of Rs 80 per equity share.
- The issue will open for subscription on September 21, 2023 and will close on September 25, 2023.
- The shares will be listed on NSE Emerge.
- The share is priced 8.00 times higher to its face value of Rs 10.
- Book running lead manager to the issue is Expert Global Consultants.
- Compliance Officer for the issue is Manmeetkaur Harshdeepsingh Bhatia.
Profile of the company
Mangalam Alloys was Incorporated by its promoter Uttamchand Chandanmal Mehta and Maheshchand Jain with an aim of running stainless steel melting unit as part of Business growth. The company is having a unique integrated stainless steel, special steel & higher alloys steel melting and further processing unit i.e. up to bright bar fasteners. The company is a stainless steel unit manufacturing SS Ingots, Round Bar, RCS, Bright bar, different sections/ profiles like square, hex, angle, patti, etc, Forging and making fasteners. The company is having integrated stainless steel manufacturing unit covering 40,000 sq. meters land with an installed capacity of 25,000 TPA (Melting Capacity) with a turnover of Rs. 30,292.25 Lakh in the financial year ending on March 31, 2023. Having situated in Ahmedabad, Gujarat, the fastest growing city of India and the third in the world, the location of the Company is one of the primary factors of its growth.
For more than 3 decades, the company has demonstrated an unwavering commitment to performance along with integrity. In the span of years, the company has expanded into new businesses and new regions building a colossal record of sustained growth. As nearly 200 manpower are working in the company, the company has given highest priority to them. Having been quality driven organization, the company maintains the right environment for their employees resulting in high quality products. The important factor for the company’s working policy is its core value of innovation, intelligence, inspiration and integrity.
The company is awarded by various certificates and ISO 9001:2015 and PED certificate also recognized with Two Star Export House by DGFT, India. Furnace is an enclosed structure in which material can be heated to very high temperature. The stainless steel ingots are produced though induction furnace by melting of stainless steel scrap. This is continuous process controlled by uniform heating with the help of electricity. The Stainless Steel scrap is put into the crucible and the temperature is raised up to 1500 degree Celsius with help of electricity and then use Argon Gas and Nitrogen treatment for secondary refining. The liquid metal then poured into cast iron moulds and the ingots so produced from furnace. The company manufactures stainless steel ingots through three furnaces by melting of stainless steel scrap, rolling of ingots to stainless steel rounds & flats followed by heat treatment annealing furnace and bright bar unit.
Proceed is being used for:
- Working capital requirement
- Capital expenditure for business expansion and research and development
- General corporate purposes
- Meeting issue expenses
Industry overview
The India special steel market size was valued at $7.00 billion in 2020, and is projected to reach $38.8 billion by 2035, growing at a CAGR of 10.9% from 2021 to 2035. The Indian steel industry is modern, with state-of-the-art steel mills. It has always strived for continuous modernisation of older plants and up-gradation to higher energy efficiency levels. The Indian steel industry is classified into three categories - major producers, main producers and secondary producers. In 2019, India ranked as the second-largest crude steel producer in the world. Between April 2022 - January 2023, the finished steel production stood at 99.48 MT and in April - November 2022, the production of crude steel in India stood at 81.96 MT. India’s steel production capacity has expanded rapidly over the past few years, growing at a CAGR of 3.93% from 122 MT in FY16 to 143.9 MT in FY21. The National Steel Policy 2017 has envisaged achieving up to 300 MT of production capacity by 2030-31. ii. By FY22, India's total steel capacity is likely to increase to 150 MT annually.
The steel industry has emerged as a major focus area given the dependence of a diverse range of sectors on its output as India works to become a manufacturing powerhouse through policy initiatives like Make in India. With the industry accounting for about 2% of the nation's GDP, India ranks as the world's second largest producer of steel and is poised to overtake China as the world’s second largest consumer of steel. Both the industry and the nation's export manufacturing capacity have the potential to help India regain its favourable steel trade balance.
The National Steel Policy, 2017 envisage 300 million tonnes of production capacity by 2030-31. The per capita consumption of steel has increased from 57.6 kgs to 74.1 kgs during the last five years. The government has a fixed objective of increasing rural consumption of steel from the current 19.6 kg/per capita to 38 kg/per capita by 2030-31. As per Indian Steel Association (ISA), steel demand will grow by 7.2% in 2019-20 and 2020-21. Huge scope for growth is offered by India's comparatively low per capita steel consumption and the expected rise in consumption due to increased infrastructure construction and the thriving automobile and railways sectors.
Pros and strengths
Integrated manufacturing facility: The company does continuous endeavour to maintain the requisite infrastructure and technological up gradation for the smooth running of the manufacturing process as well as to cope with the changing market demand situation. There is a continuous change in the technology and the markets are very dynamic to the change in technology. The company keeps itself technologically upgraded with the latest machines and infrastructure.
Zero Waste Philosophy: The company is an example of implementing Zero Waste Philosophy in Stailess Steel Manufacturing Industry. The company already has achieved and implemented zero effluent discharge, zero domestic sewage discharge. The company has STP plant and with the help of this plant MAL even recycle human waste and use in gardening. MAL is the only unit in India who is recycling near about 100% solid waste and there is no discharge of solid waste at all from the unit.
Well-developed distribution and marketing network: The company has developed and implemented a wide range of networking channels throughout the industry and society to strengthen the scope of identifying core customer base and designing right marketing strategies for procurement and liaising of projects to deliver customized solutions for clients. The company’s distribution and marketing network ensures its product availability to its customers translating into efficient supply chain, focused customer service and short turnaround times for product delivery.
Risks and concerns
Maximum revenue comes from top 10 customers: The business of the company is dependent on top 10 customers. Its top ten customers contribute 48.39%, 30.51% and 26.09% of the topline for the year ended March 31, 2023, March 31, 2022, and 2021 respectively. There is no assurance that it will be able to get the sales from its customers in any future periods, the loss of income will have material and adverse effect on its business and results of operations. Any decline in its quality standards, growing competition and any change in demand may adversely affect its ability to retain them. Moreover, there is no assurance that the company will be able to maintain long term relationships with such customers or find new customers in time.
Significant portion of total revenue is attributable from top 2 states only: The company is working in 8 states among which, its Revenues is dependent on the top 2 states including Gujarat and Karnataka. It generated almost 79.53% and 17.82% of the total revenue from Gujarat and Karnataka respectively for the financial year ended March 31, 2023. The heavy reliance on Gujarat and Karnataka exposes it to concentration risk. Clients in these two states may contribute a substantial share of its revenue in the future. The loss of a major client or reduced business from significant clients in these regions could have a considerable negative impact on its financials.
High working capital requirement: The company’s business demands substantial funds towards working capital requirements. In case there are insufficient cash flows to meet its working capital requirement or the company is unable to arrange the same from other sources or there are delays in disbursement of arranged funds, or if it is unable to procure funds on favourable terms, it may result into its inability to finance its working capital needs on a timely basis which may have an adverse effect on its operations, profitability and growth prospects.
Outlook
Mangalam Alloys is primarily engaged in the business of manufacturing and processing of SS Ingots, Round Bar, Flats, Bright Bars, with section round, hex, square, SS Angles, SS Patti, SS Forgings and SS Fasteners. The company has outgrown itself into a distinguished large-scale organization specializing in steel and alloys various types having plentiful applications. Its experience of more than 3 decades has enabled it to build an effective business model that gives it control over its processes from raw material procurement, manufacturing and marketing to sales through its network. On the concern side, the company is dependent on top 10 customers for sales. The loss of any of these large customers may affect its revenues and profitability. Moreover, a significant portion of the company’s total revenue is attributable from top 2 states only and the loss of a major client or reduced business from significant clients in these regions could have a considerable negative impact on its financials.
The company is coming out with an IPO of 68,64,000 equity shares of face value of Rs 10 each for cash at a fixed price of Rs 80 per equity share to mobilize Rs 54.91 crore. On performance front, the company’s revenue from operations has decreased by 2.08% to Rs 302.92 crore for financial year 2022-23 from Rs 309.37 crore for financial year 2021-22. This decrease is due to fall in exports. Moreover, profit of the company increased to Rs 10.14 crore in FY23 from Rs 5.05 crore in FY22. Meanwhile, the company focus on value added products instead of low value added products. The company works with zero waste philosophy (as in Mother Nature there is no waste). Zero waste includes Zero solid waste (recycling 100%) and Zero liquid waste (recycle liquid discharge by STP). Moreover, the company is continuously doing R&D on its products, process improvement and develop new grades. It has achieved in manufacturing of rare grades in its melting unit which are substitute of imports. It is continuously working on improving its process by minimizing cost i.e. indirectly generating revenue, which will increase its bottom line. Doing forward, the company is developing new markets such as Canada and United States of America
Latest News
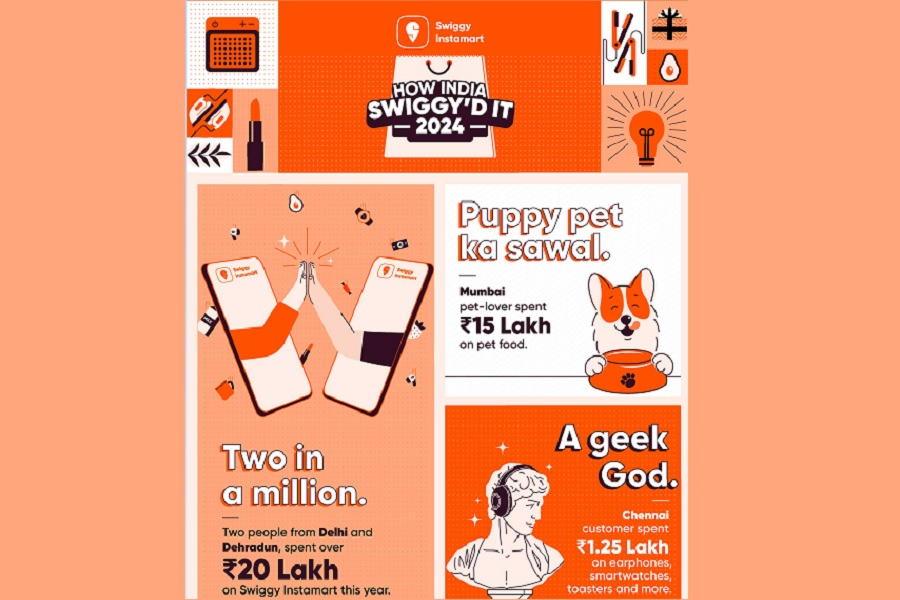
How India Swiggy`d 2024: Swiggy Instamart Edition
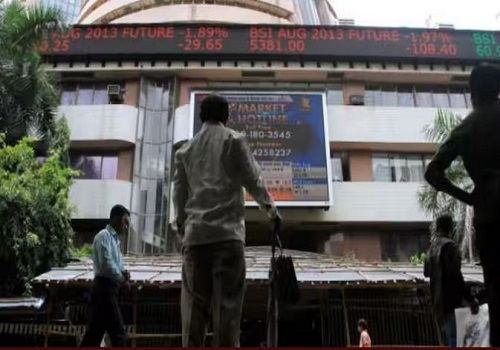
Share market ends flat, Adani Ports top gainer
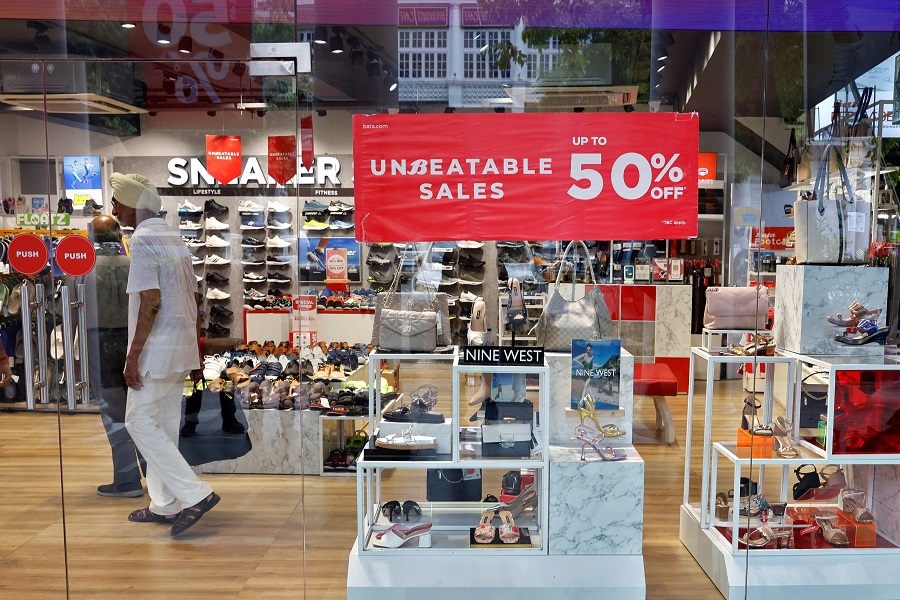
India considers cutting personal income tax to lift ...
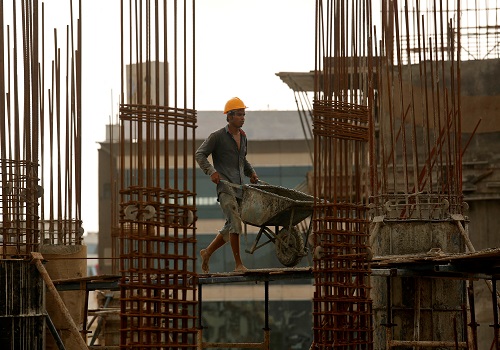
GHV Infra Projects touches the roof on receiving sub...
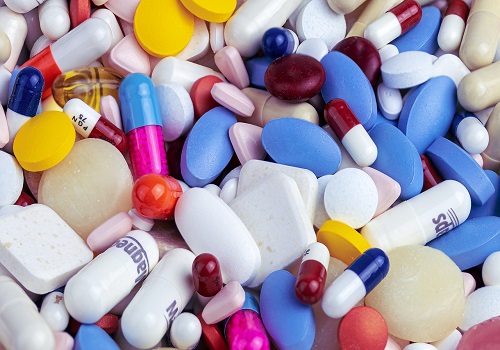
Shelter Pharma climbs on securing order worth $23,000
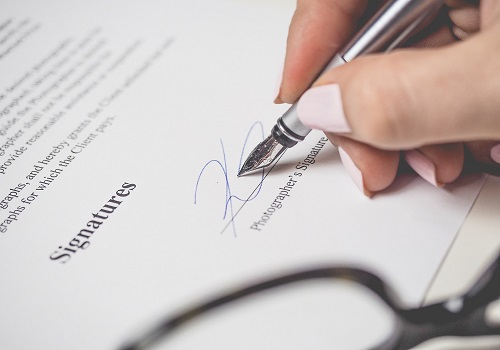
Ace Software Exports surges on signing LoI with repu...
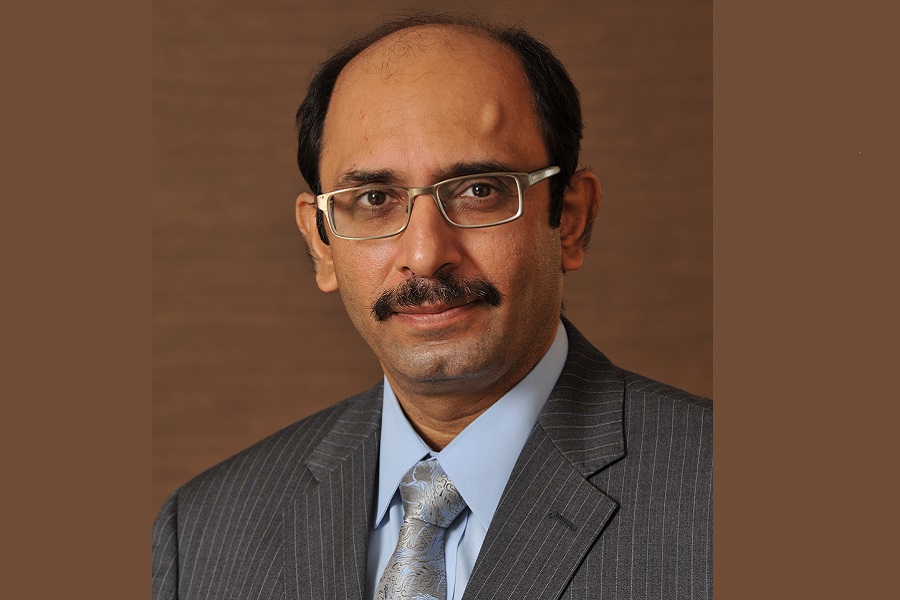
From Fear to Confidence ? How to overcome Loss Avers...
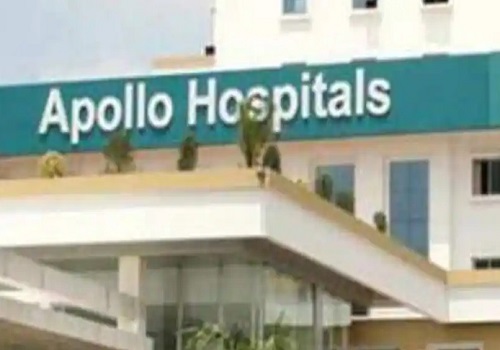
Apollo Hospitals Enterprise gains as its arm to acqu...

India strengthens leadership in agricultural exports...
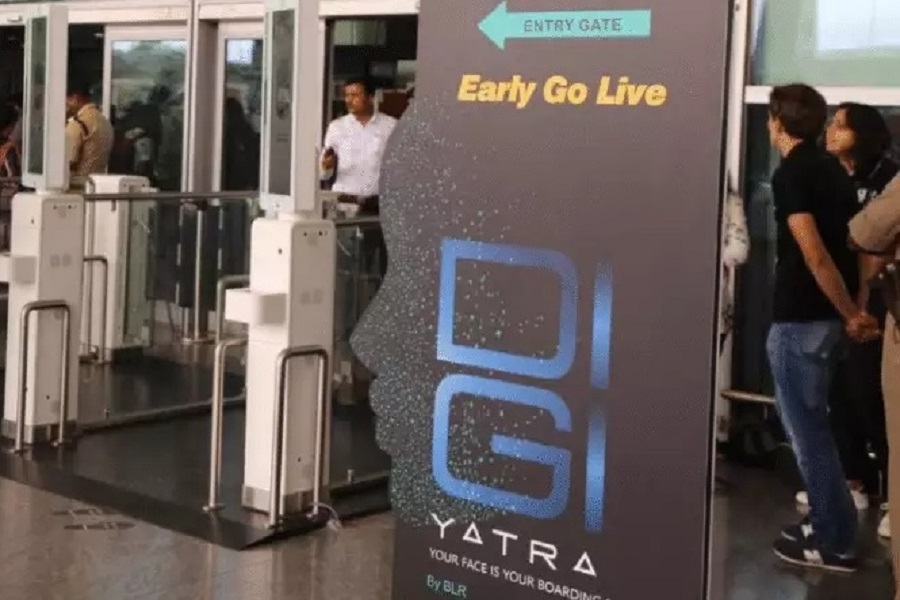
Digi Yatra clocks over 9 million active users, 30,00...