Pyramid Technoplast coming up with IPO to raise upto Rs 153.05 crore
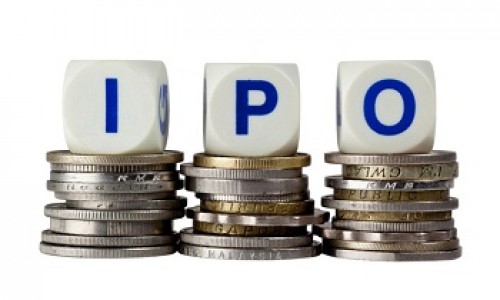
- Pyramid Technoplast is coming out with a 100% book building; initial public offering (IPO) of 92,20,000 shares of Rs 10 each in a price band Rs 151- 166 per equity share.
- Not more than 30% of the issue will be allocated to Qualified Institutional Buyers (QIBs), including 5% to the mutual funds. Further, not less than 20% of the issue will be available for the non-institutional bidders and the remaining 50% for the retail investors.
- The issue will open for subscription on August 18, 2023 and will close on August 22, 2023.
- The shares will be listed on BSE as well as NSE.
- The face value of the share is Rs 10 and is priced 15.10 times of its face value on the lower side and 16.60 times on the higher side.
- Book running lead managers to the issue are PNB Investment Services and First Overseas Capital.
- Compliance Officer for the issue is Chandrakant Joge.
Profile of the company
The company is an industrial packaging company engaged in the business of manufacturing polymer based molded products (Polymer Drums) mainly used by chemical, agrochemical, speciality chemical and pharmaceutical companies for their packaging requirements. It is one of the leading manufacturers of rigid Intermediate Bulk Containers (IBC) in India manufacturing 1,000 litre capacity IBC. IBCs are industrial-grade containers engineered for the mass handling, transport, and storage of liquids, semi-solids, pastes, or solids. Rigid IBCs are manufactured across a volume range which is in between that of standard shipping drums and intermodal tank containers, hence the title intermediate bulk container. It also manufacture MS Drums made of mild steel (MS) used in the packaging and transport of chemicals, agrochemicals and speciality chemicals.
The company use blow molding technology to manufacture Polymer Drums and IBCs. Injection molding technology is used for manufacturing caps, closures, bungs, lids, handles, lugs, etc. for in-house use. Its products are marketed and sold under its brand name ‘Pyramid’. It started commercial production in the year 1998 in Unit I. Presently, it has six strategically situated manufacturing units out of which four are in Bharuch, GIDC, Gujarat and two are situated at Silvassa, UT of Dadra and Nagar Haveli. The seventh manufacturing unit is under construction at the Bharuch, GIDC, Gujarat adjacent to the existing six units. The total installed capacity of the company’s Polymer Drum manufacturing units is 20,612 MTPA. The total installed capacity of its IBC manufacturing unit is 12,820 MTPA and the total installed capacity of its MS Drums unit is 6,200 MTPA.
Proceed is being used for:
- Repayment and/or pre-payment, in full or part, of certain outstanding borrowings availed by the company.
- Funding working capital requirements of the company.
- General corporate purposes.
Industry overview
Plastic molding is the process of pouring liquid plastic into a container or mold and allowing it to harden into the desired shape. These plastic molds can then be used for a variety of applications. When molding plastics, a powder or liquid polymer, such as polypropylene or polyethylene, is poured into a hollow mold and allowed to assume shape. Various ranges of heat and pressure are employed to create an end product depending on the type of process performed. There are many different types of plastic molding that are thought to be the most effective and popular.
An intermediate bulk containers (IBC) are known to be reusable industrial containers which are extensively utilized for the handling, storage and transportation of variable states of products including, pastes, liquids and solids. These containers are named as intermediate as they are relatively larger than drum and comparatively smaller than tanks. These containers are widely adopted across various end-use industries including, pharmaceuticals, chemicals, and food & beverages, among others. The rapid growth in these sectors in the Indian region would enhance the demand for the intermediate bulk containers. As the adoption of these containers offers various benefits including, customizable, durable, reusable, cost efficient, ease of logistics usage, capability to handle pressure during transportation, and optimised storage space, among others. For instance, key chemical manufacturers widely use intermediate bulk containers for the transportation and storage of various kinds of powders that are constituents in a chemical product and also be utilized to contain a liquid that serves as a catalyst to quicken chemical reactions. The demand for intermediate bulk containers in India is anticipated to grow significantly in the forecast years.
High-density polyethylene, or HDPE, is the specific type of plastic used in the production of polymer drums. For storing and moving goods, barrels and drums have been used for millennia. The oldest of these containers were built of readily accessible materials like wood or clay. Steel production enabled the creation of steel drums a century ago, and synthetic polymer drum and barrel production quickly followed. Modern technology made it possible to mass-produce plastic at low cost. Since HDPE was created to be sturdy and long-lasting enough to hold even the most dangerous chemicals, it swiftly gained popularity during the 20th century. HDPE, a polymer-based plastic, is ideal for an industrial application because it doesn't react with many everyday components and won't react with many other chemicals and substances. HDPE barrels are made using plastic mould, which make it simple to build a smooth, cylindrical-shaped drum in great quantities while keeping expenses to a minimum. Polymer drums come in two basic types: open head and tight head. For storage or transportation, open head polymer drums can be sealed with a tight lid and fasteners or left open-topped. The top of the container will be used for both filling and emptying because it has the single entrance.
Pros and strengths
Diverse customer base: The company caters to bulk packaging requirements of its clients from diverse industries like chemicals, agrochemicals, pharmaceuticals, lubricants and edible oil by supplying them Polymer Drums, IBC and MS drums. It has over the years established relationships with various clients across these industries and continue to serve them its product offerings. Its clients have stringent quality and qualification requirements which it is required to adhere to for continued supply of its products. It enjoys long term relationships with most of its clients and the repeat business from them allows it to have strong visibility on future revenues and a stable client base. It has served more than 376 customers on a regular basis during the past three financial years.
Comprehensive product portfolio: The company offers complete bulk industrial packaging solutions to its clients since it manufacture both polymer based bulk packaging drums and IBC, as well as MS Drums for packaging. Its product offering in polymer based packaging by way of drums ranges from 20 litres to 250 litres and IBC which is 1,000 litres. It also offer the alternative packaging option of MS Drums manufactured from MS enabling it to offer and provide alternative packaging solutions to its customers as per their preferences and requirements. It use blow molding technology to manufacture industrial packaging products such as jerry cans, polycans, drums (wide mouth, narrow mouth, open top), open top drums, etc. ranging from 20 litres to 250 litres. In addition to these products, it also use injection molding technology to manufacture caps, closures, bungs, lids, handles lugs for in-house use for the products manufactured by it.
Strategic location of its manufacturing units: The company has six manufacturing units out of which its four are situated at Bharuch, GIDC, Gujarat and two units are situated at Silvassa, UT of Dadra and Nagar Haveli. Its units are situated in the industrial belts of Bharuch, Gujarat and Silvassa, UT of Dadra and Nagar Haveli which are manufacturing hubs for various industries like chemicals, agrochemicals, pharmaceuticals, lubricants, edible oil, etc. Proximity to these industries enables easy accessibility and delivery of its products to these industries in these industrial regions. Since it is a B2B supplier of products, being close to its end-user market provides various advantages including lower freight costs and improved customer relationships. The location of its units is in proximity to Mumbai and major industrial zones having good connectivity to ports, airports and highways which enhances its capability of supplying its products in time and on a cost-effective basis to its clients.
Quality Standard Certifications & Quality Tests: The company has obtained UN certification for IBC and MS Drums to meet safety levels outlined by United Nations Recommendations on the Transport of Dangerous Goods, in order to transport them safely (by road, rail, sea and air). Its manufacturing units are ISO 9001:2015/ ISO 14001:2015/ISO 45001:2018 certified by quality, environment, health and safety management systems for the manufacture of Polymer Drums, carboys, jerry cans, IBC & MS Drums and accessories connected thereto. Further, its MS Drums meet quality standards as per IS 1783:2014 (Part 1 and 2) laid down by Bureau of Indian Standards. Its products undergo stringent quality tests to meet industry standards before they are delivered to its clients.
Risks and concerns
Substantial working capital requirements: The company’s business requires significant amount of working capital. It requires significant amount of its working capital for purchasing key raw materials which are procured from domestic and international suppliers. Though, presently it has sanctioned working capital limits from the existing lenders and one of the Objects of the Offer is to meet its future working capital requirements, it may need additional debt in the future to satisfy its working capital needs. It strives to maintain strong relationships with banks and non-banking financial institutions to increase its financing flexibility. Its credit profile often enables it to obtain financing on favourable terms from financial institutions. However, it cannot assure that its relationships with lenders will not change or that lenders will continue lending practices it is familiar with.
Polymer Drum paneling hamper their usage in certain industrial applications: The walls of polymer drums are few millimeters thick and in some industrial applications they need to be controlled to external and internal pressures to ensure they are within their allowable tolerance ranges. A distortion in the drums' outer surface may be seen when the pressure applied to them is outside their allowable tolerance ranges. Panelling is the conventional name for this phenomena. Variations in temperature, product penetration through the container wall, storage of an oxygen scavenger product in the drum, and changes in air pressure conditions are all causes of problems with Polymer Drum paneling and can hamper the usage of Polymer drums in some industrial applications. The Polymer Drums manufactured and supplied by it to its customers are mainly for the purpose of industrial packaging for transportation of chemicals, agrochemicals, speciality chemicals and pharmaceuticals by its customers.
Any reduction in demand for products could lead to underutilization of manufacturing capacity: The company faces the risk that its customers might not place any order or might place orders of lesser than expected size or may even cancel existing orders or make change in their policies which may result in reduced quantities being manufactured by it. Cancellations, reductions or instructions to delay production (thereby delaying delivery of products manufactured by it) by customers could adversely affect its results of operations by reducing its sales volume leading to a reduced utilization of its existing manufacturing capacity. Further, it make significant decisions, including determining the levels of business that it will seek and accept, production schedules, personnel requirements and other resource requirements, based on its estimates of customer orders. The changes in demand for their products (which are in turn manufactured by it) could reduce its ability to estimate accurately future customer requirements, make it difficult to schedule production and lead to over production and utilization of its manufacturing capacity for a particular product.
Any downgrade of debt ratings could adversely affect business: Currently, the company’s borrowings facilities availed from the bank are rated by a credit rating agency. These ratings assess its overall financial capacity to pay its obligations and are reflective of its ability to meet financial commitments as they become due. Though the credit rating have not been downgraded in the past three financial years, there can be no assurance that these ratings will not be revised or changed by the above rating agencies due to various factors, including on account of the COVID-19 pandemic. Any downgrade in its credit ratings may increase interest rates for refinancing its outstanding debt, which would increase its financing costs, and adversely affect its future issuances of debt and its ability to raise new capital on a competitive basis.
Outlook
Incorporated in 1997, Pyramid Technoplast manufactures polymer-based molded products (Polymer Drums) mainly used by chemical, agrochemical, specialty chemical, and pharmaceutical companies for their packaging requirements. The company manufactures polymer-based bulk packaging drums and Intermediate Bulk Containers (IBC), as well as MS Drums for packaging used in the packaging and transport of chemicals, agrochemicals, and specialty chemicals. Pyramid Technoplast started its commercial production in 1998 and now has over 6 manufacturing units out of which four are situated in Bharuch, GIDC, Gujarat, and two are situated at Silvassa, UT of Dadra and Nagar Haveli. The total installed capacity of their Polymer Drum manufacturing units is 20,612 MTPA, the total installed capacity of the IBC manufacturing unit is 12,820 MTPA and the total installed capacity of the MS Drums unit is 6,200 MTPA. The company is in the process of constructing its seventh manufacturing unit which will also be situated in Bharuch, GIDC, Gujarat. On the concern side, the company faces competition from various domestic manufacturers and traders. Competition emerges from organized as well as unorganised players in the plastic product industry. Besides, the company has experienced negative net cash flow from operating in the past and may continue to experience such negative operating cash flows in the future.
The company is coming out with an IPO of 92,20,000 equity shares of face value of Rs 10 each. The issue has been offered in a price band of Rs 151-166 per equity share. The aggregate size of the offer is around Rs 139.22 crore to Rs 153.05 crore based on lower and upper price band respectively. On the financial front, total income increased by 19.72% to Rs 48,202.74 lakh for Fiscal 2023 from Rs 40,264.15 lakh for Fiscal 2022 primarily due to an increase in revenue from operations. The company’s profit after tax (PAT) increased by 21.47% to Rs 3,176.07 lakh for the financial year 2023 from Rs 2,614.61 lakh for the financial year 2022. Meanwhile, the company intends to continue its focus on IBC by expanding its existing capacity by adding new manufacturing unit (Unit VII) at Bharuch GIDC, Gujarat near its existing manufacturing units. It intends to continue its focus on the manufacturing of Polymer drums and MS drums used by chemical, agrochemical, speciality chemical and pharmaceutical companies. Polymer and MS drums demand has shown continuous growth for the past several years considering the growth prospects of these sectors it will required to meet the demand coming from these industries in the future.
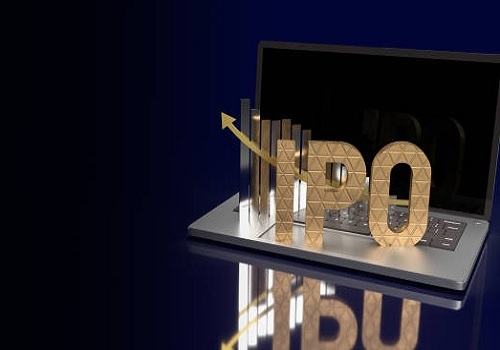
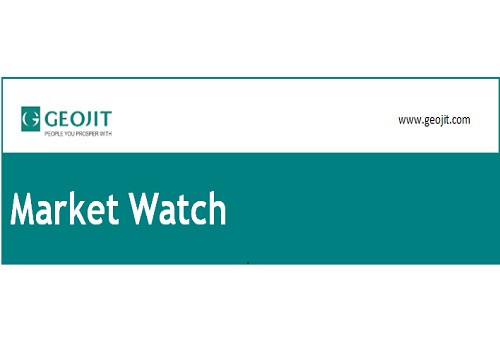
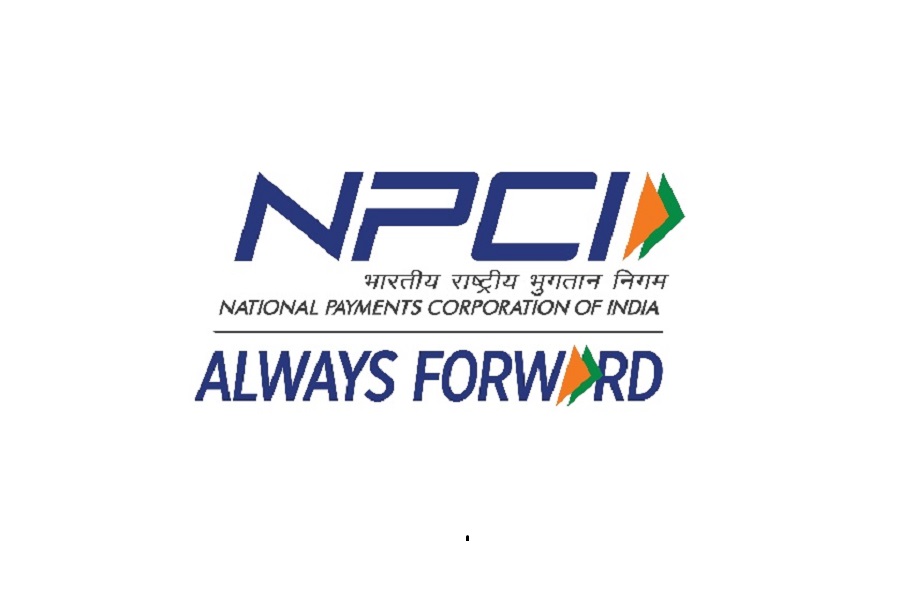
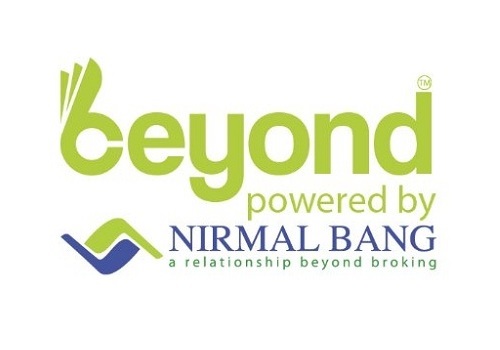

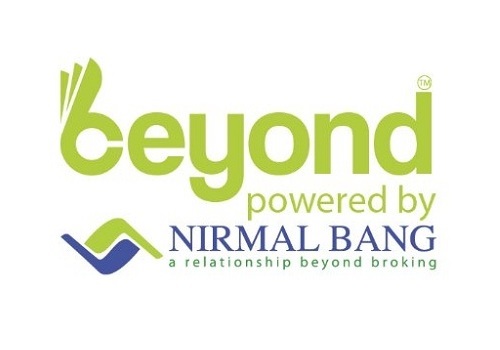
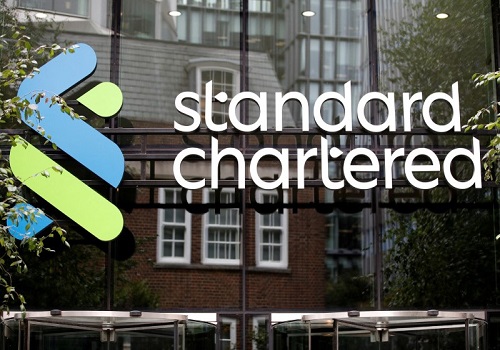
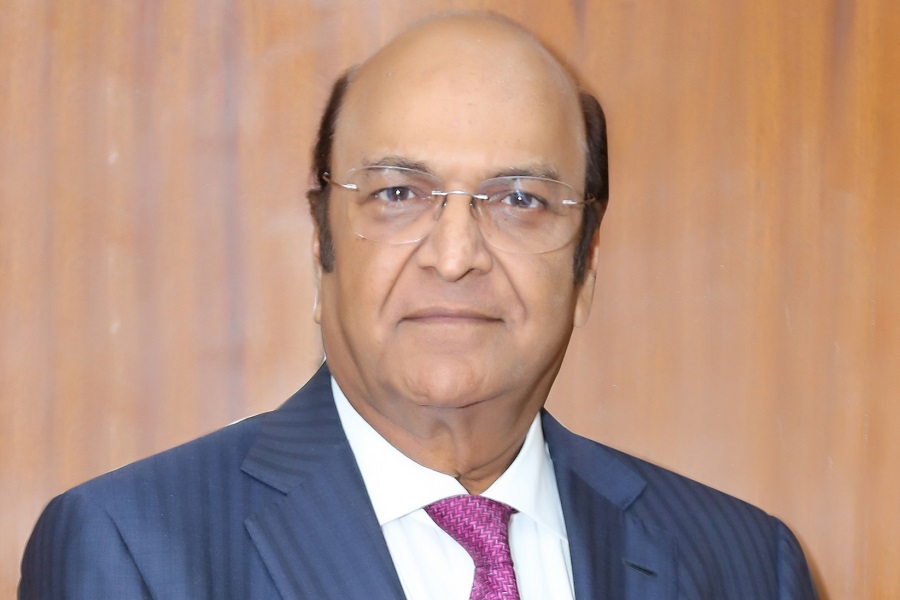
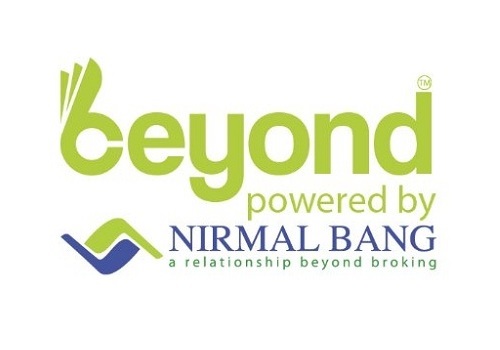
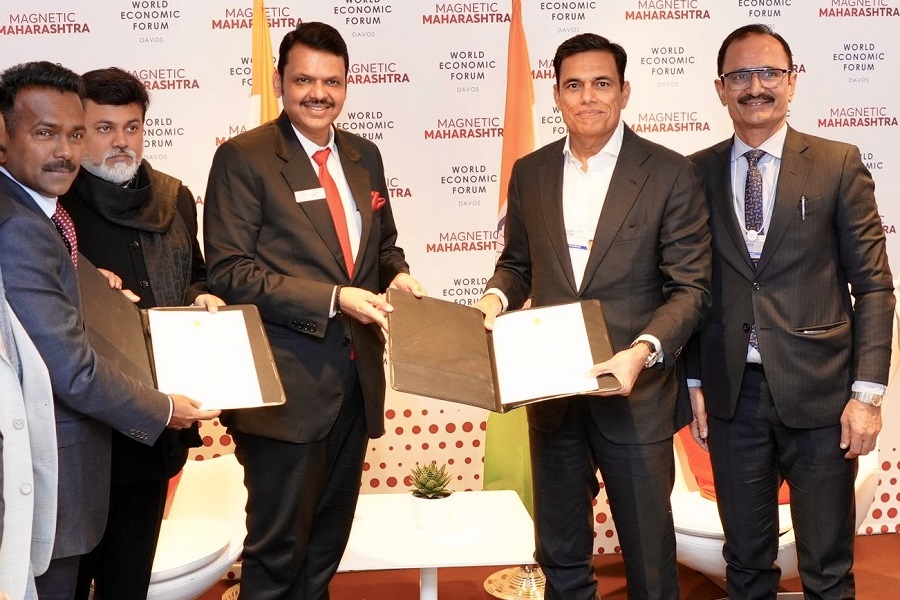