No Record Found
Latest News
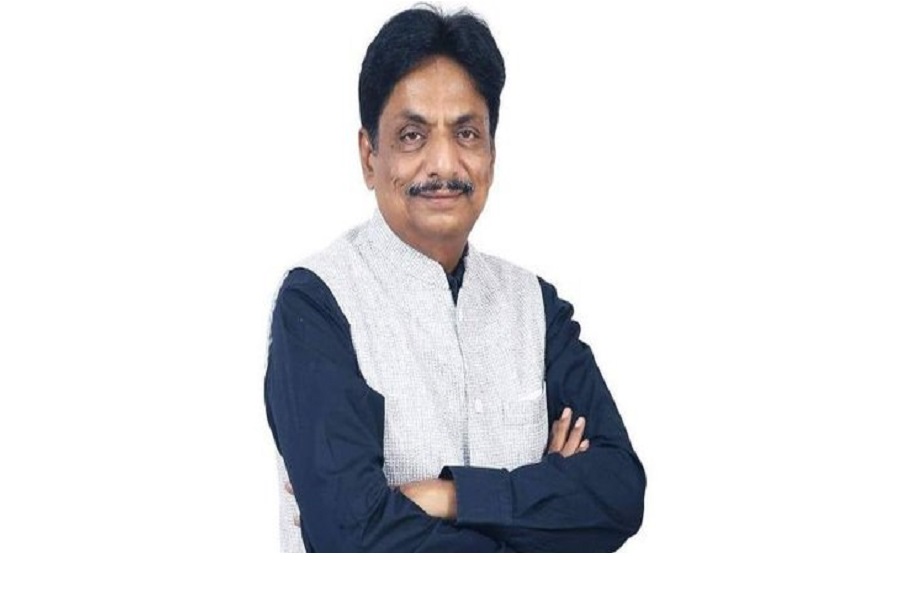
Gujarat: State budget earmarks Rs 15 crore for judic...
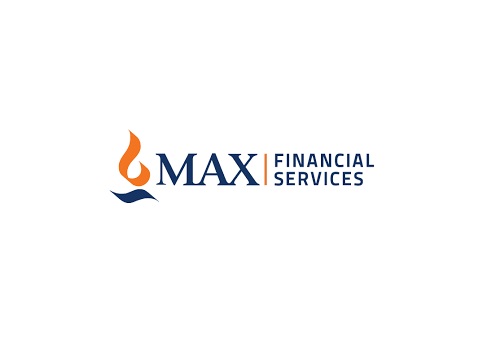
Buy Max Financial Services Ltd For Target Rs. 1,800 ...
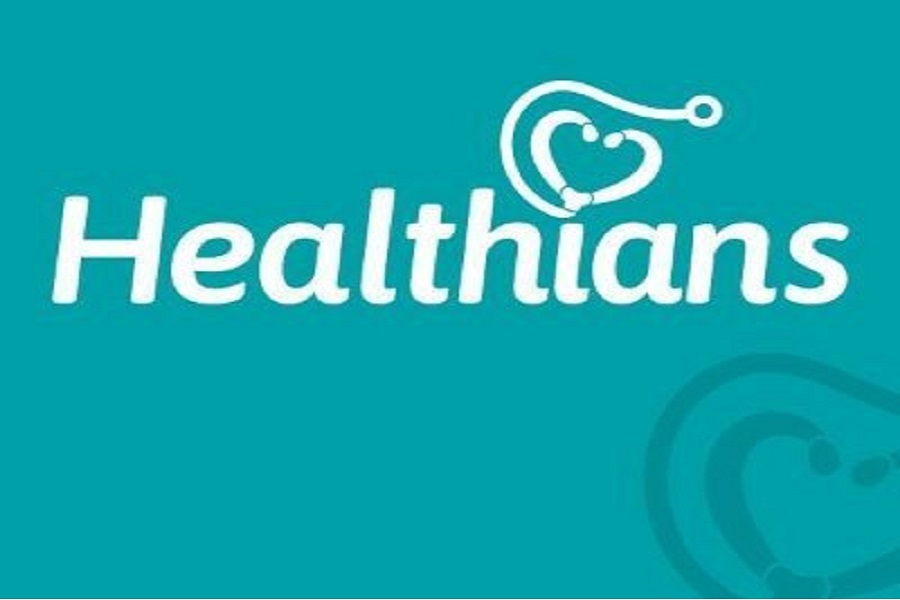
We lead with tech-driven, consumer-oriented services...
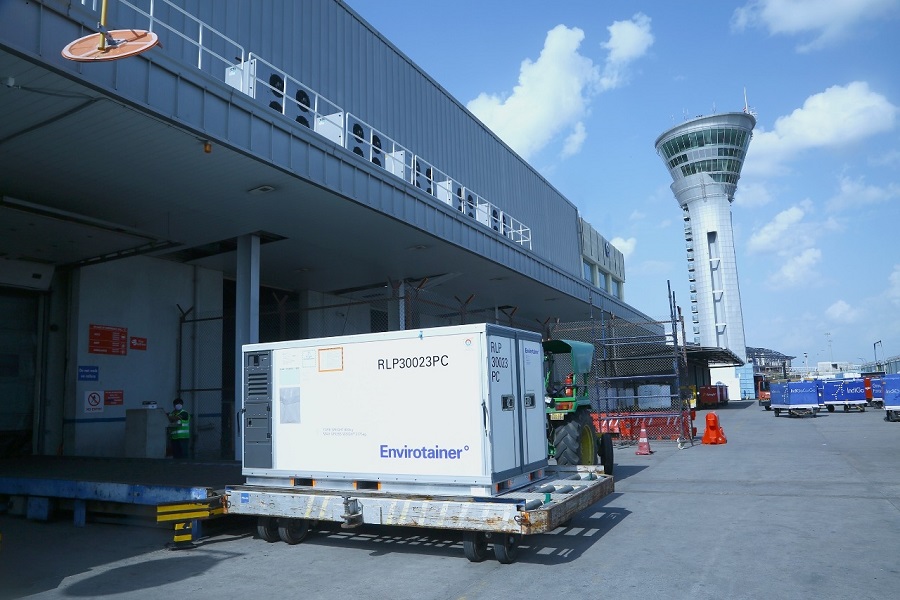
Air cargo industry shows resilience amid global chal...
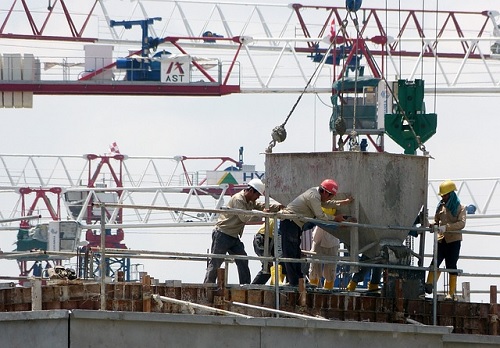
Building Materials Sector Update : Tepid quarter By ...
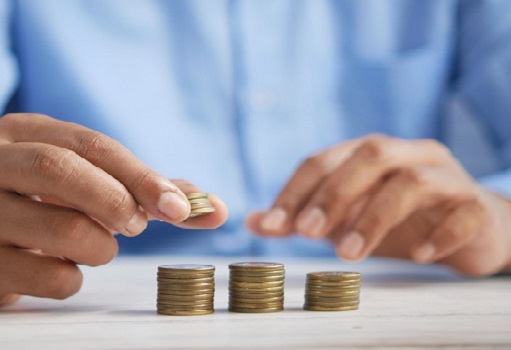
Asset and Wealth Management Sector Update : 1QFY26 P...
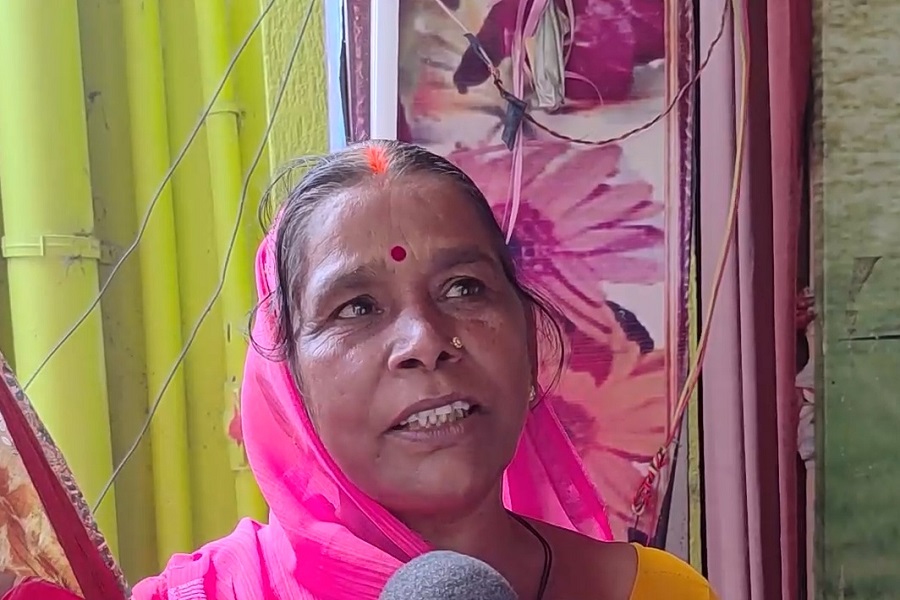
Bihar: Enhanced Rs 1,100 pension credited into bank ...
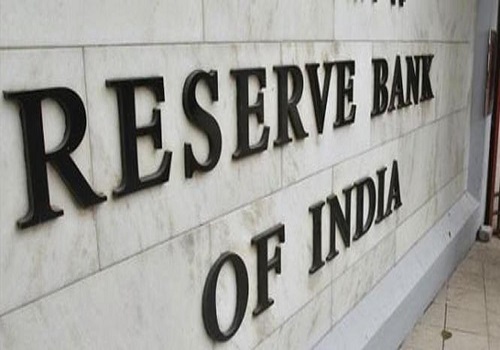
India`s gold reserves rise by $342 million, forex st...
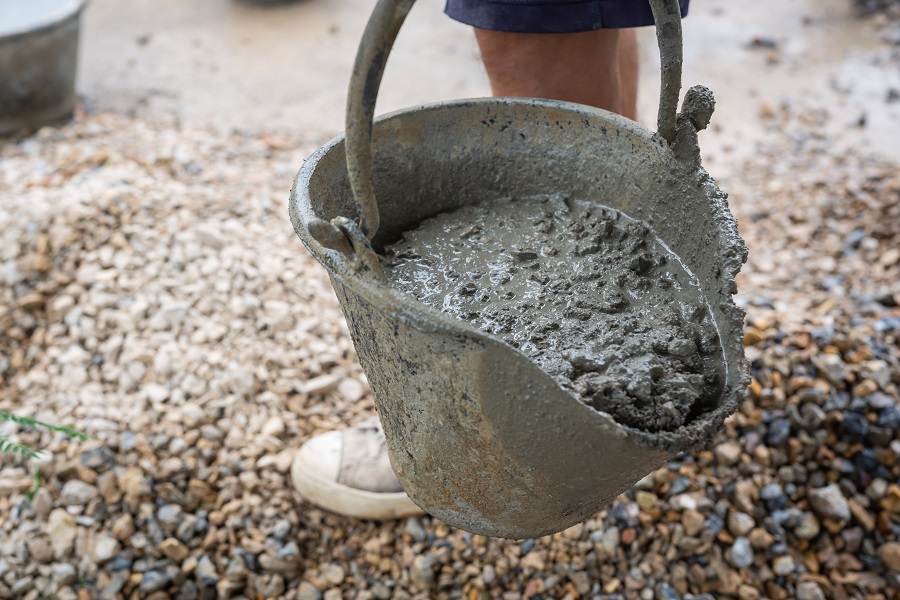
Cement Sector Update : 1QFY26 Preview: Price-led mar...
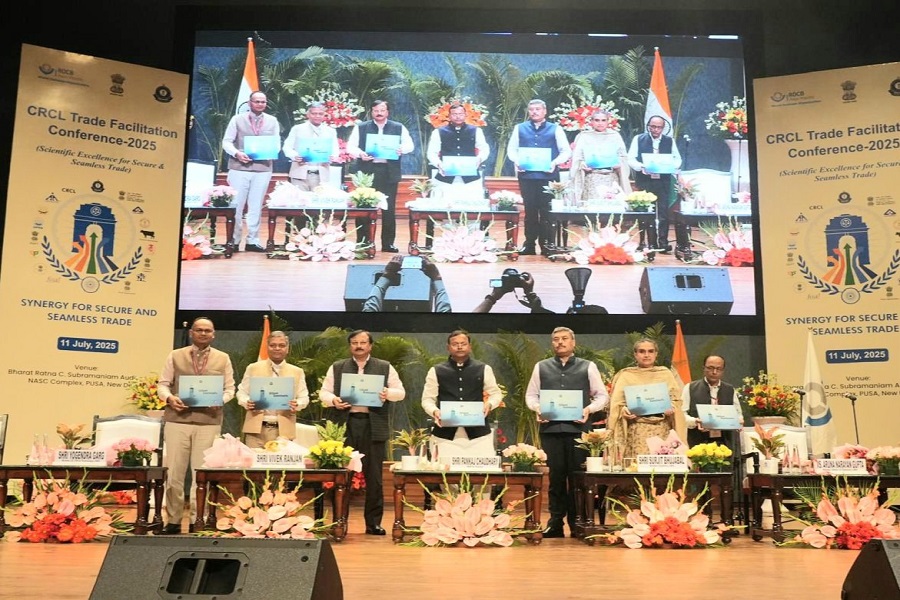
Centre to build modern and efficient testing framewo...
Top News
News Not Found
Tag News
News Not Found
More News
News Not Found