Alphalogic Industries coming with an IPO to raise Rs 12.88 crore
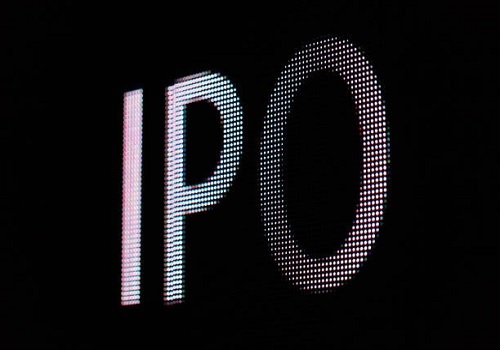
Alphalogic Industries
- Alphalogic Industries is coming out with an initial public offering (IPO) of 13,41,600 equity shares of face value of Rs 10 each for cash at a fixed price of Rs 96 per equity share.
- The issue will open for subscription on July 3, 2023 and will close on July 6, 2023.
- The shares will be listed on BSE SME.
- The share is priced 9.60 times higher to its face value of Rs 10.
- Book running lead manager to the issue is Finshore Management Services.
- Compliance Officer for the issue is Aayushi Khandelwal.
Profile of the company
Alphalogic Industries Limited was incorporated in the year 2020. The company is engaged in Design, Manufacturing, Supply and Installation of Industrial and Institutional Storage Systems i.e. Compactor Storage System, Heavy Duty Storage Racks, Cantilever Racks, Lockers, Mezzanine Floors, Metal Pallets & Crates, Library Stacks, Book Case, Book Trolly, Periodical Display Rack, School Lockers, Book Support etc. Its state-of-the-art manufacturing facility located at Pune, Maharashtra delivers an array of customized storage systems that are safe, easy to use, save space, and attractive. It is an ISO 9001:2015, 14001:2015, 45001:2018 and BIFMA certified storage solution manufacturing company. Its commitment to innovation, excellence, quality, and customer service has ensured consistent growth for it and its clients. Its compact products with simple designs facilitate transport and assembling at the site. They are easy to operate and maintain, and beautifully become a part of clients workspace, enhancing its ambiance.
It has designed and delivered storage solutions for the automobile industry, e-commerce companies, food industry, logistics companies, engineering companies, pharmaceutical organizations, educational institutes, IT companies, etc. It understands the industry needs and study the usage-specific requirements to suggest designs that fulfil the storage requirements of clients in the best possible manner. Some of the storage systems that are in great demand are Pallet Racking System, Shelving Systems, Mezzanine & Cantilever Racking, Mobile Compactor, Metal Pallets, Storage and Display racks. Its manufacturing process includes both through In-house manufacturing and outsourcing model. Through its outsourcing model, it mainly process the following activities i.e. Perforation, Powder Coating, Installation etc.
Proceed is being used for:
- Meeting working capital requirements
- Meeting the issue expenses
- General corporate purposes
Industry overview
One of the primary forces behind industrialization has been the use of metals. Steel has traditionally occupied a top spot among metals. Steel production and consumption are frequently seen as measures of a country's economic development because it is both a raw material and an intermediary product. Therefore, it would not be an exaggeration to argue that the steel sector has always been at the forefront of industrial progress and that it is the foundation of any economy. The Indian steel industry is classified into three categories - major producers, main producers and secondary producers.
In the past 10-12 years, India's steel sector has expanded significantly. Production has increased by 75% since 2008, while domestic steel demand has increased by almost 80%. The capacity for producing steel has grown concurrently, and the rise has been largely organic. In FY22, the production of crude steel and finished steel stood at 133.596 MT and 120.01 MT, respectively. The consumption of finished steel stood at 105.751 MT in FY22. Between April-December 2022, India's finished steel consumption stood at 75.34 MT. In April-July 2022, the production of crude steel and finished steel stood at 40.95 MT and 38.55 MT respectively.
The steel industry has emerged as a major focus area given the dependence of a diverse range of sectors on its output as India works to become a manufacturing powerhouse through policy initiatives like Make in India. With the industry accounting for about 2% of the nation's GDP, India ranks as the world's second-largest producer of steel and is poised to overtake China as the world's second-largest consumer of steel. Both the industry and the nation's export manufacturing capacity have the potential to help India regain its favourable steel trade balance.
Pros and strengths
Smooth flow of operations: It has maintained good relationship with its major customers. It is successful in building a strong client base for its business. Its existing relationships help it to get repeat business from its customers. This has helped it to maintain a long-term working relationship with its customers and improve its customer retention strategy. It considers that its existing relationship with its clients represents a competitive advantage in gaining new clients and increasing its business.
Well-defined organizational structure: The company has a qualified and experienced management that has decision making powers. It is expected to benefit from the management’s ability to ensure smooth flow of operations. The company is managed by a team of competent personnel having knowledge of core aspects of its Business. Its senior management has pioneered its growth and fostered a culture of innovation, entrepreneurship and teamwork within its organization.
Quality assurance and accreditations: Quality plays one of the most vital role in the success of any organization. It is focused on providing high quality products and services. It constantly strive to improve its industrial processes at every step in its manufacturing of finished products. Its focus on quality is evidenced by the quality certifications and accreditations that its facility has obtained from various local and international accreditation agencies.
Risks and concerns
Depends on third-party services: The company is dependent on third party for certain processes i.e. Perforation, Powder Coating, installation etc. It may not be able to obtain services from third parties for its requirements, on attractive rates or the third parties may not have adequate available capacity to meet its requirements in a timely manner. Further, if the company is unable to procure the services of third-party capable of sufficiently scaling up operations in response to increased demand from customers, the company might be compelled to make capital expenditures or seek out costlier or lower quality third-party service to meet the requirements which could have an adverse effect on the business prospects, financial condition and results of operations of the company.
Highly competitive industry: It operates in the highly competitive industry. There are no entry barriers in its industry which puts it to the threat of competition from new entrants. There are numerous players operating in the industry. It faces tough competition in its business from a large number of unorganized and a few organized players. Its aim is to provide the standardized and uniform quality products at competitive prices to its consumers. It competes with its competitors on a regional or product line basis. Many of its competitors have substantially large capital base and resources than it do and offer broader range products.
Dependent on few customers: Revenues from any of its particular customers may vary significantly from reporting period to reporting period depending on the nature of ongoing orders and the implementation schedule for such orders. The company is supplying its products majorly to customers from Maharashtra, Karnataka and Telangana. The efficiency of the sales and marketing network is critical to success of the company. Its success lies in the strength of its relationship with the customers who have been associated with the company. Its team through their experience and good rapport with these customers owing to timely and quality delivery of products plays an instrumental role in creating and expanding a work platform for the company. However, such concentration of its business on a few customers may adversely affect it if it do not achieve its expected margins or suffer losses on one or more of these customer contracts. Significant revenue from a few customers increases the potential volatility of its results and exposure to individual contract risks with such customers and suppliers, which may have an adverse effect on its results of operations.
Outlook
Incorporated in the year 2020. The company is engaged in Design, Manufacturing, Supply and Installation of Industrial and Institutional Storage Systems i.e. Compactor Storage System, Heavy Duty Storage Racks, Cantilever Racks, Lockers, Mezzanine Floors, Metal Pallets & Crates, Library Stacks, Book Case, Book Trolly, Periodical Display Rack, School Lockers, Book Support etc. On the concern side, it operates in the highly competitive industry. There are no entry barriers in its industry which puts it to the threat of competition from new entrants. There are numerous players operating in the industry. It faces tough competition in its business from a large number of unorganized and a few organized players.
The company is coming out with an IPO of 13,41,600 equity shares of face value of Rs 10 each for cash at a fixed price of Rs 96 per equity share to mobilize Rs 12.88 crore. On performance the company’s revenue from operation and other income of the company was increased to Rs 1823.14 lakh in FY 2022-23 as against Rs 784.33 lakh in the FY 2021-22. The restated Profit after Tax for FY 2022-23 has been increased to Rs 219.41 lakh as against Rs 30.51 lakh in the FY 2021-22. Going forward, the company focuses on improving operating efficiencies to achieve cost reductions to have a competitive edge. It continuously strives to increase operational output through continuous process improvements, quality check and technology development. Its employees are regularly motivated to increase efficiency, higher productivity with minimum wastage. Economies of scale also plays an important role. Its focus is on increasing sales volume through expansion, diversification and spread in geographical outreach.
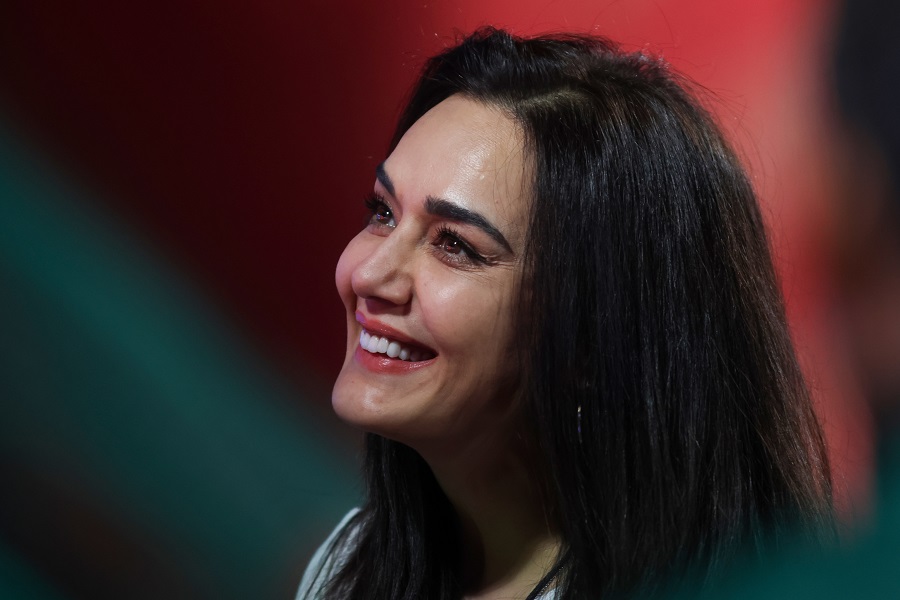
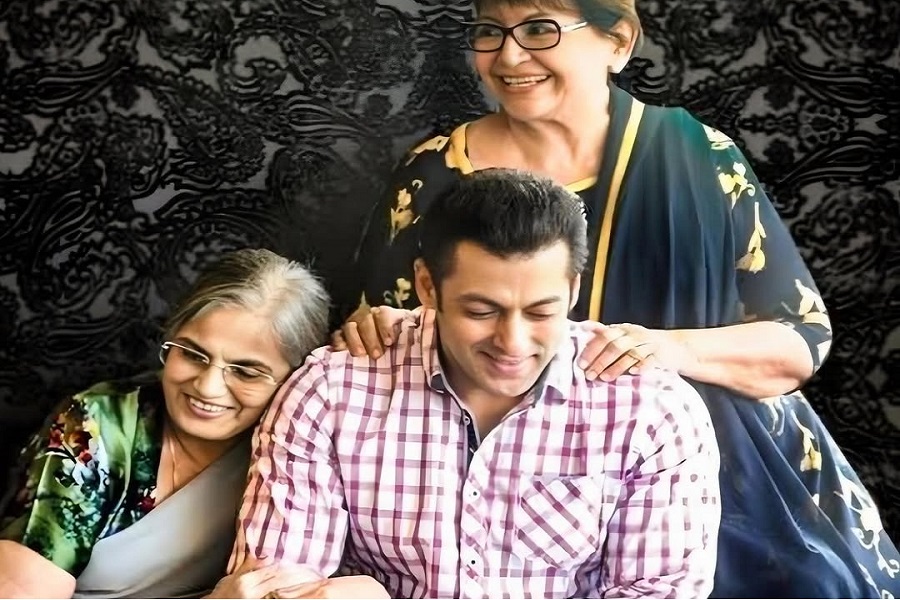
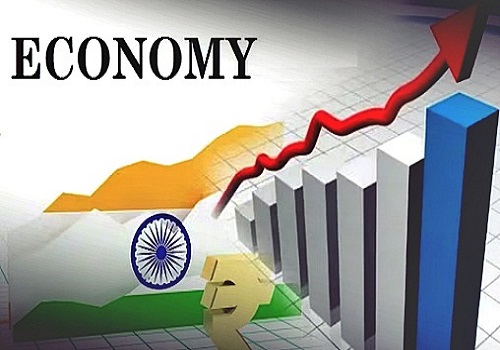
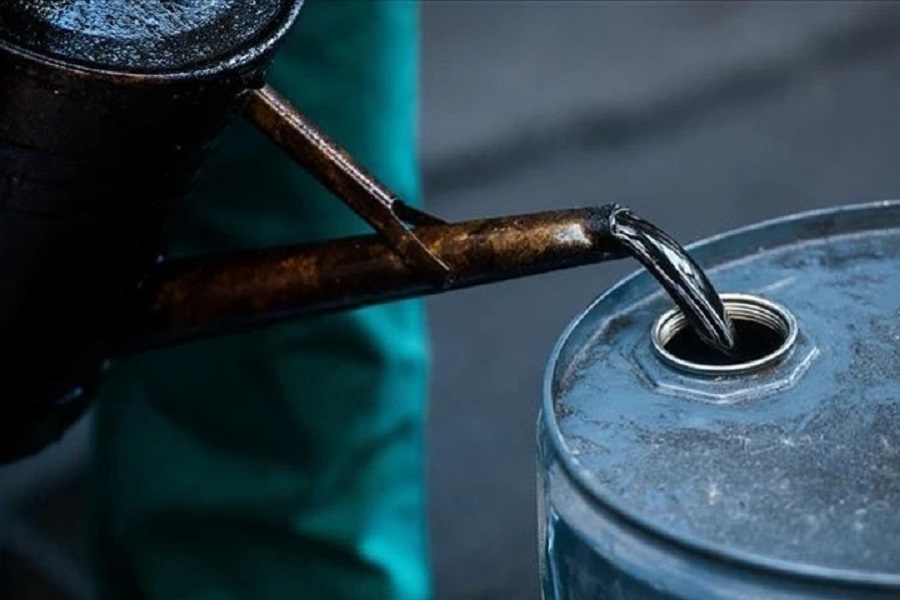
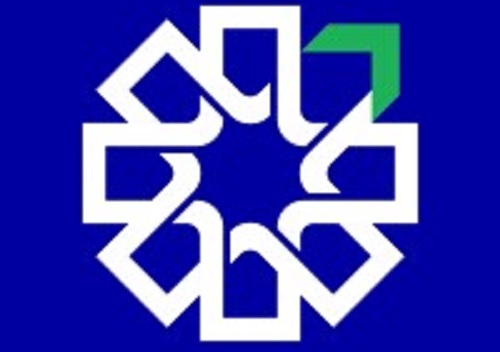
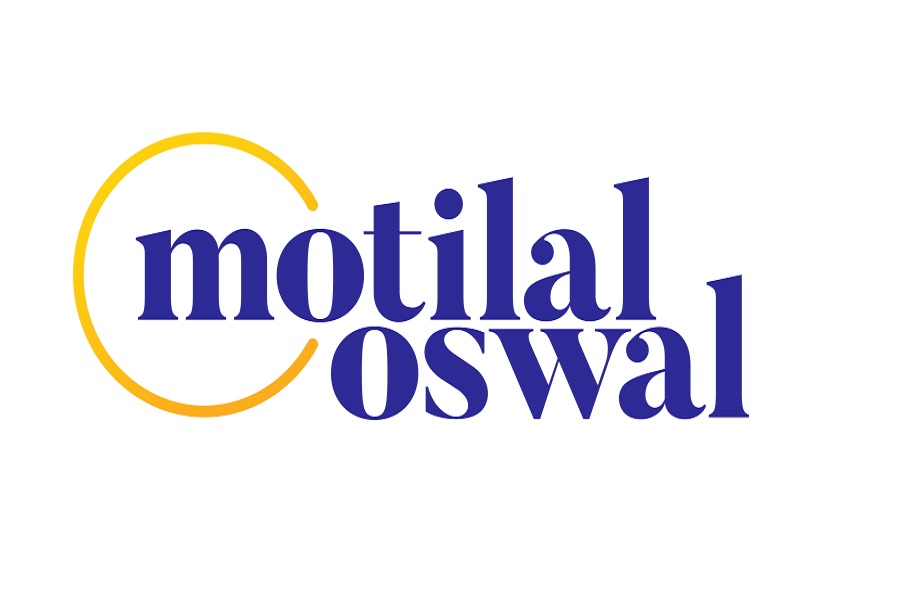
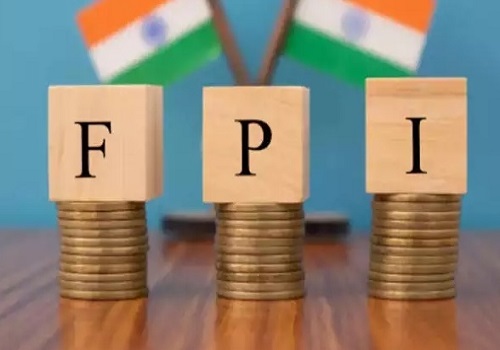
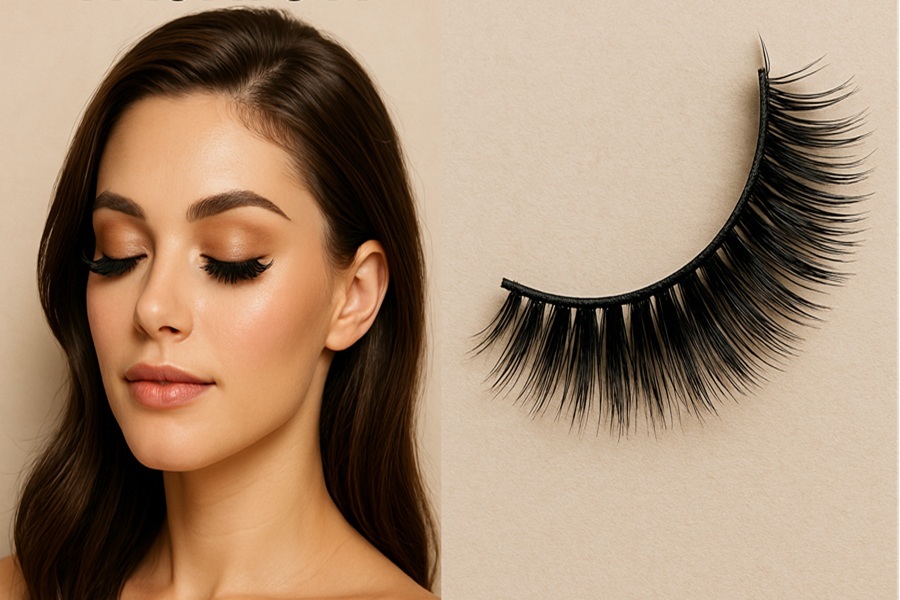
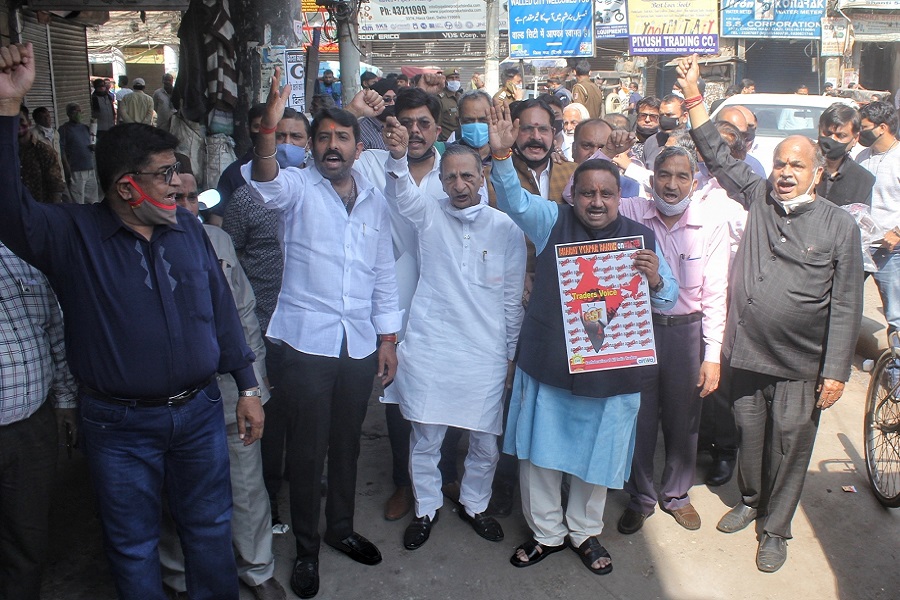
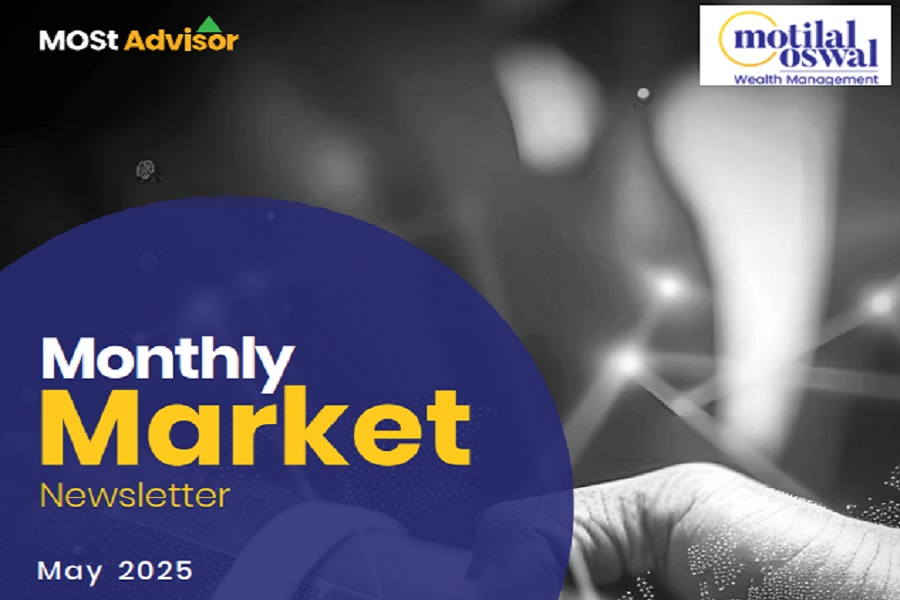