Mangalam Worldwide coming with an IPO to raise Rs 65.58 crore
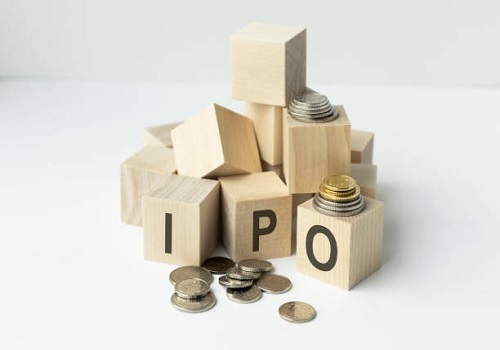
Mangalam Worldwide
-
Mangalam Worldwide is coming out with an initial public offering (IPO) of 64,93,200 equity shares of face value of Rs 10 each for cash at a fixed price of Rs 101 per equity share.
-
The issue will open on June 30, 2022 and will close on July 4, 2022.
-
The shares will be listed on NSE Emerge Platform.
-
The share is priced 10.10 times higher to its face value of Rs 10.
-
-
-
Book running lead manager to the issue is Beeline Broking.
-
Compliance Officer for the issue is Fageshkumar Rameshbhai Soni.
Profile of the company
The company is mainly engaged in manufacturing of Stainless Steel (SS) Billets and rolling of SS Flat Bars with its fully integrated infrastructure consisting of steel melting shops, rolling mills and finishing machines at its plants located at Halol (Unit-I) and Changodar (Unit-II), Gujarat. The company also does the manufacturing of Stainless Steel (SS) Billets on job work basis. To cater the demand of customers for SS Round bars and SS Bright bars, it get manufacturing of such products on job work basis from third party manufacturers. The company is also engaged in trading of steel - scrap, ferro alloys, etc.
The company manufacture wide range of stainless steel of 200 series, 300 series (including series 304 and series 316), 400 series -grades in Austenitic, Ferritic, Martensitic and special chemical composition grades steel like 17/4 PH, Duplex and Super duplex Steel. The company with sound infrastructure, zero tolerance quality policies and with its energetic team of experts, it make sure that it can fulfill any special customer requirements for various critical product applications. The company is Quality Management System certified company and holding ISO 9001:2015, ISO 45001:2018, ISO 14001:2015 certificates.
The company’s plants are located at Halol (Unit I) and Changodar (Unit II). Unit I is having installed manufacturing capacity of 66000 MT/p.a. of Stainless Steel (SS) Billets of 200 series, 300 series (including series 304 and series 316), 400 series and out of which 200 series SS Billets is captively consumed in Unit II. Its Unit II is having installed rolling capacity of 90,000 MT/p.a. of SS Flat bars. Its products are used across industries like food and dairy equipments, Utensils, oil and gas, aerospace and medical devices among others. Its major customers are spread across states Rajasthan, Gujarat, Maharashtra and Uttarpradesh. Recently, it has also started exporting its products to Brazil.
Proceed is being used for:
-
Meeting working capital requirements.
-
General corporate purpose.
-
Meeting public issue expenses.
Industry overview
The Indian steel industry is modern with state-of-the-art steel mills. It has always strived for continuous modernisation of older plants and up-gradation to higher energy efficiency levels. Indian steel industry is classified into three categories - major producers, main producers and secondary producers. In FY21, the production of crude steel and finished steel stood a 102.49 Million Tonnes and 94.66 Million Tonnes, respectively. Crude steel production is expected to reach 112-114 Million tonne, an increase of 8-9% YoY in FY22. The consumption of finished steel stood at 93.43 Million Tonnes in FY21. Between April 2021 and September 2021, finished steel consumption stood at 49.11 Million Tonnes. In May 2021, finished steel production stood at 7.8 Million Tonnes. In June 2021, SAIL’s crude steel production stood at 1.30 Million Tonnes and saleable steel production was 1.27 Million Tonnes. Exports and imports of finished steel stood at 7.75 Million Tonnes and 2.37 Million Tonnes, respectively, in FY22 (until September 2021). In April 2021, India’s export rose by 121.6% YoY, compared with 2020. In FY20, India exported 8.24 Million Tonnes of finished steel.
Government has taken various steps to boost the sector including the introduction of National Steel Policy 2017 and allowing 100% Foreign Direct Investment (FDI) in the steel sector under the automatic route. According to the data released by Department for Promotion of Industry and Internal Trade (DPIIT), between April 2000 and June 2021, Indian metallurgical industries attracted FDI inflows of $ 16.0 billion. The Government’s National Steel Policy 2017 aims to increase the per capita steel consumption to 160 kgs by 2030-31. The Government has also promoted policy which provides a minimum value addition of 15% in notified steel products covered under preferential procurement. In 2019, the Government introduced Steel Scrap Recycling Policy with an aim to reduce import. The industry is also benefitting from the developments happening across various industries. The new Vehicle Scrappage policy will help in reducing the steel prices since the policy enables recycling the materials used in old vehicles. In the healthcare front, major steel producers are now exceeding their production capacities to produce oxygen cylinders for COVID patients. In 2021, Indian Railways is planning to procure over 11 lakh tons of steel from Steel Authority of India (SAIL) for the track renewal and laying new lines across the country.
Pros and strengths
Prime location of factory: The company’s Manufacturing Unit I is located at Halol (Gujarat) and Unit II is located at Changodar (Gujarat). Its Manufacturing units are established in industrial estate which is providing developed plots and ready sheds for setting up industries throughout the state. In this estate all the infrastructure facilities such as power supply, roads, water supply etc. are developed. Its manufacturing units enjoys the good connectivity through National Highway roads and railway, which makes the movements of the raw-material as well as finished goods easy and comfortable. Thus it helps in smooth procurement of raw material from the various suppliers spread in the states like Gujarat, Maharashtra and Rajasthan and dispatch of finished goods to its various customers located in the state of Rajasthan, Gujarat, Maharashtra and Uttarpradesh.
Scalable business model: The company’s business model is currently driven by the demand of its customers in different industry segments like food and dairy equipments, Utensils, oil and gas, aerospace and medical devices among others and comprises of optimum utilization of its procuring abilities, such that its customer is provided with the required goods with minimal delays, and thus achieving consequent economies of scale. Its procurement team’s ability and the business model has proved successful and scalable for it, and it has accordingly established relationships with customers in different industry segments like food and dairy equipments, Utensils, oil and gas, aerospace and medical devices among others. It can scale upward with the growth of various industries, thereby allowing it to increase its scale of operations in each of the products that it is producing especially Stainless Steel (SS) Billets and rolling of SS Flat bars.
Long term relationship with customers: The company has long term relationship with its customers. The business model is based on client relationships that are established over period of time rather than a project-based execution approach. A long-term client relationship with large clients fetches better dividends. Long-term relations are built on trust and continuous maintaining of the requirements of the customers. It forms basis of further expansion for the company, as it is able to monitor a potential product/ market closely.
Risks and concerns
Require high working capital: The company’s business demands substantial funds towards working capital requirements. In case there are insufficient cash flows to meet its working capital requirement or it is unable to arrange the same from other sources or there are delays in disbursement of arranged funds, or it is unable to procure funds on favorable terms, at a future date, it may result into its inability to finance its working capital needs on a timely basis which may have an adverse effect on its operations, profitability and growth prospects.
Rely on third parties for manufacturing products of company: To cater the demand of customers for SS Round bars and SS Bright bars, the company get manufacturing of such products on job work basis from third party manufacturers to whom it provide the requisite billets. Any decline in the quality of products manufactured or delay in delivery of products by such parties, or rise in job work charges may adversely affect its operations. Further there can be no assurance that such parties shall continuously provide their services or would not cater to demand of competitors. Any withdrawal of services from such manufacturers or supply of services to competitors at better rates may adversely affect its result of operations and future prospects. Further it is also exposed indirectly to the risks of these manufacturers.
Changes in technology: The company’s future success will depend in part on its ability to respond to technological advances and emerging steel Industry standards and practices on a cost-effective and timely basis. Changes in technology and product preferences may make newer steel units or equipment more competitive than its or may require it to make additional capital expenditures to upgrade its facilities. If it is unable to adapt in a timely manner to changing market conditions, customer requirements or technological changes, its business, financial performance and the trading price of its Equity Shares could be adversely affected.
Outlook
Mangalam Worldwide is engaged in the manufacturing of stainless steel (SS). The company manufactures Stainless Steel (SS) Billets and SS Flat Bars. The company is also engaged in the trading of steel - scrap, ferro alloys, etc. It has two Plants, located at Halol (Unit I) and Changodar (Unit II). Unit I has an installed manufacturing capacity of 66000 MT/p.a. of Stainless Steel (SS) Billets and Unit II is having installed rolling capacity of 90,000 MT/p.a. of SS Flat bars. The company's customers have spread across states Rajasthan, Gujarat, Maharashtra and Uttarpradesh in different industry segments like food and dairy equipment, Utensils, oil and gas, aerospace and medical devices among others. It is also exporting the products to Brazil. The company is dedicated towards quality of its products which has helped it to maintain long term relations with its customers and has also facilitated it to entrench with new customers. On the concern side, the company operate in a labour-intensive industry and it hire casual labour to work at its factory. In the event of a labour dispute, if it is unable to successfully negotiate with the workmen, it could result in work stoppages or increased operating costs as a result of higher than anticipated wages or benefits. Besides, the company may require additional financing for its business operations and the failure to obtain additional financing on terms commercially acceptable to it may adversely affect its ability to grow and its future profitability.
The company is coming out with a maiden IPO of 64,93,200 equity shares of Rs 10 each at a fixed price of Rs 101 per share to mobilize around Rs 65.58 crore. On performance front, the total revenue from operations for the year ended on FY 2020-21 was Rs 30,191.90 lakh as compared to Rs 32,693.14 lakh during the FY 2019-20 showing a decrease of 7.65%. Profit after Tax (PAT) increased from Rs 147.29 lakh in the FY 2019-20 to Rs 265.18 lakh in FY 2020-21 showing increase of 80.04%. Meanwhile, the company constantly endeavors to improve its production process, skill up-gradation of workers to optimize the utilization of resources. It regularly analyse its material procurement policy and manufacturing process to de?bottle neck the grey areas and take corrective measures for smooth and efficient working thereby putting resources to optimal use. It is planning to expand its current business operations by optimum utilization of resources.
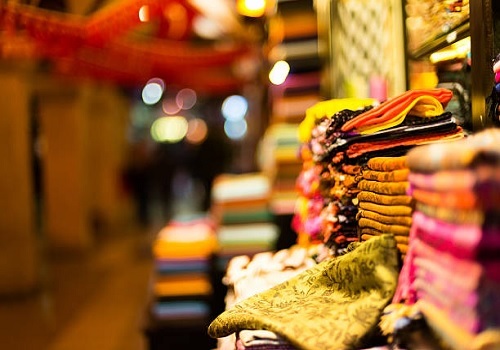
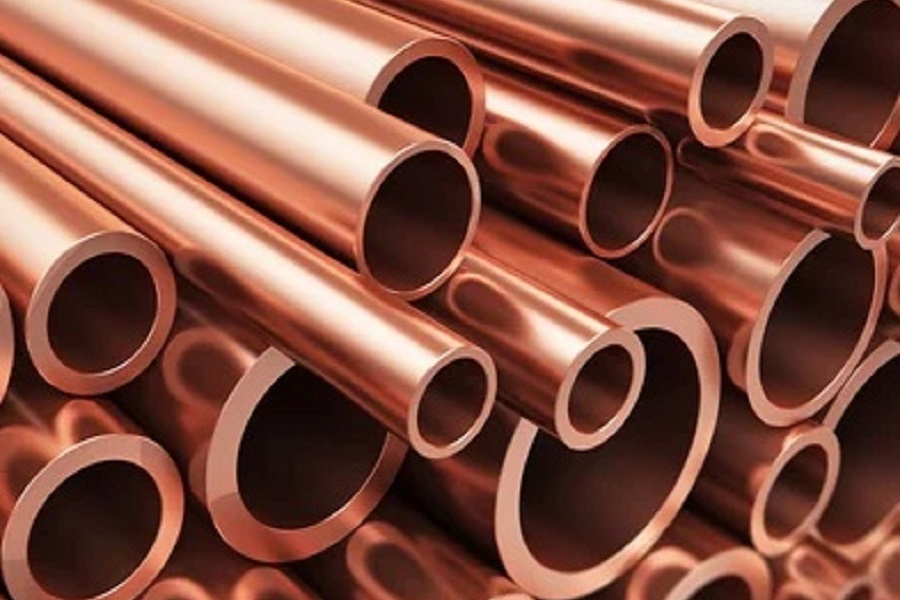
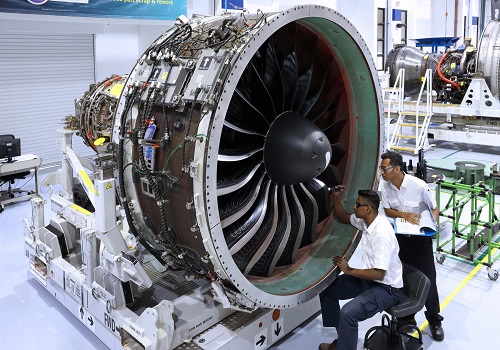
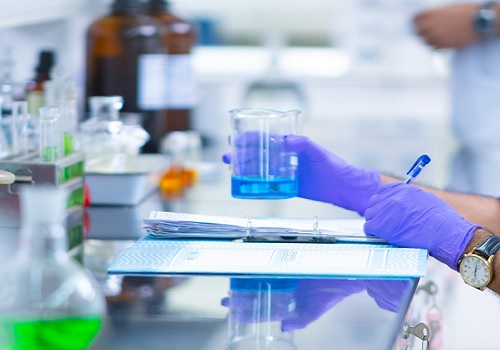
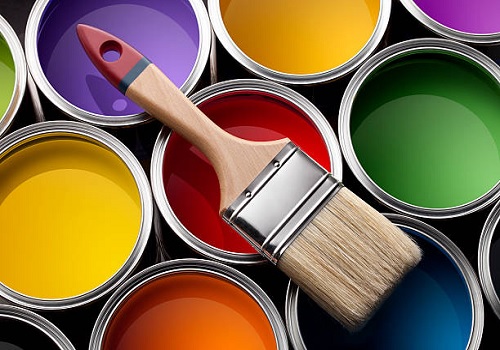
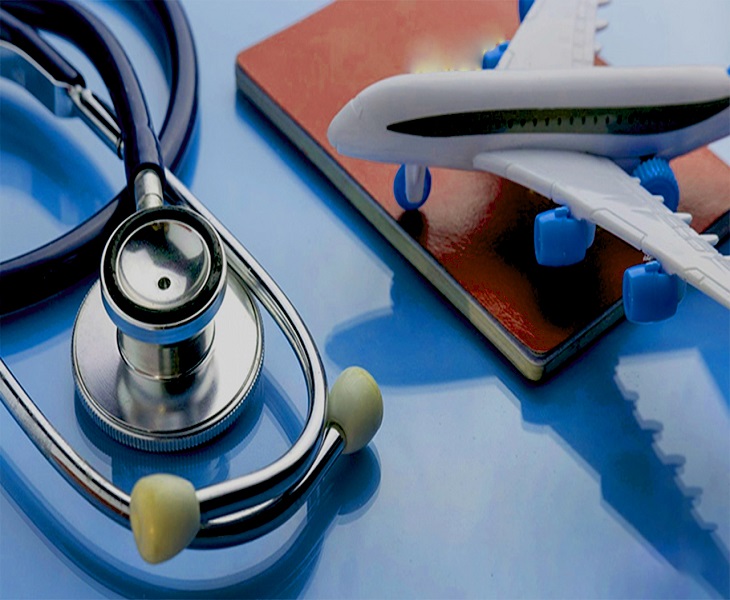
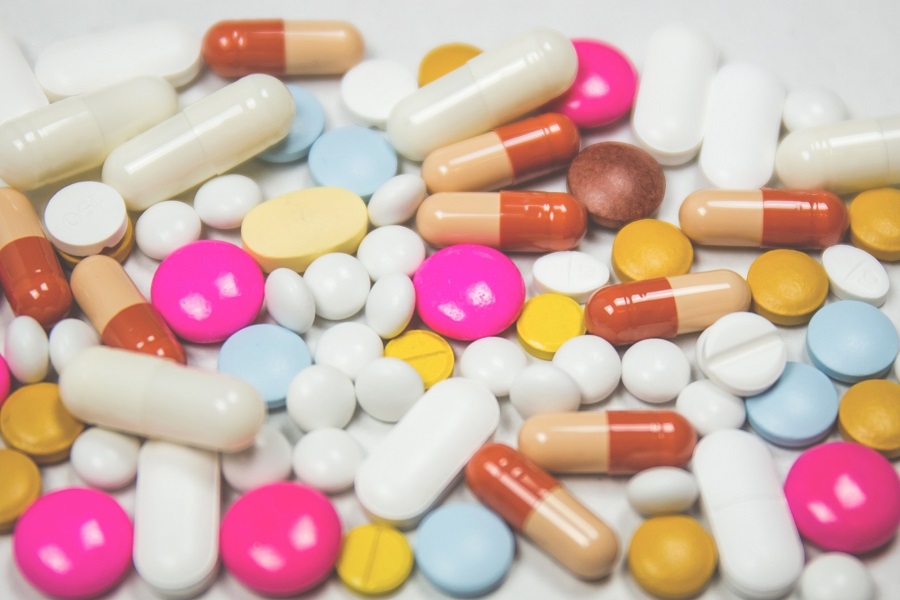
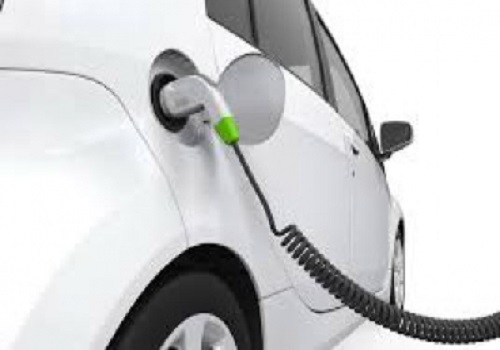
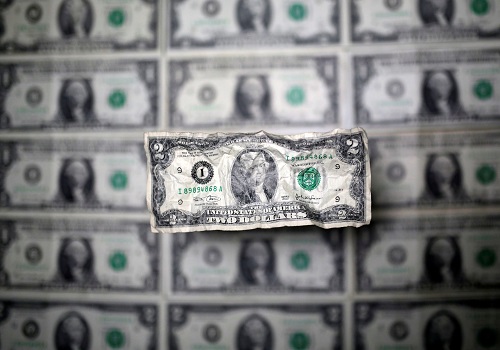