SBICAPS Report : Briding the Green Gap - Investigation into Project Economics of GREEN H2
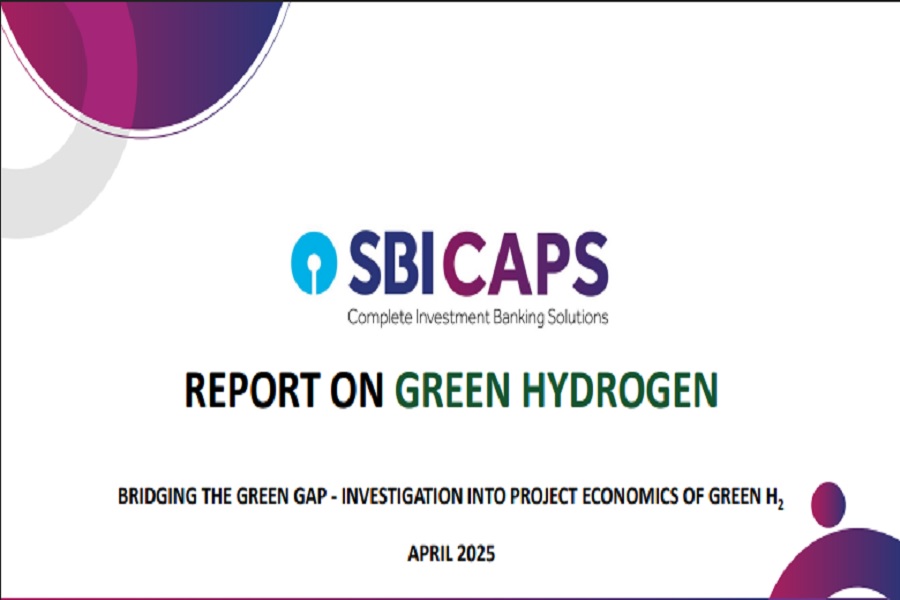
EXECUTIVE SUMMARY
Import substitution: the untapped driver of India’s H2 demand from traditional sources
India's incumbent H2 demand, embedded within the substantial importation of natural gas for fertiliser and refinery applications, constitutes a significant ~9 mn tonnes, predominantly as grey H2 . Since these end users are near saturation (and expected to grow by only ~3% per annum hereon), H2 demand in India has grown slowly at ~5-6% per annum. Hence, bulk of the demand from traditional sectors would be for substitution of natural gas imports – which is one of the aims of the NGHM.
Green light for growth: new H2 uses hinge on reducing both carbon and costs
Emerging H2 applications in transport, steel production, and piped gas blending remain underdeveloped due to current cost premia relative to incumbent solutions and the comparable emissions profile of grey H2 production. Green H2 presents a transformative potential, with various pilot projects exploring these applications. While demand from these nascent sectors is contingent on significant cost reductions, an estimated incremental demand of ~2-5 mn tonnes could materialise by 2030
SIGHT Lines: growing interest through incentives, with more to come
To achieve stated objectives, the Union initiated the Rs. 175 bn SIGHT scheme, offering incentives across the green hydrogen value chain, from electrolyser manufacturing to green molecule synthesis. Component 1 (electrolyser manufacturing) is fully subscribed, while Component 2 (green molecule synthesis) has achieved 40% allocation. Scheme interest is escalating, evidenced by a 33% average reduction in incentive demands for green molecule manufacturing between tranches and sustained interest from major players across all categories. Subsequent modes of SIGHT also close a critical chink by tying up demand and are expected see fair traction.
High energy costs and primitive electrolyser technology create the green gap
SIGHT incentives for green molecule production are projected to reduce green H2 costs by approximately Rs. 15/kg over the project lifecycle. However, this subsidy is insufficient to bridge the current cost differential, with green H2 priced at ~Rs. 300/kg compared to grey H2 at ~Rs. 150/kg. Achieving project viability necessitates a confluence of factors, including substantial reductions in power costs, enhanced electrolyser scale and efficiency, operational expenditure optimisation, and supplementary revenue generation from heat and O2 byproducts
Filling the green gap: large players with integrated renewable capacity and tied-up use cases will get the most breathing space on viability
Key success factors for green H2 projects include substantial operational scale, access to captive renewable energy sources with storage in favorable regions (potentially yielding savings up to Rs. 75/kg), secured demand through internal consumption or long-term HPAs, access to cost-effective, high-efficiency electrolysers (benefiting from intra-group access to electrolyser manufacturing subsidies), adequate storage and transport infrastructure (proximity to demand centers, green H2 hubs, or East Coast for exports), and high average incentive capture (ideally exceeding Rs. 25/kg). Consequently, vertically integrated players with access to low-cost financing are best positioned for success, while smaller, pure-play operators lacking offtake agreements face significant viability risks.
Above views are of the author and not of the website kindly read disclaimer
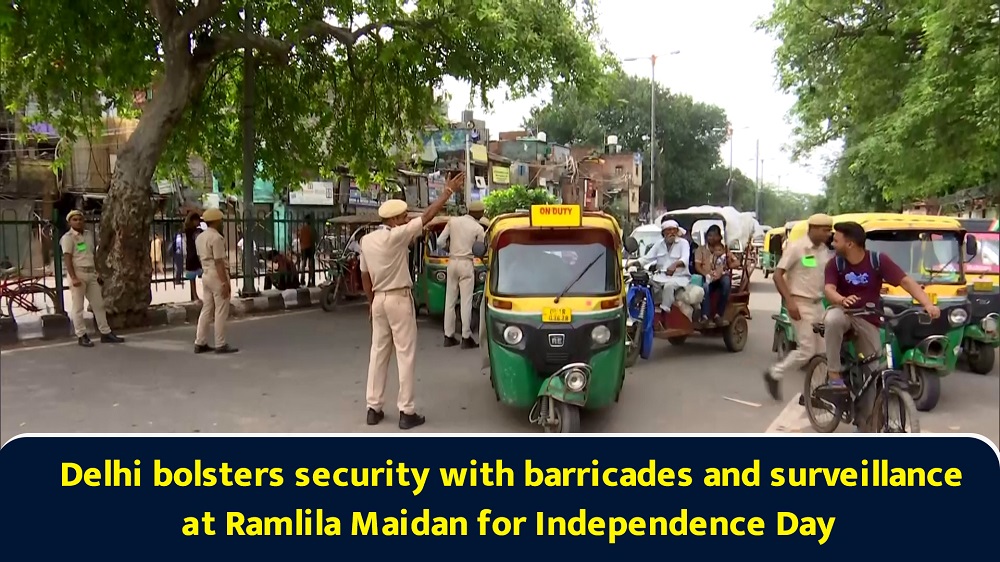
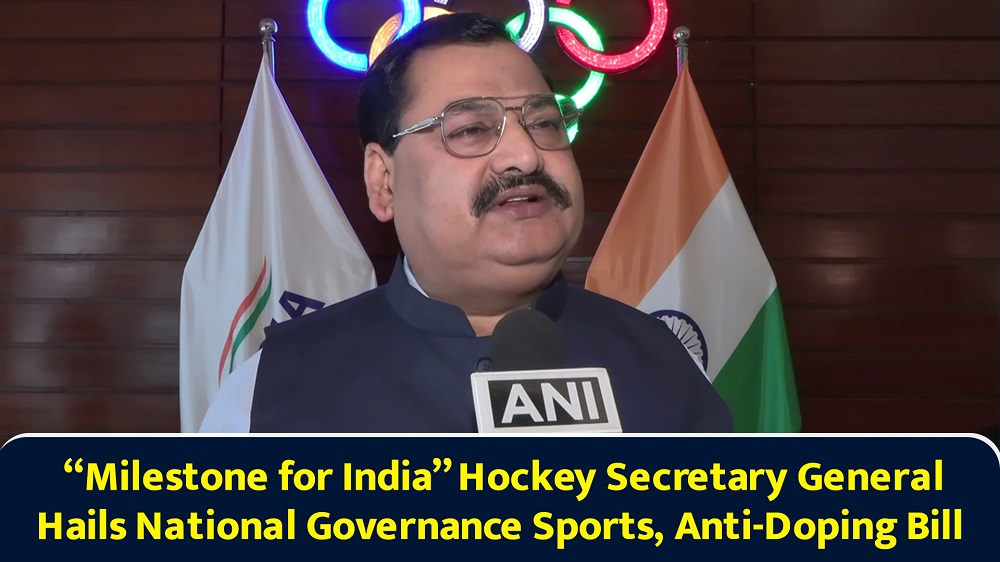
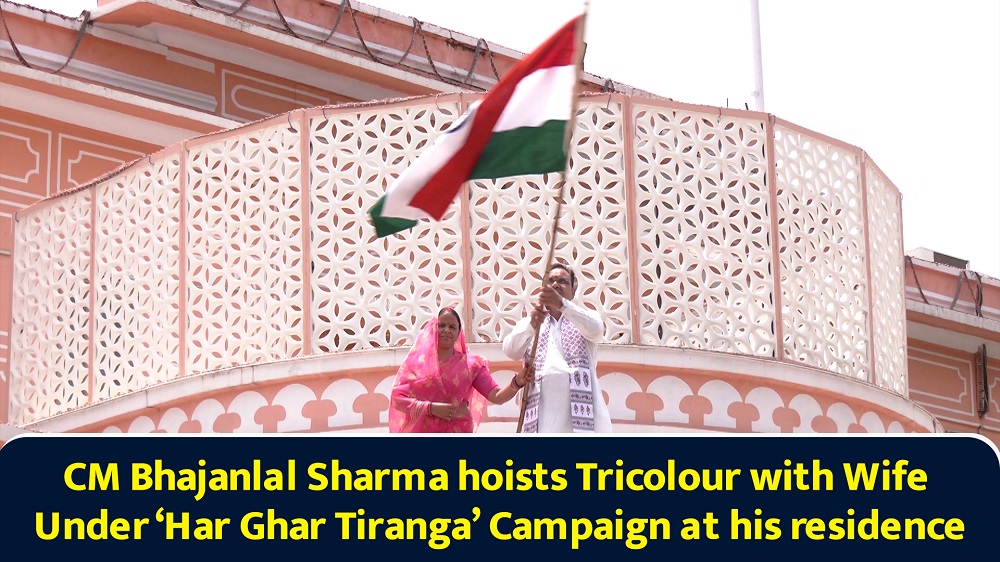
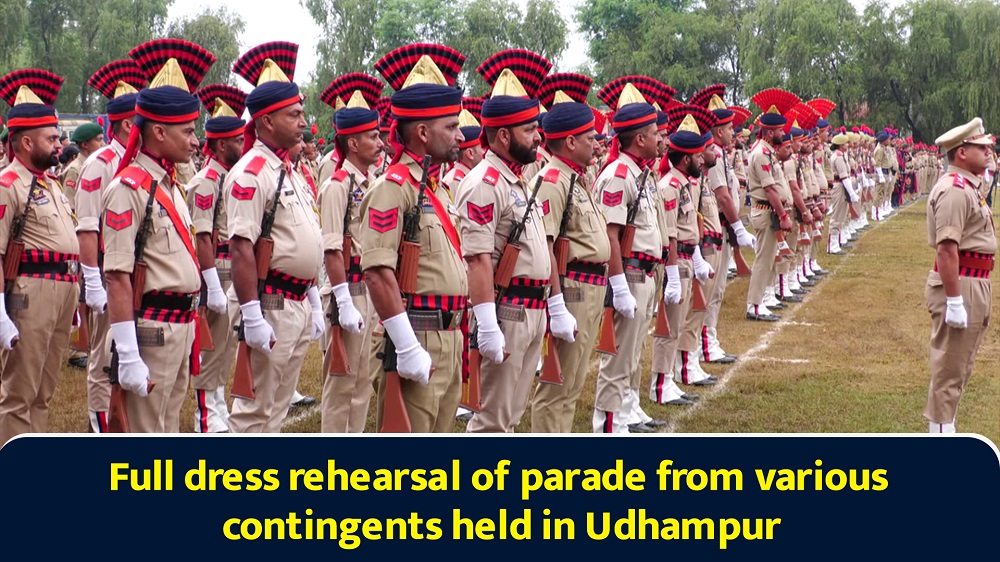
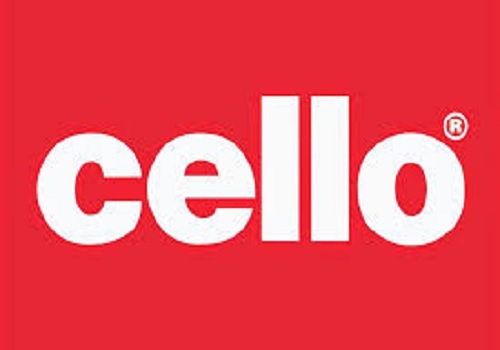
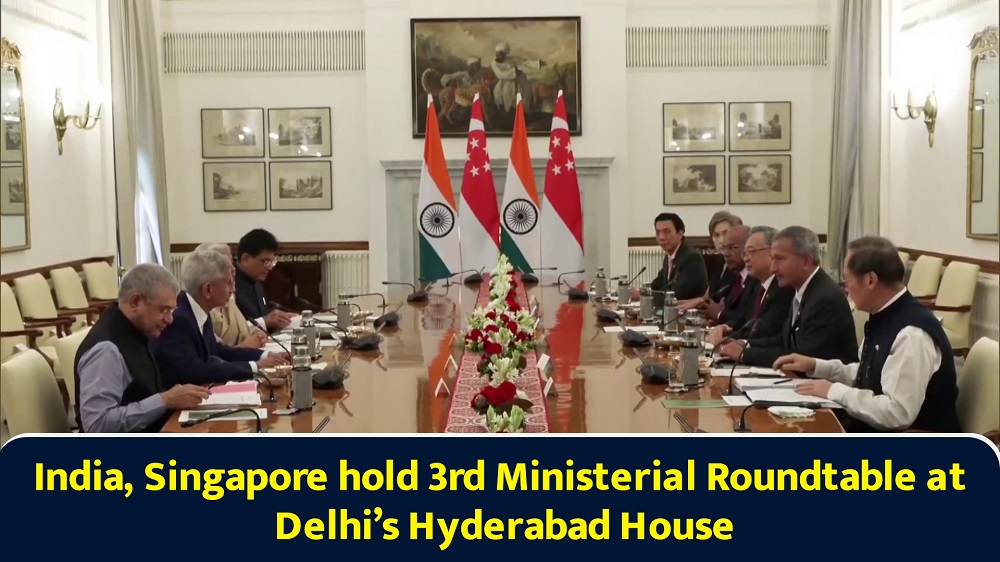
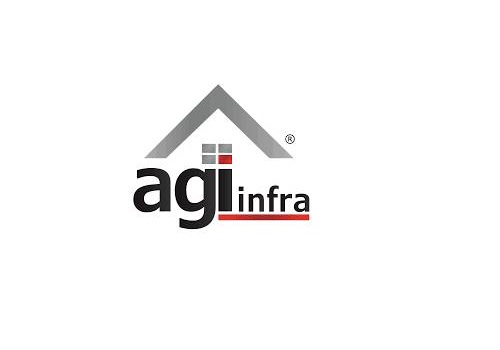
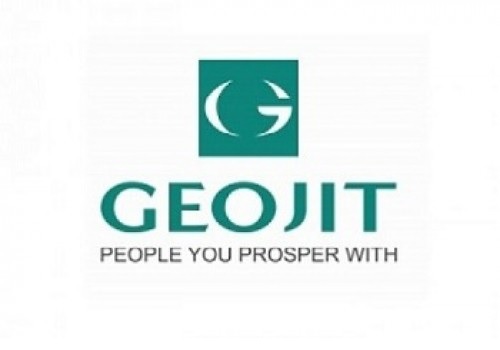
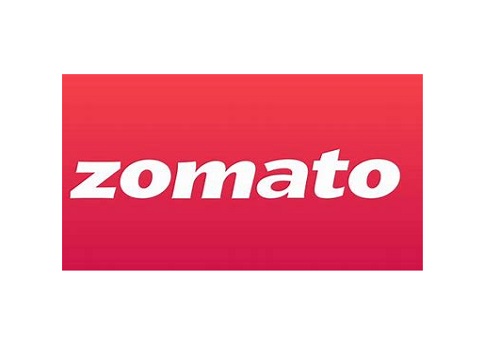
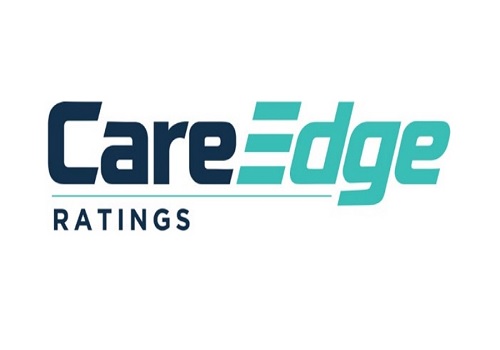