Clean Science and Technology coming with an IPO to raise Rs 1582 crore
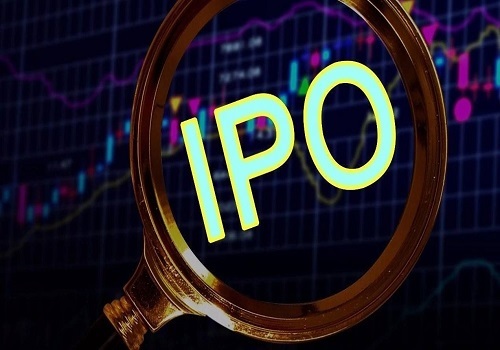
Clean Science and Technology
-
Clean Science and Technology is coming out with a 100% book building; initial public offering (IPO) of 1,75,75,245 shares of Rs 10 each in a price band Rs 880-900 per equity share.
-
Not more than 50% of the issue will be allocated to Qualified Institutional Buyers (QIBs), including 5% to the mutual funds. Further, not less than 15% of the issue will be available for the non-institutional bidders and the remaining 35% for the retail investors.
-
The issue will open for subscription on July 7, 2021 and will close on July 9, 2021.
-
The shares will be listed on BSE as well as NSE.
-
The face value of the share is Rs 10 and is priced 88 times of its face value on the lower side and 90 times on the higher side.
-
Book running lead managers to the issue are Axis Capital, JM Financial and Kotak Mahindra Capital Company.
-
Compliance Officer for the issue is Mahesh Arvind Kulkarni.
Profile of the company
The company is among the few companies globally focused entirely on developing newer technologies using in-house catalytic processes, which are eco-friendly and cost competitive. This has enabled company to emerge as the largest manufacturer globally of certain specialty chemicals in terms of installed manufacturing capacities as of March 31, 2021. The company’s continued focus on product identification, process innovation, catalyst development, significant scale of operations as well as its measures towards strategic backward integration have all contributed to its success as one of the fastest growing and among the most profitable specialty chemical companies globally.
The company manufactures functionally critical specialty chemicals such as Performance Chemicals (i.e. MEHQ, BHA and AP), Pharmaceutical Intermediates (i.e. Guaiacol and DCC), and FMCG Chemicals (i.e. 4-MAP and Anisole). Within 17 years of incorporation, it has grown to be the largest manufacturer globally of MEHQ, BHA, Anisole and 4-MAP, in terms of installed manufacturing capacities as of March 31, 2021. The company’s specialty chemicals have a wide range of applications that cater to a diverse base of customers across industries. Its customers include manufacturers and distributors in India as well as other regulated international markets including China, Europe, the United States of America, Taiwan, Korea, and Japan. In Fiscal 2021, revenue from operations for sales outside India represented 67.86% of its total revenue from operations, respectively. It has two certified production facilities in India strategically located at Kurkumbh (Maharashtra), in close proximity to the JNPT port from where it exports majority of its products.
Proceed is being used for:
-
Making an offer for sale of equity shares aggregating to Rs 1,5466.22 million.
-
Achieving the share listing benefits on the BSE and NSE.
Industry overview
The Indian Pharmaceuticals market was valued at $54 billion in 2019, contributing to around 4% of the global market. The Indian market is expected to grow at around CAGR of 10% between 2019 and 2025, fuelled by a substantial increase in Indian API domestic consumption. In addition, the government is also taking various initiatives to boost the industry, such as allocating land in different states to develop API Mega Parks, increasing investment in R&D, etc. Of the total domestic API demand, about 32–35% was imported in 2019. Of the overall imports, 57-60% of the imported APIs originate from China alone. Countries such as Italy, Germany, Malaysia and others are the other countries of origin. These facts suggest that the domestic API market has enough potential to expand if manufacturers are willing to self-produce the required quantity of APIs instead of importing them. The Government of India announced a Rs 99.40 billion package to boost the domestic API manufacturing industry. The package is divided into two parts; (i) Rs 69.40 billion has been allocated for the PLI Scheme and (ii) Rs 30.00 billion will be spent on setting up three bulk drug parks. Out of the total allocation of Rs 69.40 billion for the PLI Scheme, Rs 46.00 billion will be earmarked for fermentation-based products and Rs 23.40 billion for chemical synthesis products.
The Indian cough syrup market was valued at $711 million in 2019 accounting for 17% of global demand. The Indian market is expected to grow at a CAGR of 11.2% to reach $1.4 billion by 2025. Cough, cold and flu formulations have a large share of the pharmaceutical market in India, mainly because of self-medication. India is the fifth most polluted country (2019), by IQAir (a company that primarily works on air filtration). Air pollution is leading to chest congestion which is one of the most important public health issues in the country. With a growing number of chronic cough cases coupled with rapidly growing elderly population and rising vehicle pollution, the demand for cough remedy products is expected to increase.
Pros and strengths
Track record of strategic process innovation through consistent R&D initiatives: The company is among the leading companies in India to have commercialized use of environment-friendly processes to manufacture certain specialty chemicals, at global capacities. It has achieved this position by optimizing use of conventional raw materials, improving atom economy, enhancing yields, reducing effluent discharge, and consequently increasing cost competitiveness. Based on the technical expertise it has developed over the years, it is able to carry out these processes at global scale capacities, which is difficult to replicate, and create significant barriers for new entrants. It has developed these technologies through process innovation and consistent R&D. Various catalysts have been developed in-house through R&D, which are used across process developments, and have helped improve productivity, yields, atom economy and cost efficiencies.
Strong and long-standing relationships with key customers: The company’s customers comprise direct end-use manufacturers as well as institutional distributors. A majority of its revenues is generated from direct sales to customers. Certain of its key customers include Bayer AG and SRF for agro-chemical products, Gennex Laboratories for pharmaceutical intermediates, and Vinati Organics for specialty monomer products, Nutriad International NV for animal nutrition. Some of its customers have also been associated with it for over 10 years as of May 31, 2021. Its products are used as key starting level materials, as inhibitors, or additives by its customers for their finished products, for sale in regulated markets. Its customer engagements are therefore dependent on delivering quality products consistently, and it could take potential customers few years to approve it as suppliers, based on quality control systems and product approvals across jurisdictions by multiple regulators. Due to the resources involved in engaging with new suppliers, customers are less inclined to pursue alternate supply sources. This provides company with an advantage over new entrants that would need to make significant investments and endure a long gestation period with potential customers in order to effectively compete.
Automated manufacturing facilities with proven design and commercialization capabilities: The company has two manufacturing facilities in India with 11 production lines (including three lines for catalyst production and regeneration), which had a combined installed capacity of 29,900 MTPA as of March 31, 2021. It has recently set-up a unit at its third manufacturing facility. As majority of its sales are through exports, both facilities are strategically located at Kurkumbh (Maharashtra), which is in close proximity to the JNPT port. With dedicated production lines for its key products, it aim to limit losses and capacity reductions that are typically incurred during transitioning between products. It also has multiple lines across separate units for its key products to limit contagion risk, and consistently meet the demand for these products. Each facility is equipped to function independently, with its own quality department, effluent treatment plant, warehouse, and R&D unit.
Among the largest producers globally of functionally critical specialty chemicals used across various industries: The company’s specialty chemicals have a wide range of applications and its key raw materials are abundantly available resulting in a significantly de-risked business model. Its products are used as polymerization inhibitors, intermediates for agrochemicals and pharmaceuticals, anti-oxidants, UV blockers, and anti-retroviral reagents, which are functionally critical in a wide range of industries, including in the manufacture of paints and inks, agro-chemicals, pharmaceuticals, flavours and fragrance, food and animal nutrition (feed), and personal care (cosmetics) products. Its customers comprise manufacturers in India and other regulated international markets including China, Canada, Europe, the United States of America, Taiwan, Korea, and Japan.
Risks and concerns
Operations depends on R&D capabilities: The company’s competitive position in the specialty chemicals industry is primarily characterised by cost-efficiencies and R&D improvements. Its ability to continue to design catalytic processes is a significant factor in its ability to remain competitive. This depends on a variety of factors, including meeting development, production, certification and regulatory approval schedules; successful development and application of catalytic-technologies; captive production of key raw materials; hiring and training of qualified personnel; identification of emerging regulatory and technological trends in its target end markets; and the level of demand for new products. There can be no assurance that it will be able to secure the necessary technological knowledge through its own R&D or external sources, such as technical assistance agreements or strategic acquisitions, that will allow it to continue to develop its product portfolio or that it will be able to respond to industry trends by developing and offering cost effective products.
Depend on success of relationships with customers: The company has developed strong and long-term relationships with various multinational corporations that helped it expand its product offerings and geographic reach. Accordingly, it is dependent on its arrangements with such corporations and its business depends on the continuity of its relationship with these customers. It is dependent on a limited number of customers for a significant portion of its revenues. There can be no assurance that its significant customers in the past will continue to place similar orders with it in the future. Its reliance on a select group of customers may also constrain its ability to negotiate its arrangements, which may have an impact on its profit margins and financial performance. The deterioration of the financial condition or business prospects of these customers could reduce their requirement of its products and result in a significant decrease in the revenues it derive from these customers.
Significant proportion of revenues derived from sale of MEHQ: The company derive majority of its revenues from the sale of Monomethyl ether of hydroquinone (MEHQ), which is used as a polymerization inhibitor in acrylic acids, primarily involved in the manufacturing acrylic fibers, paints and inks, adhesives and super absorbent polymers. It also finds use in the agriculture industry. There can be no assurance that the lack of demand for MEHQ can be off-set by sales of its other products. Accordingly, any significant downturn in the industrial use of MEHQ could have a significant impact on business, financial condition and growth prospects.
Derive significant portion of revenues from operations from limited number of markets: The company has historically derived a significant portion of its revenues from operations from a limited number of markets, namely, China, India, Europe, and the Americas. Therefore, any developments in the global specialty chemical industry or the industries in which its customers operate could have an impact on its sales from exports. From time to time, tariffs, quotas and other tariff and non-tariff trade barriers may be imposed on its products in jurisdictions in which it operate or seek to sell its products. There can be no assurance that China, the European Union and the United States, among others, where it seek to sell its products will not impose trade restrictions on it in future. It may also be prohibited from exporting to certain restricted countries that may be added to a sanctions list maintained by the Government of India or other foreign governments, such as the Specially Designated Nationals and Blocked Persons list maintained by the Office of Foreign Assets Control of the US Department of Treasury in the United States. Any such imposition of trade barriers may have an adverse effect on its results of operations and financial condition.
Outlook
Incorporated in 2003, Clean Science and Technology is one of the leading chemical manufacturers globally. It manufactures functionally critical specialty chemicals such as Performance Chemicals (MEHQ, BHA, and AP), Pharmaceutical Intermediates (Guaiacol and DCC), and FMCG Chemicals (4-MAP and Anisole). Its specialty chemicals have a wide range of applications that cater to a diverse base of customers across industries. Its products are used as key starting level materials, as inhibitors, or as additives, by customers, for products sold in regulated markets. It has two manufacturing facilities in India with 11 production lines (including three lines for catalyst production and regeneration), which had a combined installed capacity of 29,900 MTPA as of March 31, 2021. It has recently set-up a unit at its third manufacturing facility. As majority of its sales are through exports, both facilities are strategically located at Kurkumbh (Maharashtra), which is in close proximity to the JNPT port. On the concern side, the specialty chemicals industry requires a substantial amount of capital and the company will continue to incur significant expenditure in maintaining and growing its existing infrastructure, purchase equipment and develop and implement new technologies in its new and existing manufacturing facilities. Adverse geopolitical conditions such as increased tensions between India and China resulting in any military conflict in the region could adversely affect its business and operations. Such events may lead to countries imposing restrictions on the import or export of products or raw materials, among others, and could either affect its ability to supply its products to China or to procure raw materials required for its manufacturing operations from China.
The issue has been offered in a price band of Rs 880-900 per equity share. The aggregate size of the offer is around Rs 1546.62 crore to Rs 1581.77 crore based on lower and upper price band respectively. On performance front, total income increased by 25.08% from Rs 4,301.65 million in Fiscal 2020 to Rs 5,380.71 million in Fiscal 2021 primarily on account of an increase in revenue from operations. The company’s restated profit increased by 42.07% from Rs 1,396.31 million in Fiscal 2020 to Rs 1,983.80 million in Fiscal 2021. The company also intends to capitalize on the growing demand for its products by expanding its manufacturing capacities and strengthening its distribution network in existing markets and gaining access to newer markets. To expand its product portfolio, it seeks to identify products with high demand that only limited manufacturers produce within India and globally. It also intends to continue to explore high margin downstream product lines, which have low competition and multiple applications.



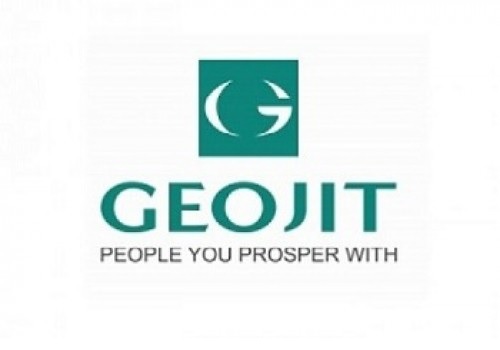
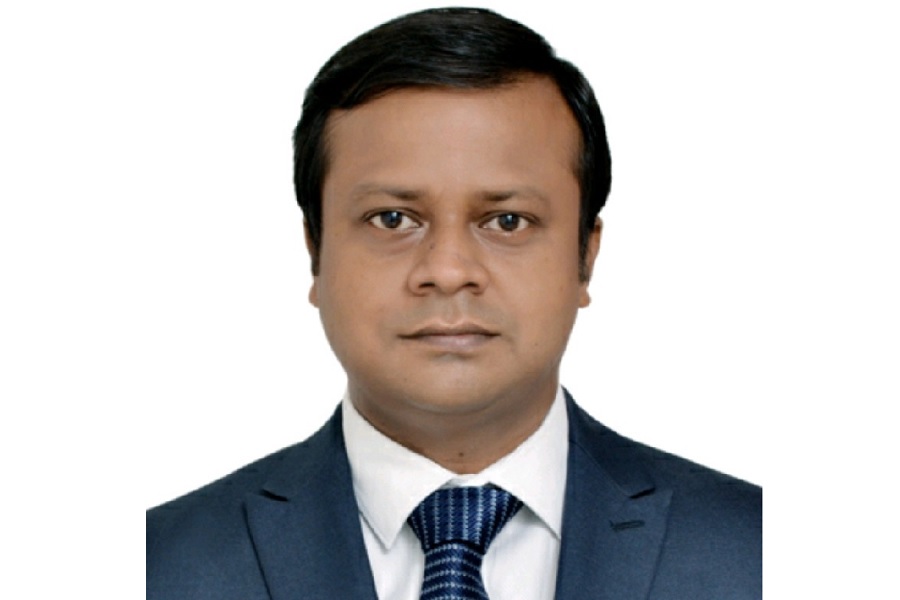
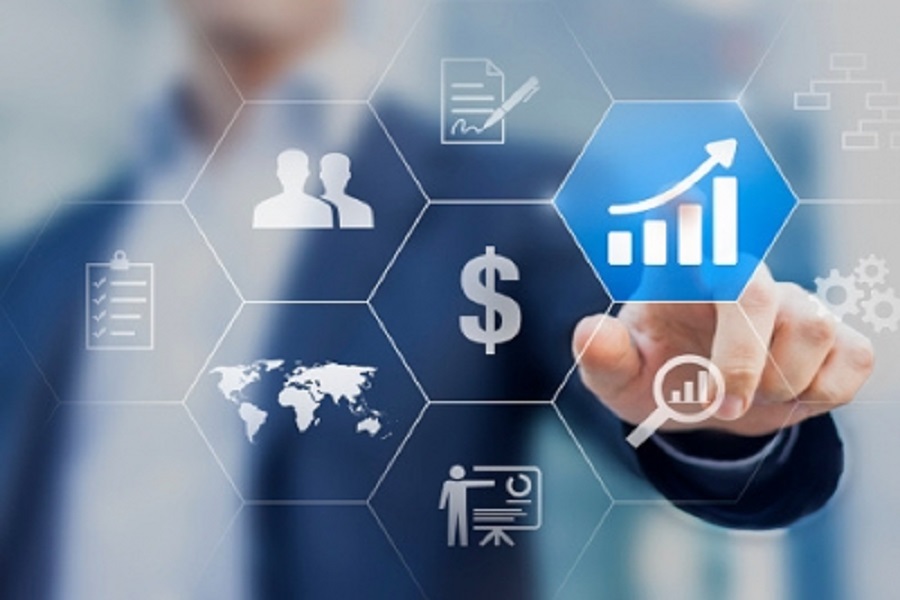
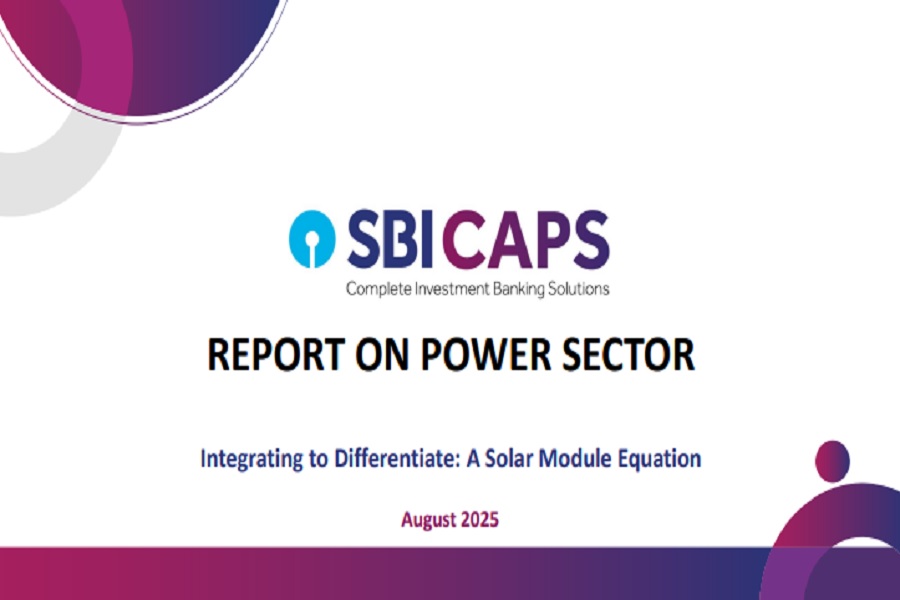
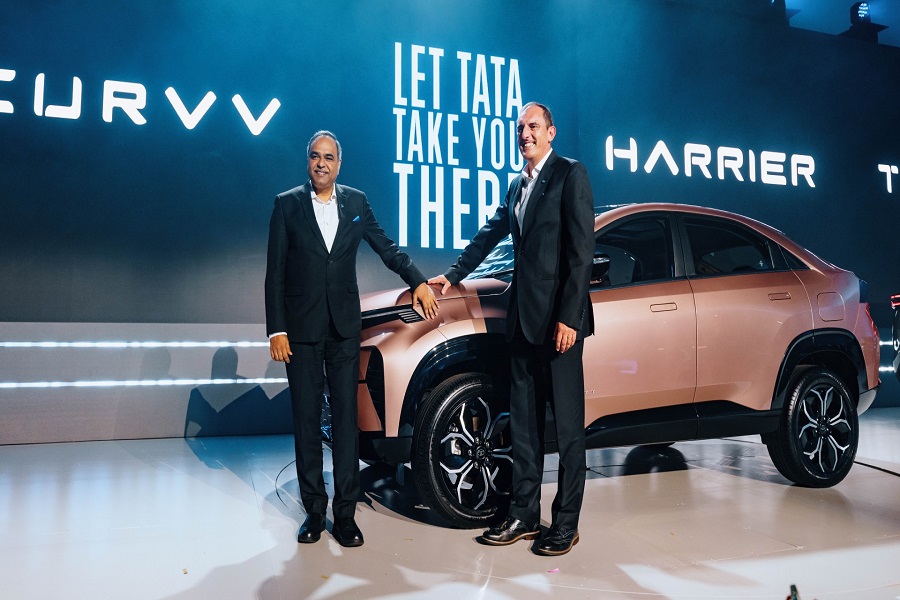
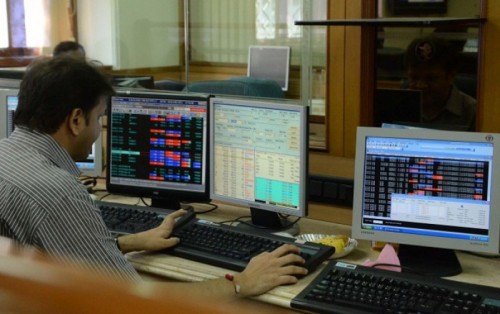
