Ratnaveer Precision Engineering coming up with IPO to raise around Rs 165 crore
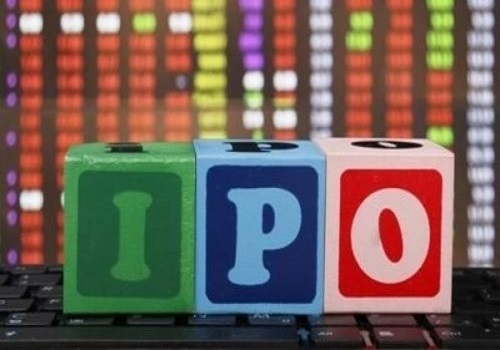
Ratnaveer Precision Engineering
- Ratnaveer Precision Engineering is coming out with a 100% book building; initial public offering (IPO) of 1,68,40,000 shares of Rs 10 each in a price band Rs 93-98 per equity share.
- Not more than 50% of the issue will be allocated to Qualified Institutional Buyers (QIBs), including 5% to the mutual funds. Further, not less than 15% of the issue will be available for the non-institutional bidders and the remaining 35% for the retail investors.
- The issue will open for subscription on September 4, 2023 and will close on September 6, 2023.
- The shares will be listed on BSE as well as NSE.
- The face value of the share is Rs 10 and is priced 9.30 times of its face value on the lower side and 9.80 times on the higher side.
- Book running lead manager to the issue is Unistone Capital.
- Compliance Officer for the issue is Prerana Rajeshbhai Trivedi.
Profile of the company
Ratnaveer Precision Engineering is a stainless steel (SS) product manufacturer focused on producing finished sheets, washers, solar roofing hooks, pipes and tubes. Stainless steel is a value-added product with high corrosion resistant properties. Higher levels of chromium and additions of other alloy elements enhance the corrosion resistance. Compared to traditional steel, stainless-steel has higher resistance to corrosion, superior aesthetic finish and higher life span. These features have helped in increasing the popularity of stainless-steel across the world. Globally, cold rolled flat products are the largest produced stainless-steel product in the world, followed by hot rolled coils, and steel wire rods & bars. The company operates out of four manufacturing units, out of which two (Unit-I and Unit-II) are located at GIDC, Savli, Vadodara, Gujarat, one (Unit-III) is located at Waghodia, Vadodara, Gujarat and the other one (Unit-IV) is located at GIDC, Vatva, Ahmedabad, Gujarat. Its manufacturing units are strategically located with availability of transportation, which facilitates convenient transportation of its products.
The company manufactures SS finishing sheets, SS washers and SS solar mounting hooks at its Unit I and SS pipes & tubes at its Unit II. Unit III and Unit IV are dedicated for the backward integration process. Unit III is the melting unit where it melts steel scrap and turns it into steel ingots and Unit IV is the rolling unit where flat ingots are further processed to turn them into SS sheets which are the raw material for SS washers. Its Units are supported by infrastructure for storage of raw materials, manufacturing of its products, storage of finished goods, together with a quality control and R&D laboratory. The company is one of the few companies who has a backward integration model. This backward integration model is one of its major strengths and has helped it in maximizing the returns on its investments. While its two units (Unit I and II) are dedicated for manufacturing the products which are offered to its customers, the other two units (Unit III and IV) are dedicated towards processing the byproducts generated in manufacturing its products and converting it back into the raw material for its products. Its products find application across various industries including automotive, solar power, wind energy, power plants, oil & gas, pharmaceuticals, sanitary & plumbing, instrumentation, electro mechanics, architecture, building & construction, electrical appliances, transportation, kitchen appliances, chimney liners, etc. Its products are used in both commercial and residential sector and are sold within India and overseas.
Proceed is being used for:
- Funding working capital requirements of the company.
- General corporate purposes.
Industry overview
Since 2000, steel production in the country has seen a phenomenal increase as the sector witnessed high investments in capacity addition as well as technology up-gradation. In 2018, India surpassed Japan to become the second largest steel producer in the world, after China. According to World Steel Association (WSA), India produced 125.3 Mn tons of crude steel in CY 2022 and accounted for 7% share in global crude steel production. According to WSA’s June 2023 update, India produced approximately 67.9 Mn tons of steel during January – June 2023 period, which nearly 7.4% higher than same period previous year. Unless there are no major disruptions, Indian steel industry would end the year with approximately 136 Mn tons of crude steel. In 2022, India’s crude steel production registered a y-o-y growth of 6% against 18% increase in the previous year while it grew at a CAGR of 4% between 2018-22. Presence of such a vast primary steel manufacturing infrastructure coupled with the low-cost worker has also helped in the growth of secondary and finished steel products. On consumption side, India is also the second largest consumer of finished steel. The emergence of a middle-class consumer segment has altered the consumption landscape in India.
The Indian stainless-steel sector, the second largest producer (in 2022) and consumer in the world, has a total manufacturing installed capacity of more than 6.5 Mn tons of stainless steel annually. The past 4 year data reveals that the country's stainless steel production in FY19 touched a level of 5.10 million tonnes. However, in the following two years, production volumes dropped to 3 million tonnes and 2.71 million tonnes respectively in FY20 and FY21, mainly hit by the Covid-19 waves. In FY22, production again picked up and was recorded at 3.5 million tonnes, recording 29% y-o-y growth compared to FY21. Since 2011, stainless-steel production has increased at a CAGR of 7.8% per annum from ~2.16 Mn Tonnes in 2011 to 3.92 Mn Tonnes in 2019. Barring 2020 for pandemic led decline, India’s stainless-steel (SS) production has increased steadily between 2014-21. In 2020, India stainless steel production observed -19.4% over 2019 owing to Covid-19 pandemic induced depressed market condition. However, the industry rebounded well in CY 2021 as India’s annual domestic stainless-steel production reached approximately 4.25 Mn tons, increasing by nearly 26% over previous year production.
Pros and strengths
Synergistic Business Model focused on Backward Integration: The company has developed a synergistic system of backward integration whereby it processes the waste being generated in manufacturing of its products for converting back into the raw material which is utilized again in manufacturing. Thus, the raw material required is also being generated in-house, while the waste being produced in the manufacturing process is being completely utilized, ensuring economies of scale and minimal wastage. It manufactures SS Finishing Sheets, SS Washers and SS Solar roofing hooks at Unit I. The scrap generated primarily in the manufacturing process of SS Washers and SS Solar roofing hooks is sent to Unit III where this scrap and the scrap purchased from third parties is organized, categorized and melted in heating furnaces and cooled naturally to form the SS ingots. These ingots are sent for job work for conversion into flat ingots.
Wide product portfolio and multiple designs: The company had started its business activities with manufacturing of SS washers and has since branched out to manufacturing SS finishing sheets, SS solar roofing hooks, SS tubes and pipes which has enabled it to diversify its product portfolio manifold. Its portfolio comprises of over 2,500 SKUs of SS washers. Having a wide range of products not only enables it to meet the trends and ever changing demands of its customers but also gives the company an edge to efficiently compete with its competitors. Its product portfolio also includes diversified variety of stainless steel pipes in various specifications and sizes having wide applications in varied industries. Its constant efforts are focused towards identifying the customer requirements and introducing high quality products which are in demand.
R&D set up for new product development: The company has an in-house R&D facility at Unit I wherein it develops tools and molds for its products. To enhance its product offerings, it has leveraged its manufacturing ability to evolve by virtue of investing in the Research and Development activities. It is focused on undertaking dedicated R&D in its existing products and development of new products and designs in areas where there is significant growth potential and would cater to needs of its customers. It connects with its customers from time to time and understand their requirements on the basis of which it develop new and advanced product designs more suitable to its customers.
Customer Diversification: The company sells its products both in the domestic as well as international markets. In the domestic market, it sells its products to the manufacturers as well as traders/ stockists and end customers whereas in the international market it supplies its products through traders/stockists in the International market. It has been exporting since incorporation and as on March 31, 2023, some of the countries it is exporting to including but not limited to Germany, UK, Spain, Netherland, etc. Its diversified customer base signifies its non-dependence on any single customer and thereby hedges its business operations from potential customer specific risk, sector specific risks, including but not limited to policy announcements, change in global markets and international relations etc.
Risks and concerns
Dependent on few customers for major part of revenues: There is no direct/ indirect relationship between such entities and the Company, Promoter, Directors and Promoter Group members. The company presently does not have any long-term or exclusive arrangements with any of its customers and it cannot assure that it will be able to sell the quantities it has historically supplied to such customers. In the event its competitors’ products offer better margins to such customers or otherwise incentivize them, there can be no assurance that its customers will continue to place orders with it. Most of its transactions with its customers are typically on a purchase order basis without any commitment for a fixed volume of business. There can also be no assurance that its customers will place their orders with it on current or similar terms, or at all. Further, its customers could change their business practices or seek to modify the terms that it has customarily followed with them, including in relation to their payment terms.
Business working capital intensive: The company's business requires significant amount of working capital primarily as a considerable amount of time passes between purchase of raw materials and collection of receivables post sales to customers. As a result, it is required to maintain sufficient stock at all times in order to meet manufacturing requirements as well as extend credit period to customers as per the industry practice, thus increasing its storage and working capital requirements. Consequently, there could be situations where the total funds available may not be sufficient to fulfil its commitments and hence it may need to incur additional indebtedness in the future or utilize internal accruals to satisfy its working capital needs. Its future success depends on its ability to continue to secure and successfully manage sufficient amounts of working capital.
High volume-low margin business: The company’s business is a high-volume low margin business. Its inability to regularly grow its turnover and effectively execute its key business processes could lead to lower profitability and hence adversely affect its operating results, debt service capabilities and financial conditions. Due to the nature of the products it manufacture, sell and due to high competition, it may not be able to charge higher margins on its products. Hence, its business model is heavily reliant on its ability to effectively grow its turnover and manage its key processes including but not limited to procurement of raw material and timely sales / order execution. As part of its growth strategy, it aims to improve its functional efficiency and expand its business operations. Its growth strategy is subject to and involves risks and difficulties, many of which are beyond its control and, accordingly, there can be no assurance that it will be able to implement its strategy or growth plans or complete them within the timelines.
Operate in highly competitive and fragmented industry: The company operates in an industry which is highly competitive and fragmented and it competes with a range of organized and unorganized players, both at the national and regional level. Further, while it has an expanding portfolio of products, its competitors may have the advantage of focusing on concentrated products. Further, it compete against established players also, which may have greater access to financial, technical and marketing resources and expertise available to them than it in the products and services in which it compete against them. Further, industry consolidation may affect competition by creating larger, more homogeneous and potentially stronger competitors in the markets in which it compete. Its competitors may further affect its business by entering into exclusive arrangements with its existing or potential clients. There can be no assurance that it will be able to compete successfully against such competitors or that it will not lose its key core employees, associates or clients to such competitors. Additionally, its ability to compete also depends in part on factors outside its control, such as the availability of skilled resources, pricing pressures in the staffing industry and the extent of its competitors’ responsiveness to their client’s needs.
Outlook
Incorporated in 2002, Ratnaveer Precision Engineering manufactures stainless steel finished sheets, washers, solar roofing hooks, pipes, and tubes. The company manufactures stainless steel-based products for automotive, solar power, wind energy, power plants, oil & gas, pharmaceuticals, sanitary & plumbing, instrumentation, electromechanics, architecture, building & construction, electrical appliances, transportation, kitchen appliances, chimney liners, and other industries. It has 4 manufacturing units out of which two units; Unit-I and Unit-II are located at GIDC, Savli, Vadodara, Gujarat, Unit-III is located at Waghodia, Vadodara, Gujarat, and Unit-IV is located at GIDC, Vatva, Ahmedabad, Gujarat. The company manufactures SS finishing sheets, SS washers, and SS solar mounting hooks at Unit I and SS pipes & tubes at Unit II. Unit III and Unit IV are dedicated to the backward integration process. Unit III is the melting unit where melted steel scrap is turned into steel ingots, and Unit IV is the rolling unit where flat ingots are further processed to turn them into SS sheets which are the raw material for SS washers. On the concern side, the company’s operations involve extending credit for extended periods of time to its customers in respect of its products and consequently, it faces the risk of non-receipt of these outstanding amounts in a timely manner or at all, particularly in the absence of long-term arrangements with its customers. Besides, there have been some instances of delay/ default in payment of statutory dues by the company in the past which were not material in nature and the same were regularised subsequently.
The issue has been offered in a price band of Rs 93-98 per equity share. The aggregate size of the offer is Rs 156.61 crore to Rs 165.03 crore based on lower and upper price band respectively. On the financial front, the company’s total revenue increased by Rs 526.73 million, or by 12.29%, from Rs 4,284.72 million in the Financial Year 2022, to Rs 4,811.45 million in the Financial Year 2023. The company has recorded an increase in its profit by Rs 155.68 million or by 164.29% from Rs 94.76 million in Financial Year 2022 to Rs 250.44 million in Financial Year 2023. Meanwhile, the company’s strategy is focused towards introducing new product designs to cater to the requirements of its customers as well as garnering the attention of more customers. This helps in strengthening the relationship with the existing customer network through a wide range of products while also onboarding new customers from untapped geographies.
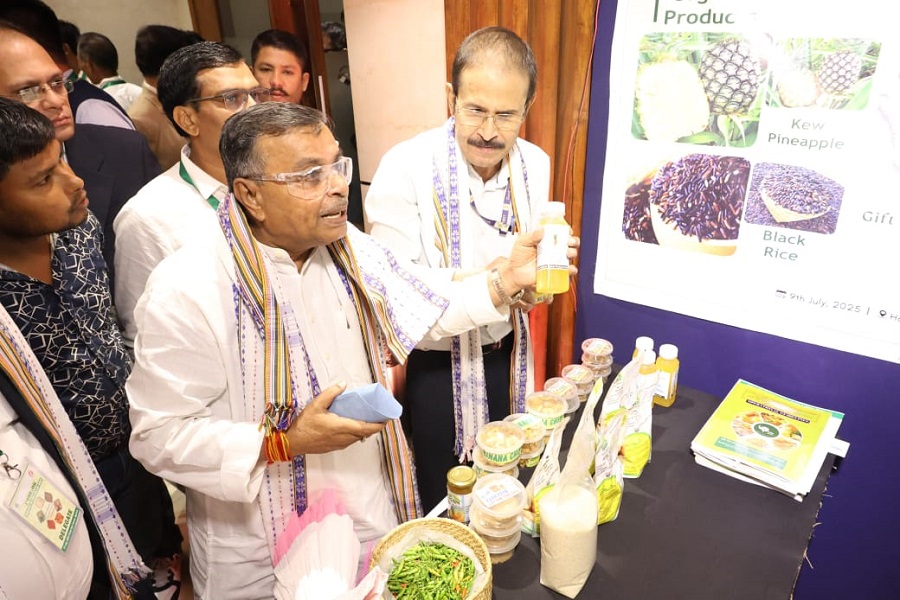
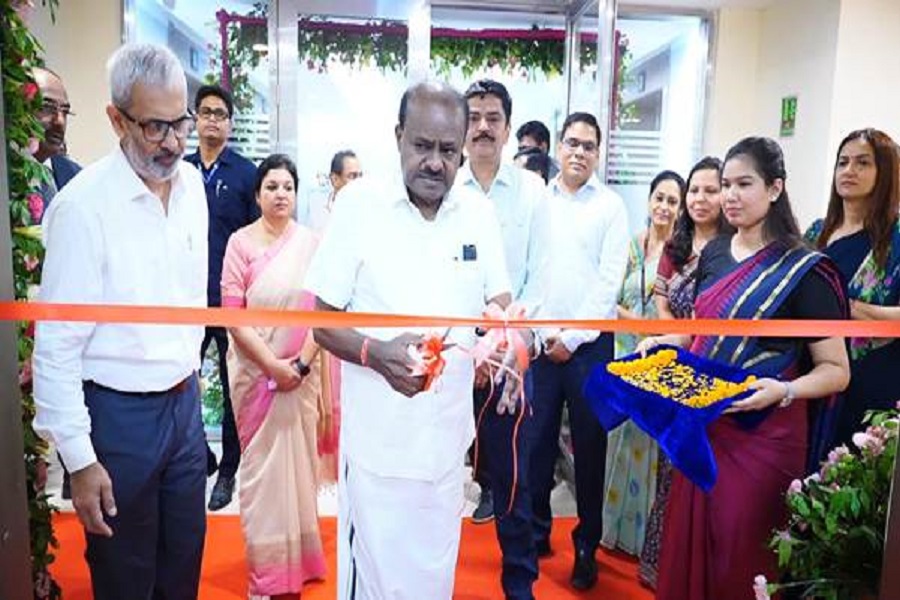
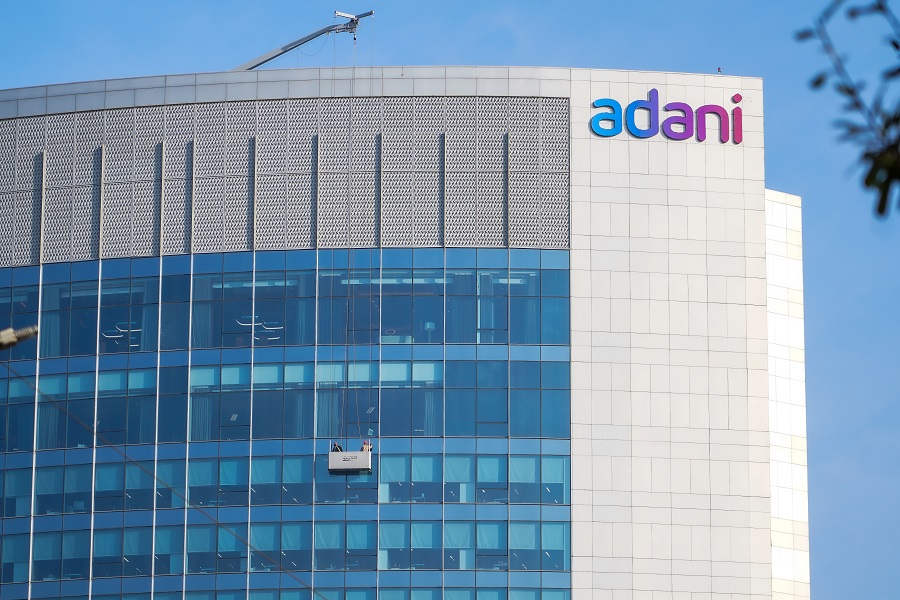
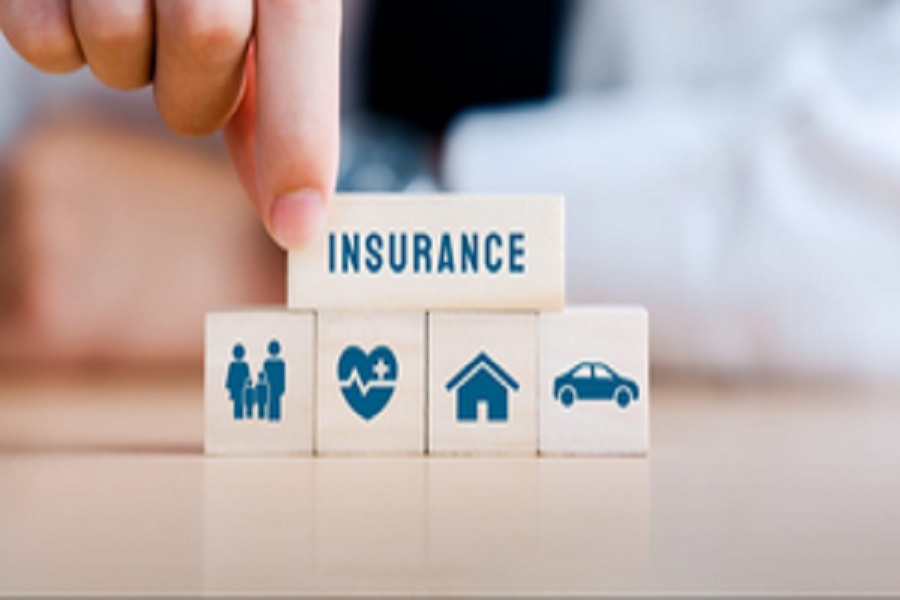
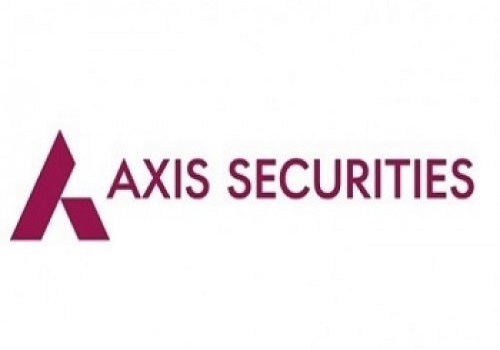
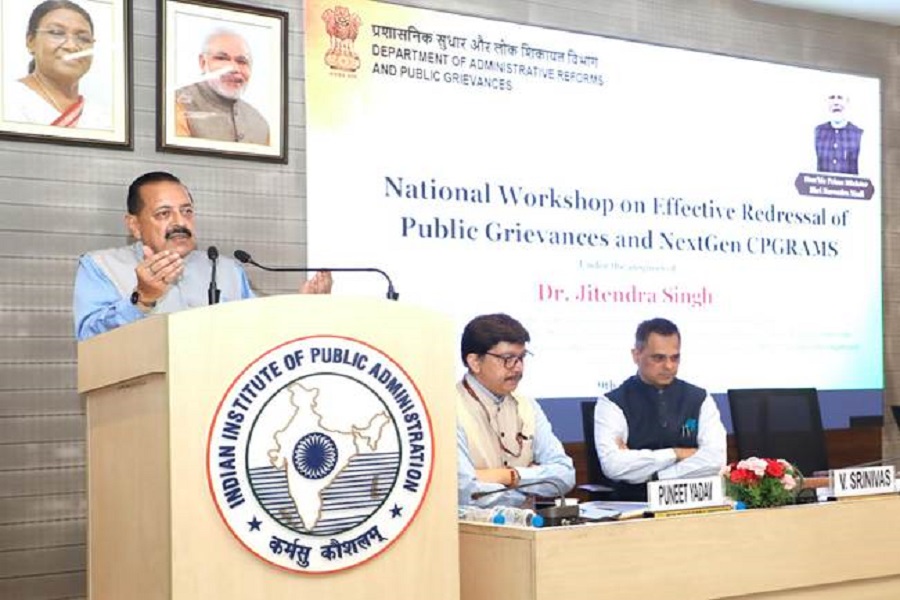
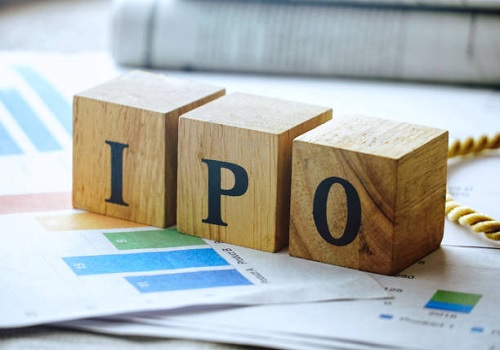
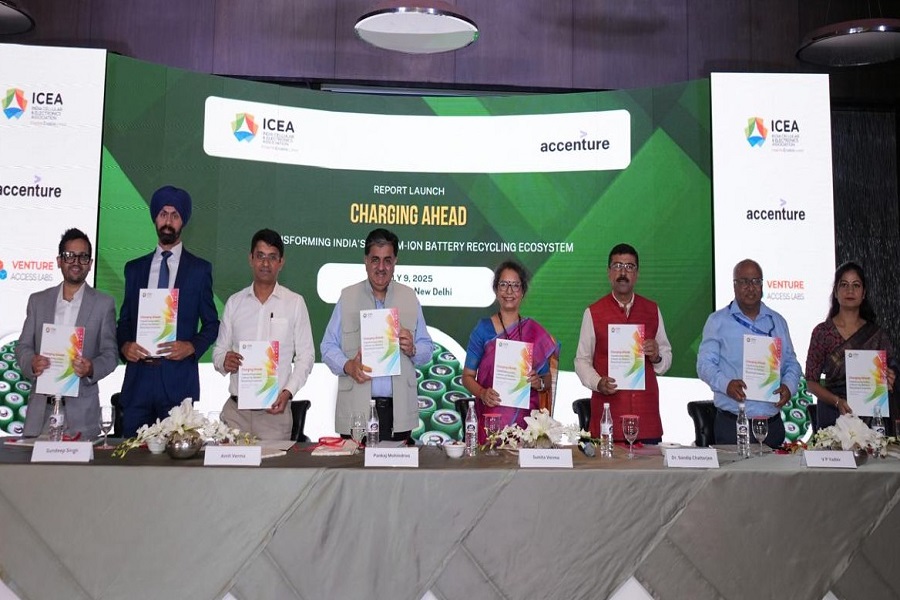
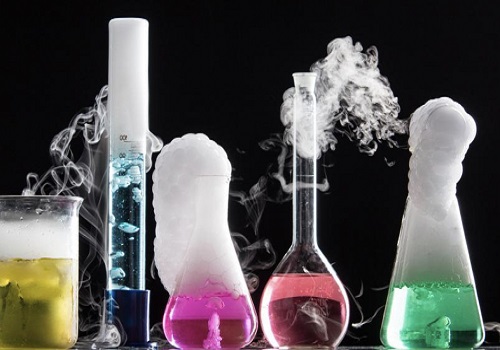
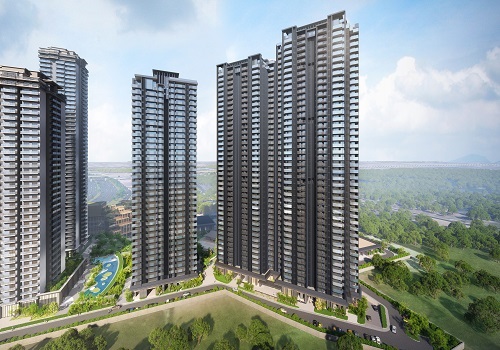