Godavari Biorefineries coming with IPO to raise Rs 572 crore
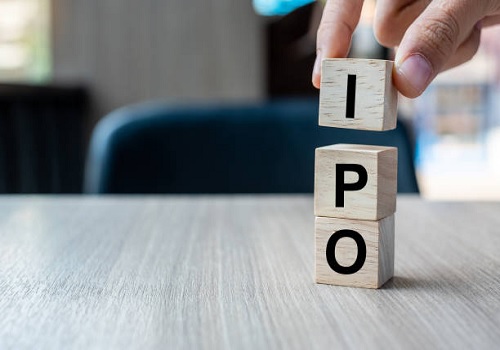
Godavari Biorefineries
- Godavari Biorefineries is coming out with a 100% book building; initial public offering (IPO) of 1,62,57,521 shares of Rs 10 each in a price band Rs 334-352 per equity share.
- Not more than 50% of the issue will be allocated to Qualified Institutional Buyers (QIBs), including 5% to the mutual funds. Further, not less than 15% of the issue will be available for the non-institutional bidders and the remaining 35% for the retail investors.
- The issue will open for subscription on October 23, 2024 and will close on October 25, 2024.
- The shares will be listed on BSE as well as NSE.
- The face value of the share is Rs 10 and is priced 33.40 times of its face value on the lower side and 35.20 times on the higher side.
- Book running lead managers to the issue are Equirus Capital and SBI Capital Markets.
- Compliance Officer for the issue is Manoj Jain.
Profile of the company
Godavari Biorefineries is one of the manufacturers of ethanol based chemicals in India and it is an integrated bio-refinery in India with an installed capacity of 570 KLPD for manufacturing ethanol as at June 30, 2024. It is one of India’s largest producers of ethanol in terms of volume as of March 31, 2024. At the same time, the company was also the largest manufacturer of MPO worldwide in terms of installed capacity, one of only two manufacturers of natural 1,3 butylene glycol and the only company in India to manufacture bio ethyl acetate. It has also set up India’s first bio-based EVE manufacturing facility in India as on March 31, 2024. Its diversified product portfolio comprises of bio-based chemicals, sugar, different grades of ethanol and power. These products find application in a range of industries such as food, beverages, pharmaceuticals, flavours & fragrances, power, fuel, personal care and cosmetics.
The company utilises sugarcane as a feedstock to manufacture a wide range of products, including sugar, ethanol, bio-based chemicals and power and was among the first few companies in India to utilise sugarcane juice and syrup for the production of ethanol. It continuously strives to improve the valorisation of sugarcane through development of down-stream products and increase the diversion of sugarcane towards value added products. For instance, it has been successful in manufacturing a wide range of bio-based chemicals such as ethyl acetate, bio-ethyl acetate, MPO, 1,3 butylene glycol, crotonaldehyde, acetaldehyde, bio-acetic acid, butanol, EVE, and paraldehyde. It is also in the process of exploring the utilisation of grains to manufacture grain-based ethanol.
Its Sameerwadi Manufacturing Facility with a crushing capacity of 18,000 TCD as on June 30, 2024, is among the top fifteen sugar complexes in India in terms of crushing capacity. It also has an environmental clearance to expand crushing capacity up to 25,000 TCD. Through its long history of purchasing sugarcane and continued support provided to the farmers, it has established strong relationships and goodwill among the farmers. Further, it is one of India’s largest producers of ethanol in terms of volume as of March 31, 2024 with an installed capacity of 570 KLPD as at June 30, 2024.
Proceed is being used for:
- Repayment/pre-payment, in full or in part, of certain outstanding borrowings availed by the company
- General corporate purposes
Industry overview
The term biochemical can refer to any chemical compound that is part of the makeup of living cells, in Industrial terms biochemicals are chemicals that are derived from renewable sources, the alternative term used is bio-based chemicals. The bio-based chemicals market has been growing exponentially owing to the increasing need for environmentally sustainable solutions. Bio-based chemicals are produced from both plant- and microorganism-based sources. However, biorefineries primarily use feedstock such as sugar crops (e.g., beet and cane), lignocellulosic crops (e.g., managed forest, short rotation coppice, switchgrass), starch crops (e.g., wheat and maize), perennial grasses and legumes (e.g., ryegrass and alfalfa), aquatic biomass (e.g., algae and seaweed), lignocellulosic residues (e.g., forest residues, stover, and straw), oil crops (e.g., palm and oilseed rape), and organic residues (e.g., industrial, commercial, and postconsumer waste). The most important aspect of bio-based chemicals is the source or the feedstock. Feedstocks for bio-based chemicals can be obtained from three of the major kingdoms of life.
Meanwhile, India is a net exporter of ethyl acetate, mainly exporting to the Europe, Middle East, and Africa. This positive trade balance gives an advantage to Indian players in exploring high-end markets such as Europe where more than half the Ethyl Acetate trade takes place. Many ethyl acetate suppliers have backward integrated ethanol production from molasses; such as Godavari Biorefineries Limited, Jubilant Ingrevia (formerly Jubilant LifeSciences), Dhampur Alcochem, Laxmi Organics, etc. India ethyl acetate market stood at 450.5 KT in 2023 and is expected to grow at a CAGR of 9.0%, from 450.5 KT in 2023 to 693.1 KT in 2028. In terms of values, the market stood at $524.1 million in 2023 at an average price of $1,164 /MT. Looking ahead, the market is expected to continue its growth trajectory, with a projected CAGR of 11.2% from 2023 to 2028, reaching a value of $890.4 million by 2028.
Further, Bio-acetic acid is at emerging phase in India. The India market for bio-acetic acid stood at 437.0 MT in 2023 and is expected to grow at a CAGR of 8.0% from 2023 to 2024, reaching upto 642.3 MT by 2028. The growth and expansion of the Indian pharmaceutical industry is expected to drive the demand for acetic acid. Rising health awareness and continuous research and development in the pharmaceutical industry is driving the industry in India. The Indian government is also implementing policies to promote the growth of the pharmaceutical industry such as infrastructure development and tax incentives. Acetic acid is a key raw material that is used for making Vinyl Acetate Monomer (VAM) which is used in paints, coatings, adhesives, and textiles. The country’s growing construction and automotive industry are driving the demand for VAM thereby driving the demand for bio-acetic acid. The Indian bio-acetic acid market holds immense growth potential, driven by sustainability concerns, government support, and diverse applications.
Pros and strengths
One of the largest producers of Ethanol in terms of volume: The company is one of the manufacturers of ethanol based chemicals in India and it is an integrated bio-refinery in India with an installed capacity of 570 KLPD for manufacturing ethanol as at March 31, 2024. It is one of India’s largest producers of ethanol in terms of volume as of March 31, 2024. At the same time, the company was also the largest manufacturer of MPO worldwide in terms of installed capacity, one of only two manufacturers of natural 1,3 butylene glycol and the only company in India to manufacture bio ethyl acetate. It has also set up India’s first bio-based EVE manufacturing facility in India as on March 31, 2024. As at June 30, 2024, it had an installed capacity of 570 KLPD for ethanol with capacity utilisation of 2.64%, 46.95%, 46.95% and 58.39% for the three months ended June 30, 2024, Fiscals 2024, 2023 and 2022.
Diversified product portfolio: The company has over the years expanded and diversified its manufacturing capabilities and product portfolio and has a diversified product portfolio, which primarily include Bio-based Chemicals, sugar and Ethanol. Its diversified product portfolio has reduced its dependence on any specific product category or products. Bio-chemicals are an emerging focus among manufacturing industries and among the peers, the company has the widest portfolio of bio-based products in India. Across the globe, governments are tightening the regulations on the use of hazardous chemicals. For instance, in India, the Union Cabinet in October 2020 ratified the ban on seven chemicals that are hazardous to the environment listed under the Stockholm Convention. Following strict regulatory changes, the demand for green chemicals is expected to increase in the next decade.
Well-developed in-house research and development capabilities: Research and development of new products to meet its customers’ requirements is a key growth driver of its business. The company has three R&D Facilities which are registered with the Department of Scientific and Industrial Research, Government of India (DSIR) comprising of one R&D Facility located at the Sakarwadi Manufacturing Facility, one located at the Sameerwadi Manufacturing Facility and one R&D Facility located in Navi Mumbai, Maharashtra. Each of its R&D Facilities is equipped with research and development infrastructure which focuses on the development of new products as well as optimizing its manufacturing processes. It regularly monitors and updates its research and development capabilities.
Integrated bio-refinery in India with an installed capacity of 570 KLPD: It is an integrated biorefinery company using sugarcane as a primary feedstock to manufacture a range of products across the value chain including sugar, Ethanol, chemicals, power and other products. Among the peers, the company has the widest portfolio of bio-based products in India. The sugarcane feedstock is processed at its Sameerwadi Manufacturing Facility for the manufacturing of sugar and Ethanol and press mud is intended to be utilised for the manufacturing of compressed biogas. The bagasse is also used for the generation of power. It has the ability to divert syrup/juice to produce different grades of ethanol which helps it to create optionality between production of sugar and ethanol. In Fiscals 2024, 2023 and 2022, it diverted 27.64%, 42.18% and 36.12% of sugar, either as syrup/ juice or as molasses, towards the manufacturing of Ethanol to take advantage of the EBP Program.
Risks and concerns
Significant revenue comes from top 10 customers: The company is dependent on a limited number of customers for a portion of its revenues. The company garnered revenue of 57.00%, 52.15% and 47.92% from top 10 customers in FY24, FY23 and FY22 respectively. It typically does not have firm commitment in the form of long-term supply agreements with most of its key customers and instead rely on purchase orders including through the tender route to govern the volume and other terms of its sales of products. It does not typically have exclusivity arrangements with most of its customers. While it has developed long-term relationships with certain of its customers, there is no commitment on the part of its key customers to continue to place new purchase orders with it and as a result, its cash flow and consequent revenue may fluctuate from time to time.
Procure significant portion of raw material from limited suppliers: The company sources its raw materials (excluding sugarcane) namely, special denatured spirit (SDS), acetic acid, methyl ethyl ketone (MEK) and molasses from a limited number of third-party suppliers from various geographies including India, USA and UAE. The company procures 68.94%, 53.49% and 72.51% of raw material from top 3 suppliers in FY24, FY213 and FY22 respectively. It does not have long-term contracts with its suppliers for such raw materials. It cannot assure that it will be able to procure raw materials that meet the specified quality standards on commercially acceptable terms.
Derive a portion of revenue from few products: The company has historically derived a portion of its revenues from the sale of a few products, namely, sugar, ethyl acetate, ethanol and 3-methyl-3-penten-2-one (MPO). The company garnered revenue of 32.50%, 33.42% and 29.16% from Sugar segment; 14.52%, 15.72% and 23.46% from Ethyl acetate and 28.58%, 28.11% and 25.16% from 1,3 Butylene Glycol in FY24, FY23 and FY22 respectively. Its revenues from these products may decline as a result of increased competition, pricing pressures, fluctuations in demand for or supply of its products which may adversely affect its business, financial condition and results of operations.
Sugar, distillery and cogeneration segments are subject to seasonal vagaries: The company’s production in the sugar, distillery and cogeneration segments are influenced by the availability of its basic raw material i.e., sugarcane. The availability of sugarcane and yield from sugarcane is dependent on various factors such as amount of rainfall in a particular year, quality of sugarcane, harvesting schedules, irrigation techniques and overall weather conditions. The presence of any crop disease, adverse weather conditions such as inadequate rainfall and temperature, floods and drought may affect the volume and quality of sugarcane obtained from farmers, thereby adversely affecting its production and pricing of the sugarcane procured by the company. There can be no assurance that future weather patterns, potential crop disease or the cultivation of certain sugarcane crop varieties will not adversely affect the quantity of sugar, bagasse, molasses and other byproducts that can be recovered in any given harvest. Any shortfall in the desired volume or quality of such products may have an adverse impact on its business, financial condition and results of operations.
Outlook
Godavari Biorefineries manufactures ethanol-based chemicals in India. As of June 30, 2024, the company operates an integrated biorefinery with a capacity of 570 KLPD for ethanol production. The company has three research and development facilities registered with the Department of Scientific and Industrial Research (DSIR): one at the Sakarwadi Manufacturing Facility, one at the Sameerwadi Manufacturing Facility, and one in Navi Mumbai, Maharashtra. On the concern side, the company derives a portion of its revenue from a few customers and the loss of one or more such customers, the deterioration of their financial condition or prospects, or a reduction in their demand for its products may adversely affect its business, results of operations, financial condition and cash flows. Moreover, the company is dependent on a few suppliers for supply of a significant portion of raw materials (excluding sugarcane). Any failure to procure such raw materials from these suppliers may have an adverse impact on its manufacturing operations and results of operations.
The company is coming out with a maiden IPO of 1,62,57,521 equity shares of Rs 10 each. The issue has been offered in a price band of Rs 334-352 per equity share. The aggregate size of the offer is around Rs 543.00 crore to Rs 572.26 crore based on lower and upper price band respectively. On performance front, the company’s revenue from operations decreased by 16.28% to Rs 16,866.65 million in Fiscal 2024 from Rs 20,146.94 million in Fiscal 2023. This was due to a decrease in revenues from its Bio-based Chemicals, sugar and distillery segments. Moreover, the company’s profit for the year decreased by 37.37% to Rs 122.99 million in Fiscal 2024 from Rs 196.37 million in Fiscal 2023.
The company currently manufactures a range of products, primarily consisting of Bio-based Chemicals, Ethanol, sugar and power. The Bio-based Chemicals currently manufactured by it includes ethyl acetate, bio-ethyl acetate, MPO, 1,3 butylene glycol, crotonaldehyde, acetaldehyde, bio-acetic acid, butanol, EVE, and paraldehyde which are downstream products of Ethanol. It intends to expand its distillery capacity from 600 KLPD (as at June 30, 2024) to 1,000 KLPD and have obtained environmental clearance for such expansion. It constantly evaluates opportunities to diversify its product portfolio by adding new products (including downstream and value-added products) which are synergistic with its existing products. The company is well poised and technologically equipped to add additional products in the value chain. For instance, leveraging its manufacturing capabilities and track record, it commenced the manufacture of EVE in Fiscal 2024 and intends to similarly develop products which are synergetic to its existing product portfolio and manufacturing capabilities.
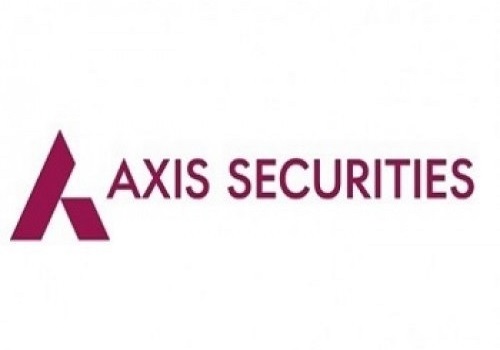
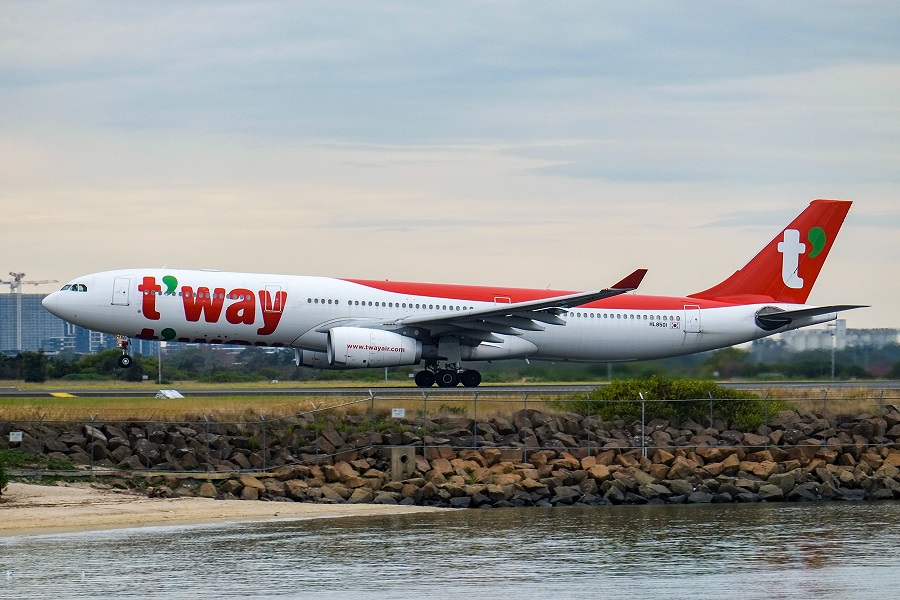
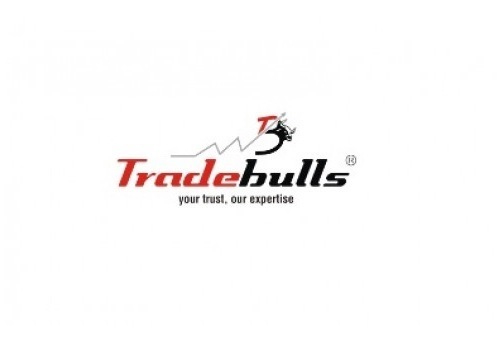
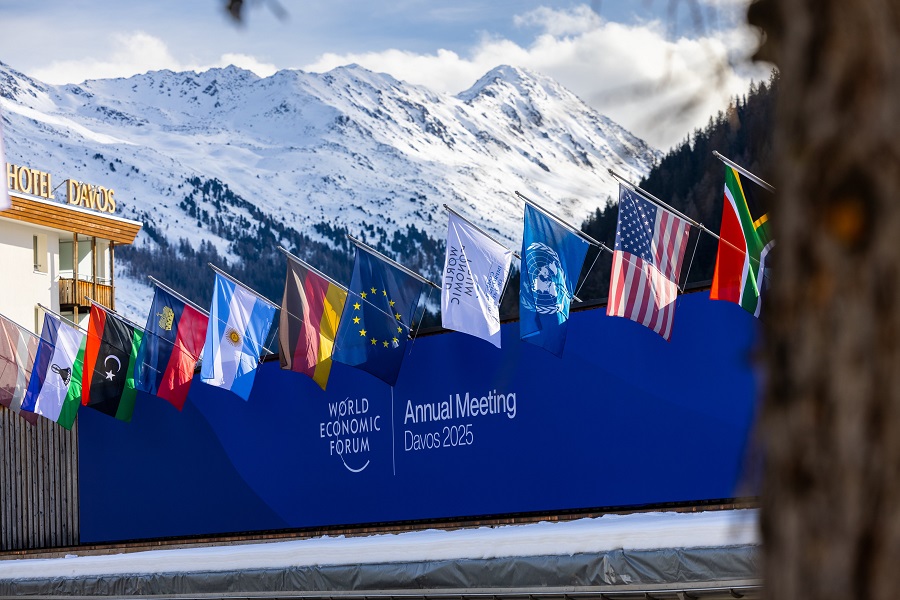
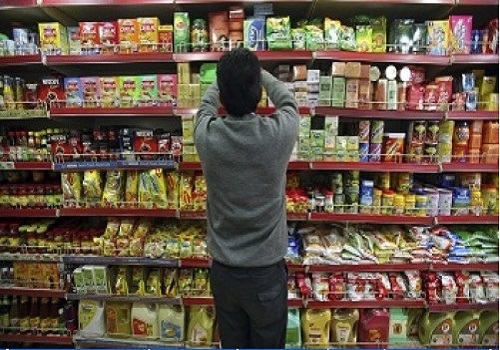
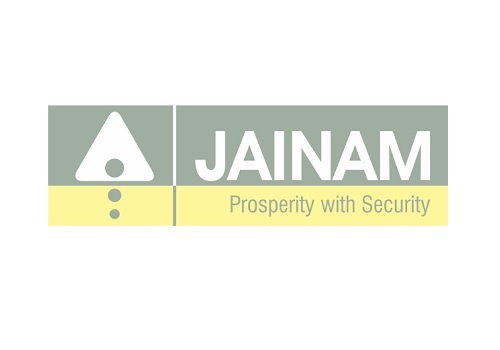
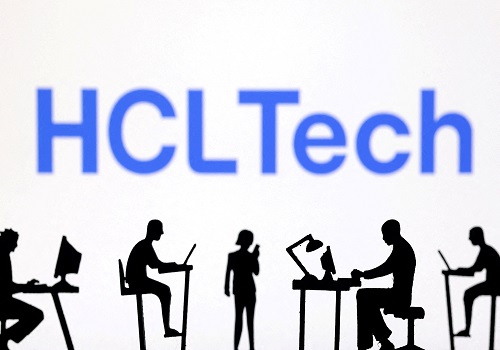
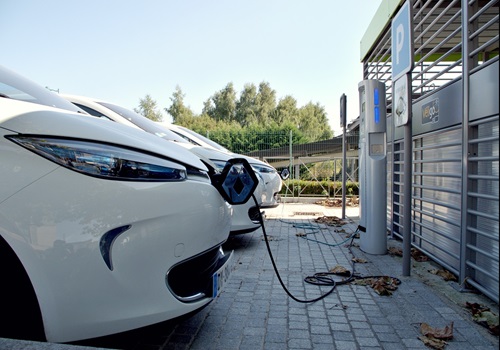
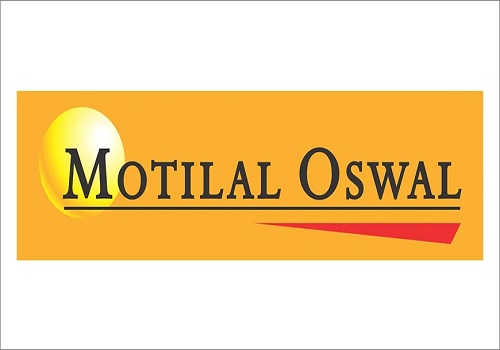
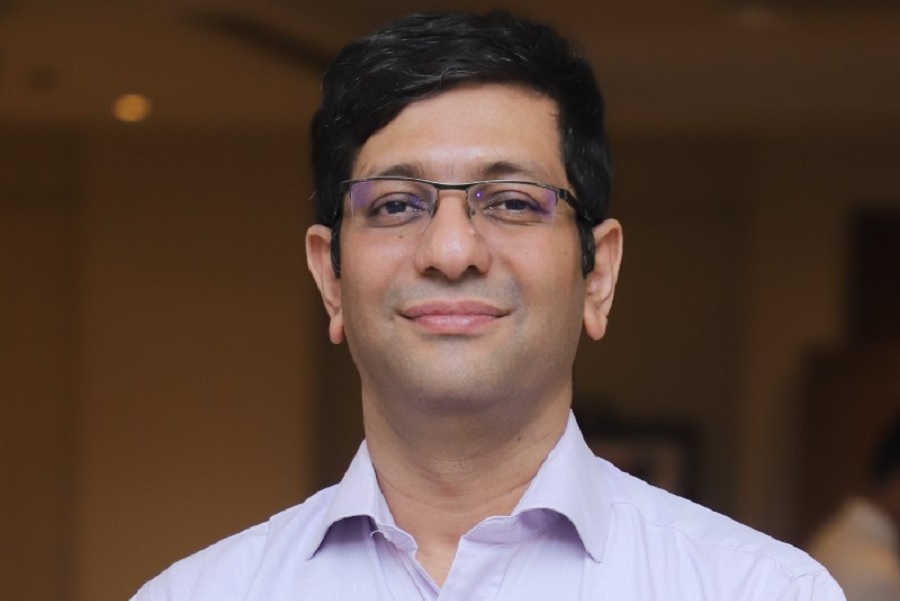